新能源汽车“着火”事故简析
概述:
国家应急管理部近日公布的数据显示: 2022年第一季度共接报新能源汽车火灾640起,比去年同期上升32%,平均每天达7起之多。笔者从部分电动车起火时的状态进行统计分析,发现电动车起火时处于非使用状态、行驶状态和充电过程中的起火比率相差不大,如下图表所示。笔者将对这三种状态下的起火原因做简单分析,并提供安全设计建议。
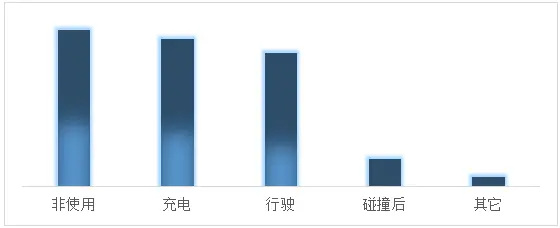
无论哪一种情况导致的电池着火或爆炸,根本原因都是电芯内部或外部的短路,致使电芯发生热失控,单个电芯发生热失控后,电池模组(包)结构设计如果不能避免发生热扩散,最终就会导致整个电池包发生着火。引起电芯内部或外部短路的原因有(不限于这些):过热、过充、过放、机械作用(挤压、撞击)、线路老化、电芯生产过程中的金属颗粒进入等。
当电芯接受到外界或自身产生的热量不能及时散热,电芯温度超过内部材质(隔膜)的温度时,隔膜收缩导致正负极接触短路;
经常性的过充会导致电芯内部产生析锂,锂金属枝晶式生长,最后刺穿隔膜,导致内部正负极短路;
当车辆发生碰撞时,电芯受到外力冲击,使隔膜扭曲变形及破损,致使发生内部短路;
外部线路连接电池包端子的线路老化,导致绝缘破损,产生外部短路引起过热。
电池包安全的两大关键部件:
要减少电池包的安全隐患,一是电芯的安全质量高,二是保护板的耐久性好;电芯的安全质量高主要指电芯的一致性好,电芯生产过程没有任何异物能进入卷芯;保护板的耐久性好主要指保护功能的循环寿命长,可靠性高。
电动车在非使用过程中发生着火的原因和电芯的安全质量有关,非使用过程中发生着火的起因可能还在使用过程中,只是当时还没有构成电芯的损坏引起着火,而是经过一段时间的自反应后使电芯彻底失控;电池充电过程中发生着火的原因可能是保护功能失效或电池包中的电芯电压出现不均衡,以及充电发热所致;车辆行驶过程和电芯的电压不均衡和发热未及时散热所致。
避免电池发生着火的措施:
1、制造过程优化:控制生产过程中的金属杂质、空气粉尘、极片毛刺等;
2、原材料优化:使用耐高温原材料,并对隔膜等材料优化,如使用陶瓷涂层或复合隔膜;
3、结构设计优化:电池组与相邻电池间可以加入隔离散热层,尽可能避免热扩散发生;
4、BMS要实行对每一个电芯的电压电流监控,增加故障诊断功能,在内短路发生的前期就排查识别出来,
避免安全事故的发生;
5、优化散热设计,使电池包在使用过程中产生的热量及时散发出去;
6、增设自动灭火功能,这可能不会完全把着火片扑灭,但可以减缓火势的蔓延。