论文|国外新型高速动车组技术现状与发展趋势
注:本文为期刊公众号简版,完整版已发群内自取。
张波,中国铁道科学研究院集团有限公司机车车辆研究所
高翔,中国铁道科学研究院集团有限公司机车车辆研究所
黄金,中国铁道科学研究院集团有限公司机车车辆研究所
陈波,中国铁道科学研究院集团有限公司机车车辆研究所

0 引言
高速铁路作为铁路运输现代化的龙头,是铁路行业技术发展水平的综合体现。近年来,得益于技术创新和需求提升的双重驱动,全球高速铁路行业面临巨大的发展机遇。德国、法国、日本等传统高铁强国纷纷推出新一代高速列车产品,其产品各具特点且采用了许多世界领先的优势技术。面对激烈的国际竞争,我国明确提出“交通强国建设”要求,将轨道交通提到战略性高度,并做出“推动时速400公里级高速铁路关键技术研发”的部署。因此,亟需对国外技术发展趋势进行总结,并结合当前我国铁路发展实际需求,对高速动车组技术发展方向提出建议,加快轨道交通行业创新突破,为推动我国铁路行业高质量发展提供支撑。
1 德国
德国最具代表性的高速动车组是城际特快列车(InterCity Express,ICE)。1988年,ICE-V试验列车研发成功;此后,德国逐渐形成以ICE1、ICE2、ICE3、ICE4为代表的系列高速动车组。ICE系列高速动车组均由西门子公司制造,其中ICE1、ICE2采用动力集中方式设计,ICE3首次采用动力分散方式设计以适应高速运行。
目前,运营中的最新一代ICE主力车型为ICE4,其在减自质量、降成本、环保、舒适性等方面提出了较高要求;Velaro Novo则是西门子公司正在研发中的新一代动车组技术平台,以降低全生命周期成本、轻量化、增加定员为目标。ICE4与Velaro Novo的设计理念不仅反映德国铁路股份公司(Deutsche BahnAG,DB)作为运营商对动车组性能的需求,也反映西门子公司作为一个主机制造企业对未来车型的思考,具有一定代表性。
1.1 ICE 4
ICE4是西门子公司为DB开发,用于逐步替换ICE1、ICE2的新一代动车组(见图1)。其中,12节编组的动车组于2017年12月投入使用;7节编组的动车组于2020年12月交付。ICE4在DB内部的定型编号为412型,其主要特点如下。
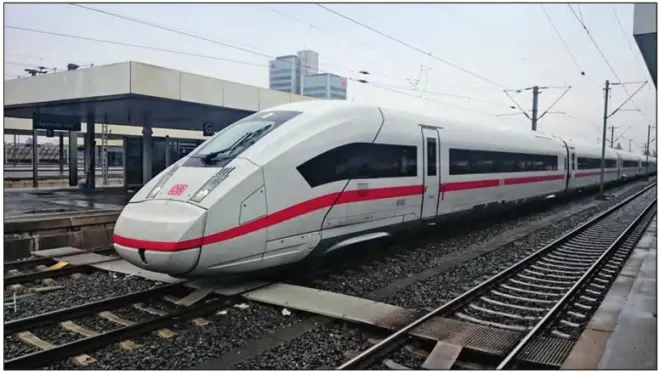
【灵活可变编组】
ICE4实现了在一个技术平台下的灵活可变编组,以适应不同加速度、速度、定员要求的乘客运输任务。ICE4可实现5~14节的任意组合,最高运行速度达280km/h。其中,7节和12节编组为基本型,最高运行速度分别为230km/h和250km/h,2列7节编组动车组可实现重联运行。ICE4主要技术参数见表1。

【创新驱力方案】
ICE4的牵引系统采用“动力包”的创新驱力方案开展模块化和集成化设计(见图2),1个牵引单元的主要部件包括变压器、冷却设备、变流器、牵引电机等,均集成于1辆动力车并安装于车厢下方。该系统由西门子公司和庞巴迪公司联合开发,通过改变列车编组中动力车的数量和动拖车比例,即可改变整车的牵引功率,实现不同速度等级运行,保证列车编组的高度灵活性。
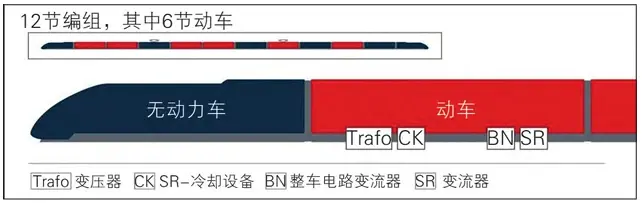
【SIBAS PN】
SIBAS PN是西门子公司继SIBAS 16、SIBAS 32之后研发的第3代产品。其中,SIBAS为西门子铁路自动化系统,PN为用于通信控制技术的Profinet协议。
SIBAS PN的通信网络由列车网络ETB列车总线和车厢网络总线Profinet构成,2种网络均基于快速以太网(100Mbits/交换以太网),效率高、冗余足。各个车辆具有单独的控制单元,保证了车辆独立性。借助SIBAS PN,ICE4的头车可对编组内任意1节车厢进行单独控制。该架构可允许替换编组内的任意车辆,是实现动车组灵活编组的基础。SIBASPN结构见图3。
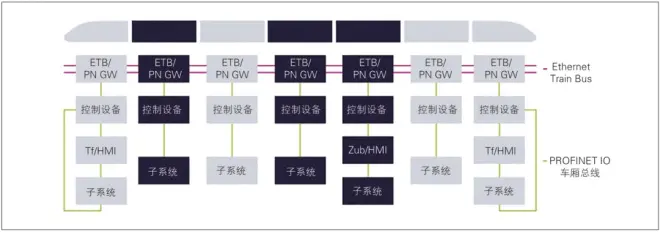
【长车体设计】
ICE4动车组采用28m长的车体,比传统ICEVe⁃laro增加了3m。与常规8节编组200m长的列车相比,ICE4可减少1节车厢,从而减少通过台、车下设备和转向架的数量,增加了座位和可用空间,且有利于牵引系统集成。同时,动车组的整个乘客区采用模块化布局,可随意改变配置。车厢内减少了电气柜,进一步增大可使用空间。所有内饰均采用模块化设计,座位安装于地板滑轨,运营商可针对需求快速作出调整。
【舒适性优化】
ICE4在服务车厢内为带小孩乘客辟出家庭区域,为自行车爱好者预留存放区域;新研发座椅经人体工程学设计,提高了乘坐舒适度;车厢采用大型全景车窗(1924mm×780mm),确保良好采光;内部照明系统的颜色和亮度可根据季节、昼夜变化自动调节,匹配自然光变化;为方便行动受限人士出行,多功能车厢提供轮椅区域,该区域位置紧邻轮椅升降机和通用宽敞洗手间,地板配备触敏引导系统,以帮助盲人或视障乘客。
【动力转向架】
ICE4的动力转向架是西门子公司在SF500基础上设计的(见图4),优化了质量,可满足对轴承负载和牵引力的较高要求。拖车转向架基于庞巴迪FLEXXEco转向架技术,针对高速运输进行了优化。拖车转向架的特点在于轴承内置化,即轴承和框架部件位于轮对的轮盘内。该结构大大降低了车体质量、减小了相关部件尺寸,与ICE3相比,7节编组的ICE4动车组质量降低约20t。受益于轻量化设计和改善的车体空气动力学性能,ICE4动车组能耗明显降低,与ICE1、ICE3相比,能耗分别降低22%、15%。
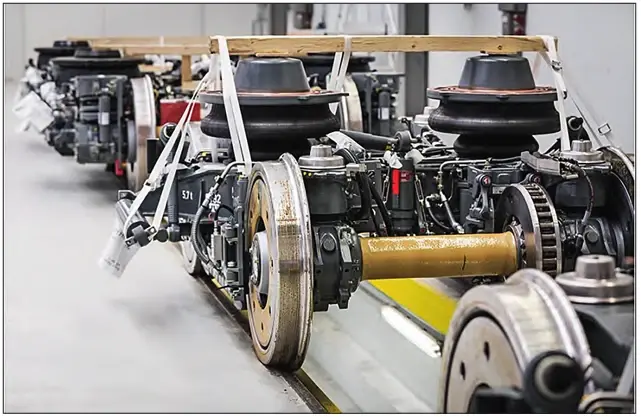
1.2 Velaro Novo
Velaro Novo是西门子公司Velaro技术平台最新一代的高速动车组(见图5)。2012年开始研发,预计2023年商用。目前,西门子公司已制造了1辆样车,编组在德铁的ICE综合检测列车中进行相关测试。
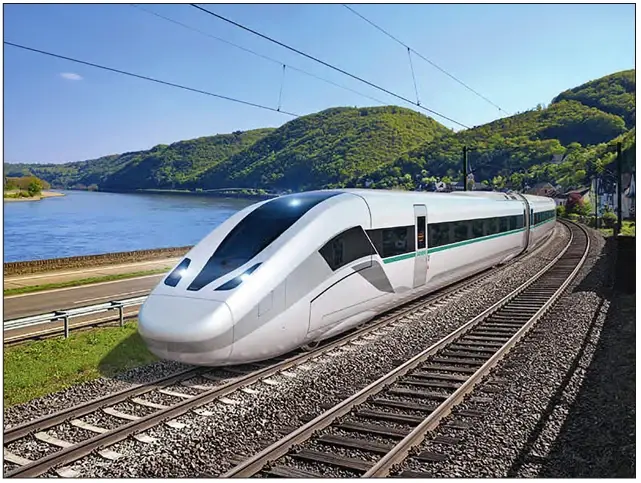
Velaro Novo继承了ICE4的设计理念,通过同一个平台内的不同配置,以适应280~360km/h不同速度等级的要求,并且提出了更高的顶层指标(见表2)。
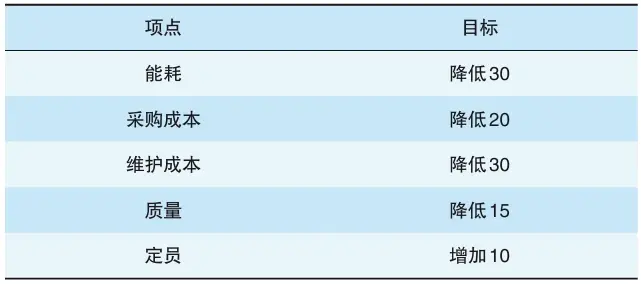
Velaro Novo特点之一是进行了大量的空气动力学优化工作,通过车顶平顺化、受电弓下沉、高压器件部分进入高压箱等措施,实现整车能耗降低10%。动车转向架和拖车转向架均采用轴箱内置式方案,并通过全包转向架,实现整车能耗降低15%。
Velaro Novo牵引、辅助变流器采用碳化硅器件,牵引电机采用永磁电机,在降低质量的同时,提高牵引系统效率,实现整车能耗降低5%。
制动系统采用全新优化方案:(1)未配置轮盘制动,为实现高速下紧急制动性能要求,增加了踏面制动;(2)充分发挥永磁电机优势,结合再生制动、电阻制动,电制动功率可达牵引功率的1.5倍,在正常运营情况下实现全速度范围内电制动,大幅减少闸片磨耗。其中,电阻制动布置于车顶,仅用于常用制动的补充。
为提高定员,Velaro Novo一方面将车长增至29m,另一方面在车体上实现了“空管”概念,电气柜小型化,布置于车顶和端墙,释放出更多车内空间(见图6)。另外,通过内装型材和布局优化,使列车在车体变窄的条件下,车内可用空间反而增加(见图7)。
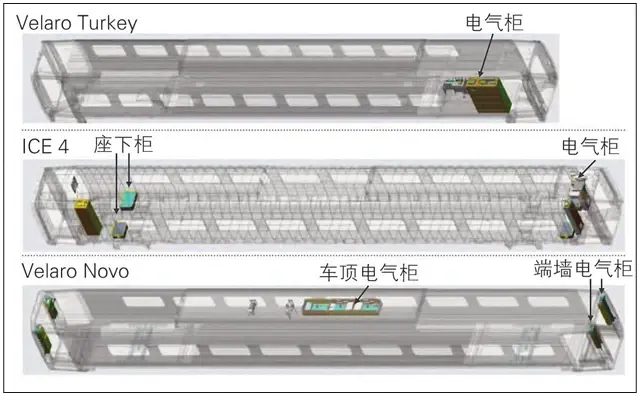
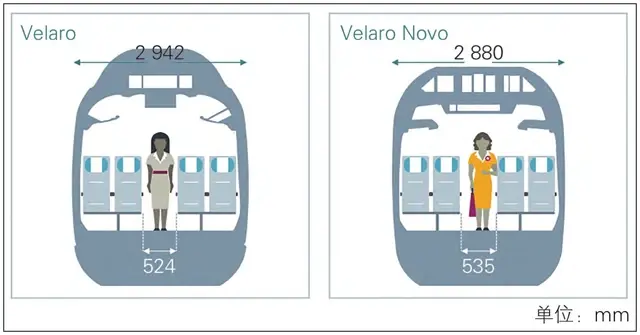
2 法国
法国自1978年制造出第1列TGV高速列车以来,至今已发展到了第4代。法国最新1代列车于2015年12月开始研发,该车型最早被阿尔斯通公司命名为“AveliaHorizon”,后被法国国营铁路公司(简称法铁)正式命名为TGV-M(见图8),“M”代表“现代”或“模块化”。根据计划,该车型于2023年起分期交付,取代自1996年起使用的TGV-DUPLEX双层列车。Avelia是阿尔斯通公司最新一代的高速列车技术平台,继承并发展了TGV和AGV系列高速列车的技术优势。
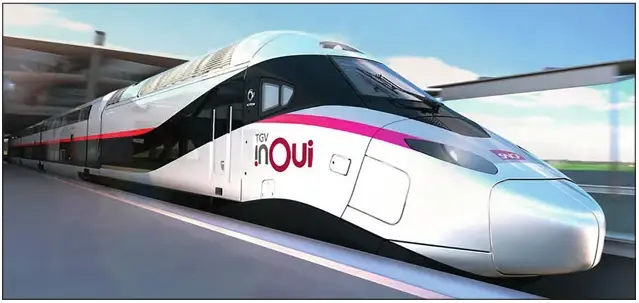
TGV-M动车组研发方向关注重点包括大载客量、低运营维护成本、环境友好、现代化乘客服务系统等,未采用AGV列车的中间动力转向架技术,而是采用双层铰接式动力集中设计。动力车采用紧凑型设计,可配备7~9节拖车,在2M9T编组条件下车长202m,使其在同样长度条件下增加了1节拖车。动车组全列采用轻量化设计,动力车和拖车轴重均不大于17t,其主要参数见表3。
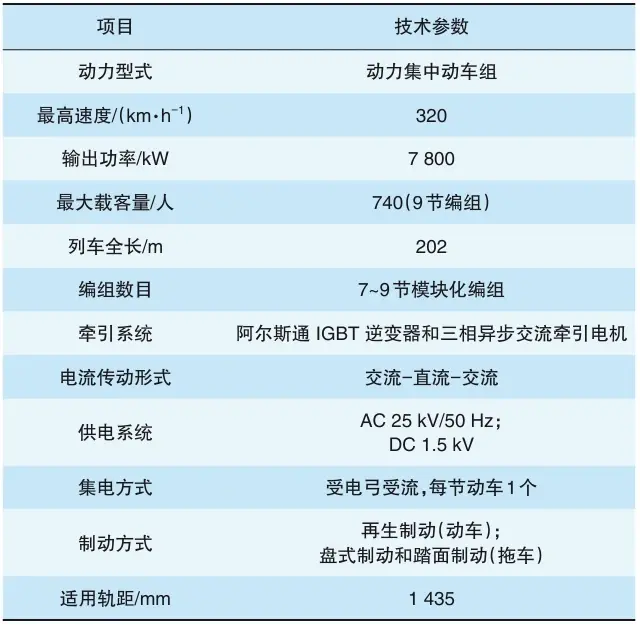
TGV-M最初计划用于法国国内线路,但其同时满足国际运营条件。通过适当改装,该列车可在荷兰、卢森堡、德国、瑞士、意大利、西班牙等国运营,其关键特点包括:
(1)节能、全生命周期成本低。TGV-M被法铁描述为历史上最环保的TGV,动车组能耗降低20%,碳排放量降低37%,可回收利用部件高达97%,列车采购成本降低20%、维修成本降低30%。
(2)采用模块化设计,可灵活编组数量和座椅布置。列车可根据需求,最大化调整车厢数量,头等车厢与二等车厢之间可实现重新配置等。
(3)改善乘车体验、优化客运服务。载客量增加约20%,可提供全面实时的行程信息,实现车内区域无障碍通行,方便乘客上下车等。
3 日本
日本是第一个开通高速铁路的国家,其高铁技术以新干线为代表,最高运营速度320km/h。日本拥有多达十几种高速列车型号,是列车种类最多的国家,全部采用动力分散形式。经过多年发展形成两大系列:(1)以百位数字表示的高速列车,从0系开始,发展出100系、200系、300系、400系、500系、700系、800系、N700系,最新车型为N700S;(2)E系高速列车,包括E1、E2、E3、E4、E5等型号。
日本铁路在发展中始终贯穿轻量化、节能环保、模块化设计、低维护成本等理念。为满足国内运营需求,新干线动车组对于质量、阻力、噪声、舒适性、安全性(特别是地震时)等指标有较高要求;同时,为保持新干线在与航空运输业的竞争中始终处于优势地位,日本铁路公司积极推动新型动车组研发,通过产品迭代,不断引入新技术,进一步提高舒适性和经济性。因此,日本动车组更新换代速度非常快,部分车型在退役时使用年限尚未达到25年。
3.1 N700S
N700S由日本JR东海铁路公司主导研制,2018年3月试运行,2020年7月投入运营。“N700S”取Su⁃preme首字母“S”,意为N700系的顶级车辆。该车型是继2013年推出N700A后,JR东海铁路公司研制的第6代新干线车辆,其主要参数见表4。
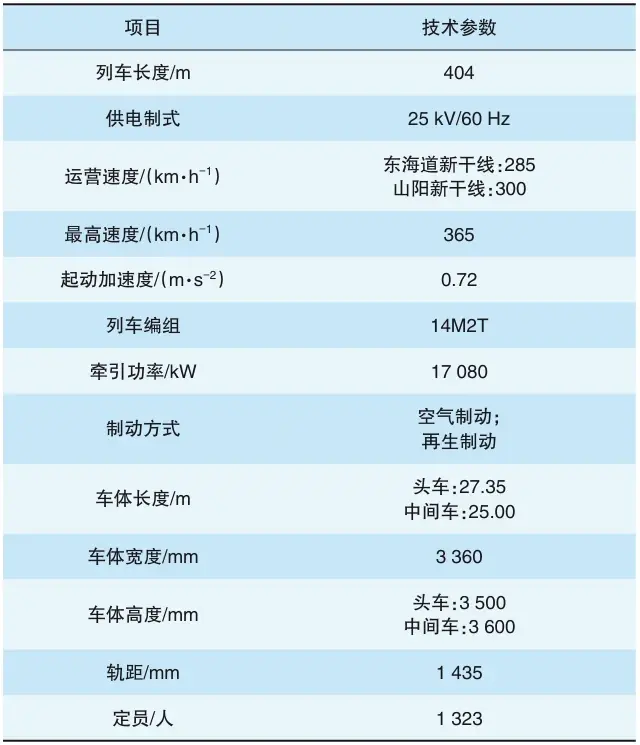
N700S设计沿用了N700系的外型风格,改进了空气动力学流线设计,采用长流线背鳍头型,车体更平滑,降低了隧道微气压波和车外噪声,减少了列车运行阻力和尾车摇晃。
N700S在轻量化和降低能耗方面比较突出,最大轴重11t,质量为700t。与N700A相比,整车质量降低13t,其轻量化设计项点见表5;能耗降低约6%(见图9)。
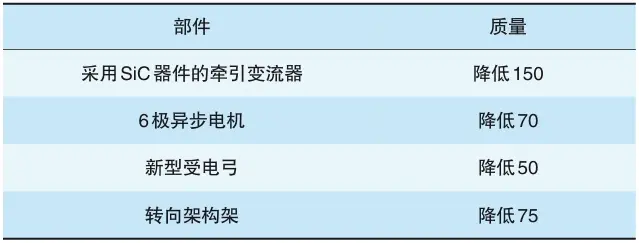
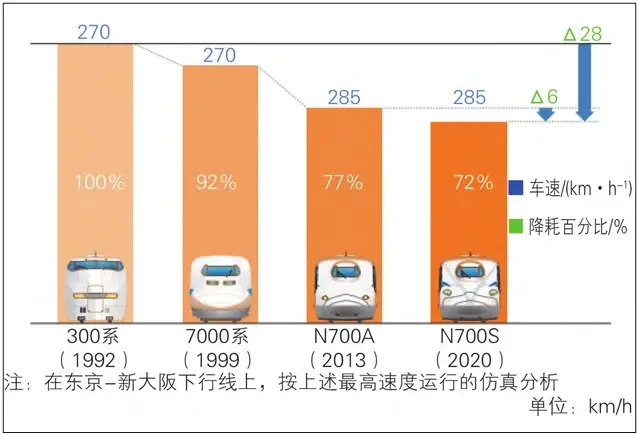
N700S主变流器采用半导体器件碳化硅(SiC),具有发热小、高速关断、高频率、低损耗等优点。结合自主研发的走行风冷却技术,主变流器大幅小型化和轻量化,能够与主变压器一起安装于同一型号车辆,可实现动车组车底设备的优化配置。牵引电机由4极增至6极,进一步小型化、轻量化。
N700S在设计中还提出“标准车辆”理念,通过设备的小型化、轻量化设计,合理配置地板下设备,按照是否安装主变压器来简化标准车辆结构,易于形成多种编组(见图10),车辆种类从8种减至4种,便于实现8节、12节、16节等多种编组形式,适应不同线路需求。
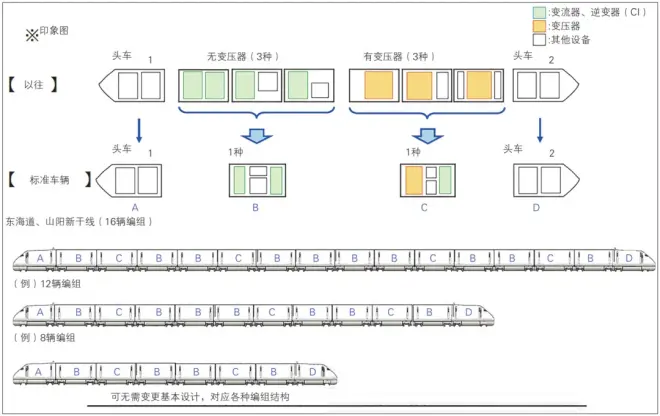
3.2 ALFA-X
ALFA-X是JR东日本公司主导,川崎公司和日立公司参与研制的用于测试前沿技术的高速试验列车,造价约合6亿人民币。该车型于2019年5月13日起开始为期3年的整车型式试验,计划以400km/h进行测试,后期运营速度为360km/h。
ALFA-X为10节编组全动力车,平均轴重12.4t,最大轴重13.1t。ALFA-X对整车空气动力学性能进行优化,采用超长前鼻,两端头车采用不同气动外形(见图11):1号车设计考虑抑制高速驶入隧道时的微气压波,长度约16m;10号车采用流线长度约22m的超长设计。
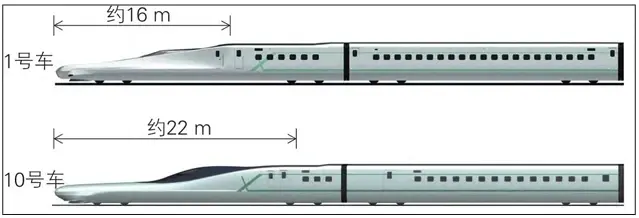
另外,对翼型受电弓整流罩进行优化,同时为提高列车抵抗积雪和适应低温环境的能力,在转向架上设置导流以减少积雪(见图12);舒适性方面,采用主动式悬挂与气动摆式机构;轻量化方面,采用SiC牵引变流器,并通过自然风冷方式减少冷却风机数量;可靠性方面,通过车载布置大量状态检测测点,实现列车健康管理和精准预防修,并搭载高效能电池用以实现应急牵引自走行。
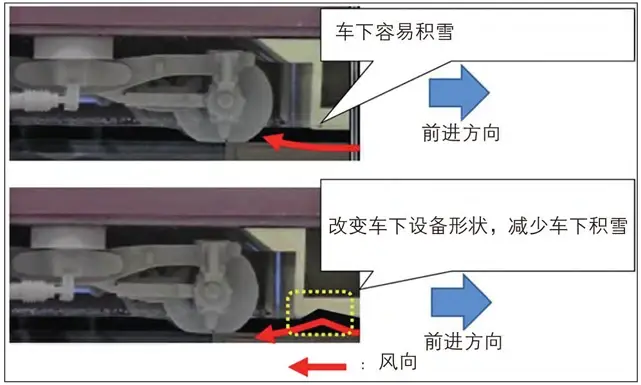
ALFA-X采用“地震-制动控制模式曲线”,可缩短地震时的制动距离。同时,在车顶设置“空气阻尼制动翼”作为风阻制动(见图13),在车底搭载线性涡流制动装置,仅在发生地震的紧急情况下使用。在初速360km/h时,紧急制动距离可大幅降至4300m(纯空气)和4000m(纯空气+风阻)。
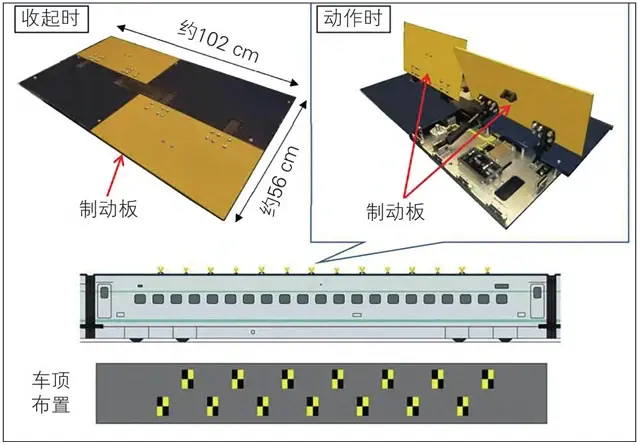
4 高速动车组技术发展趋势
(1)对更高速度的追求。速度是高速铁路区别于传统铁路的主要特征,更是高速铁路研究的核心内容。近年来,随着技术的创新与应用,世界各国铁路运营速度均有不同程度的提升,将新型高速动车组运营目标速度定为350km/h或360km/h,试验速度定为400km/h或更高,研究重点放在解决由速度提升造成的阻力、能耗、噪声加剧等问题。未来速度提升仍将是世界高速铁路发展的主要趋势。
(2)发展更注重经济性。经济性是铁路行业持续健康发展的基础。在保证安全可靠的基础上,综合考虑高速动车组的经济效益,实现研发、制造、运维各环节的全生命周期成本最优,有利于高速铁路高质量、高效益发展。同时,作为高铁运输系统中的主要耗能设备,动车组能耗对高铁运营成本也有重要影响。各国动车组将成本降低作为设计的主要目标之一,如Velaro Novo采用优化牵引传动系统、空气动力学优化等技术,使能耗降低30%;采用模块化设计、设备布置优化等措施,使整车采购成本降低20%、维护成本降低30%。
(3)灵活适应用户需求。为了达到吸引客流的效果,高速动车组乘坐舒适性也是技术发展考虑的重要因素之一。各国采取各种措施优化列车运行舒适度,如从人机工学角度,优化动车组内部结构,包括增大车窗、增加自动调节车内光线、温湿度和压力等装置;安装减振控制装置;为弱势群体提供更多便利,包括增设轮椅存放区域、专用卫生间、盲文识别等;车内设备小型化,进一步扩大乘客的可用空间,如Velaro Novo的“空管”结构设计等。
(4)智能化发展。智能化是未来铁道机车车辆的重要发展方向。近年来,德国、法国、日本等相继提出智能高铁发展战略,在列车控制、安全监测、乘客服务等方面开展系列创新实践。高速智能动车组以信息全方位感知、数据融合处理、科学决策为手段,采用物联网、云计算、大数据、人工智能、5G通信等先进技术,实现动车组自主感知、自动运行、自监控、自诊断、导向安全自决策、健康管理自保护等功能,可大幅提高动车组的安全性、经济性和舒适性。
5 我国高速动车组关键技术突破建议
(1)车体轻量化技术。相对于传统轨道车辆车体设计方法,轻量化设计能够降低能耗,提高动车组的运用经济性,代表了动车组工业设计的技术水平。
(2)降低气动阻力。动车组在高速运行时气动阻力随运行速度提升呈平方关系激增,因此,降低高速列车气动阻力是进一步提高动车组速度、降低能耗和噪声需要解决的关键问题。
(3)高效牵引传动技术。目前,牵引传动技术正在向大功率、高效率、轻量化、小体积、高可靠性和低成本方向发展。
(4)修程修制优化。目前,各国正逐步推动动车组从定期修向状态修转变,并研究智能化技术在动车组运维中的应用,希望通过故障预测与健康管理(PHM)技术,对动车组的状态进行预测,实现由预防修向预测修或状态修转变,减少过度维修,降低养护维修成本,不断提高状态修、经济修技术水平,从而降低成本。我国新型动车组的开发应更加注重修程修制正向设计,在产品设计阶段就统筹考虑制造成本和运维成本,合理确定可靠性指标,实现全生命周期成本(LCC)最优化。
(5)模块化设计与灵活配置。近年来,各国新研制的车型均引入“标准车辆”概念,在设计中采用模块化和高度灵活的设计理念。
6 结束语
综上所述,未来高速动车组将在综合考虑节能环保、安全舒适、经济性的前提下,追求运营速度的进一步提升。目前,世界高铁技术处于先进行列的国家均在持续开展技术的不断迭代,研制下一代高速动车组,国际高速铁路市场竞争日益激烈。这些新型装备在绿色环保、效率提升和智能运维方面均达到较高的技术水平,在创新理念和新技术等方面具有一定的参考借鉴意义。
近年来,我国铁路行业飞速发展,实现从追赶到引领的转变。持续推进高速铁路装备技术水平的发展,有利于提升我国科技创新能力和国际影响力,保持我国高铁技术领先优势,带动我国铁路行业产学研用创新体系完善和产业链持续健康发展,对于促进铁路高质量发展和率先实现铁路现代化具有重要战略意义。目前,面对竞争剧烈的国际市场,我国已启动时速400公里等级高速动车组研制工作,铁路行业应把握高速铁路的发展机遇,围绕着速度提升开展系列关键技术的研究与验证,为引领世界高速铁路发展奠定坚实的技术支撑。
来源:《中国铁路》编辑部