案例 | 轩田科技提供功率半导体封装测试智能工厂最优解
随着工业4.0的到来,为了把握新一代发展机遇,建设一个自动组装、高效装配、智能检测、再配合自动派工、智能调度、透明化生产等功能的智能工厂,来实现工厂的智造升级,是大势所趋。
本文分享的是由轩田科技设计落地的先进全自动车规级IGBT模块封装测试智能工厂案例。
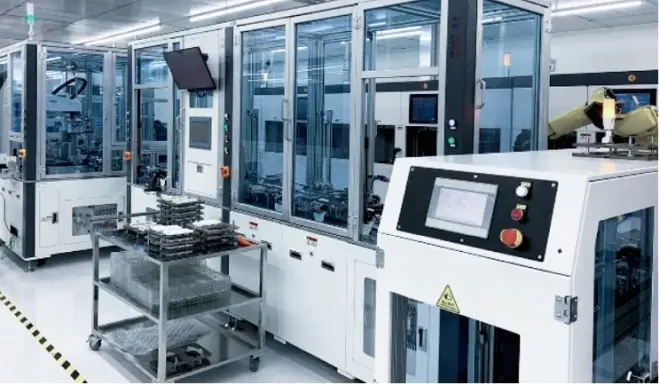
该智能工厂主要应用于IGBT模块的生产,通过顶层规划布局及多系统集成,打造了端到端的全自动生产能力,实现了包括产线及单元的布局、非标及标准设备的连接、物流仓储系统以及信息化系统的的规划和落地。
该项目是一个真正意义上的多学科多系统的复杂工程,是功率半导体行业智能工厂的完整解决方案。通过对每个环节的有效管理,实现规模化、柔性化生产。以产品制造过程全追溯,生产过程透明化,资源配置最优化为核心,将日常管理、精益生产与数字化融合,实现生产过程自动化、数字化及智能化,大幅降低出错率,提高产品合格率,缩短生产周期,满足客户预期的年产能。
01 项目背景
某半导体行业头部知名厂商,基于IGBT芯片及模块的广泛市场需求,决定建设全自动化IGBT模块封装测试智能工厂,实现IGBT模块的批量化产出、智能制造及柔性制造。
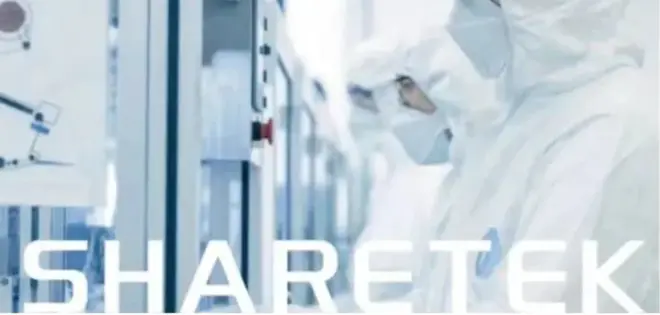
02 项目方案亮点
• 合理顶层规划布局 满足多模式生产
可实现多种类产品,单件流及批次流生产有效的融合在一起。
• 多系统集成 提升效率 支持年产能目标
可实现多系统集成(MES系统、WMS系统、EAP系统、ERP系统等),打破信息孤岛,提升生产及仓储物流等各环节的管理效率,有效支持客户年产能目标。
• 模块化/标准化产品 缩短项目周期
可提供众多自主研发可控的软件产品(Sharetek MES生产执行系统、Sharetek EAP设备自动化系统等)及硬件设备(自动插针机、自动模块贴片设备、HTRB测试系统等),通过不断进行升级迭代,可实现模块化、标准化、批量化产出,大幅缩短项目周期。
• 智能仓储转运 提升工厂效率及产出
通过信息化,可实现物料、产品可根据订单自动拣配出库入库,完成物料自动转运,减少重复、无价值的人工搬运成本,实现精准化配送和在制品流转。
• 数据采集、存储、追溯及数据价值挖掘
实现设备的生产工艺数据实时采集、存储、管理和下载;同时可实现最细化的追溯管理颗粒度,实现全流程正向或反向追溯。大数据平台可将产品、工艺、质量及供应链等数据进行建模分析,实现数据价值。
• 可视化看板与报表 透明化生产
通过看板、报表实时监控车间批次生产进度、关键质量问题、设备运行状态等;生产过程中,物料全流程标签化,可合理安排物料出入库,降低生产成本,实现灵活生产调度。
03 轩田科技智能工厂方案
轩田科技实施的智能工厂以工业 4.0 为导向,软硬结合CPS为特色,不仅提供了自动化解决方案,而且通过工业软件将IT、OT和DT(信息技术、运营技术和数据技术)相结合,实现真正的数字孪生落地,全面赋能客户的加速量产、稳质和降本。
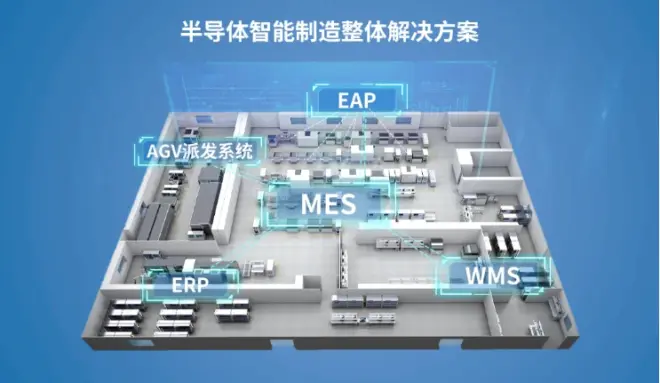
轩田科技积极推动智能工厂建设,推动工业软件、数字孪生等数字技术与制造业的深度融合,基于自主研发的完善的整体解决方案,产品被广泛应用于半导体、微组装/电装/总装等多个行业领域,服务的客户包括世界500强企业及其他众多头部企业。

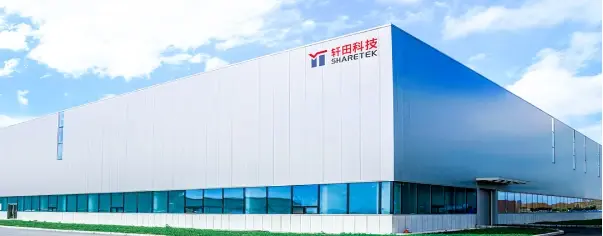
轩田科技成立于2007年,是一家致力“软硬结合 共创互联”的高新技术企业,总部位于上海,下属控股公司5家,参股公司3家,专注为客户提供软硬件结合的智能制造整体解决方案,包含数字化工厂顶层规划设计与实施。基于大量自主研发的国产替代智能装备、安全可控工业软件,轩田科技已为微组装/电装/总装、半导体晶圆与封测、汽车电子/3C电子等众多领域客户,提供了含智能生产制造及智能仓储物流等在内的完全自主可控的定制化解决方案。
轩田科技,智能制造领域相关标准制定者,具备“自动化 + 信息化宏观总体规划”、“硬件 + 软件一体化设计”、“多学科交叉 + 跨领域集成”的领先优势,曾为世界500强企业及其他众多头部企业打造了先进数字化智能工厂、标杆数字化车间,特别是在功率半导体、微系统微组装等智能制造领域拥有丰富的项目经验和优势。
轩田科技,致力于“硬核科技”发展,在核心工业软件、关键装备、精密运动控制、算法、复杂功能自动测试系统等领域重点技术攻关,拥有4大研发基地,3大生产基地(过渡厂房15000余平方米和在建厂房40余亩)。工程技术与研发人员占总人数的70%,专利、软件著作权等合计320余项(申报/授权)。同时公司在株洲、北京、马来西亚等地设有销售与技术支持团队,致力为客户提供高效的服务。
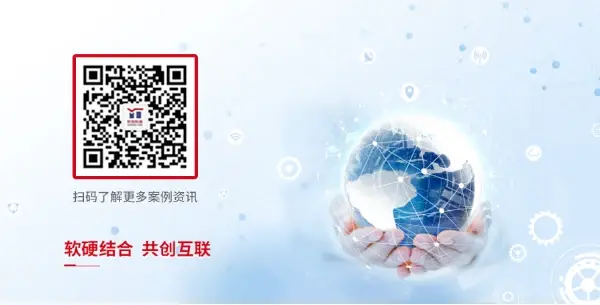