GH3536镍基高温合金轧管产生表面裂纹的原因分析
1引言
在批量生产的GH3536(规格为φ34mmx2.5mm)合金冷轧管外表面发现比较严重的网状裂纹,取样解剖后发现内表面也有纵向微裂纹;对外表面合格的部分成品冷轧管进行探伤检查,对探伤不合格的冷轧管解剖后发现内表面也有不同程度的纵向微裂纹。此项攻关研究拟在查找裂纹产生的原因,制订合理可行的GH3536合金轧管生产工艺。
2试验材料
试验用合金采用非真空感应+电渣重熔工艺冶炼,锻轧成φ95mm的棒材:(1)经过多道次轧制,最终冷轧成φ34rmmx2.5mm管,轧管经2号混底炉处理后取样;(2)经过多道次轧制,最终冷轧成φ18mmx1.5mm管,轧态取样。
3试验方案
试验方案为:(1)分析合金的化学成分、检测力学性能并与相应的技术条件做比较;(2)对经2号棍底炉处理后的φ34mm×2.5mm轧管解剖,观察裂纹的扩展方向和析出相的分布情况;(3)对φ18mmx1.5mm轧管试样进行1130℃、1150℃、1170℃、1190℃x30min的热处理,观察晶粒度的变化及碳化物的分布情况,并与经过2号辑底炉处理的轧管进行比较。
试验结果
4.1φ95mm轧棒的质量检查
合金的化学成分如表1所示,机械性能如表2所示。从表1可以看出,合金的化学成分和力学性能都满足技术标准要求。
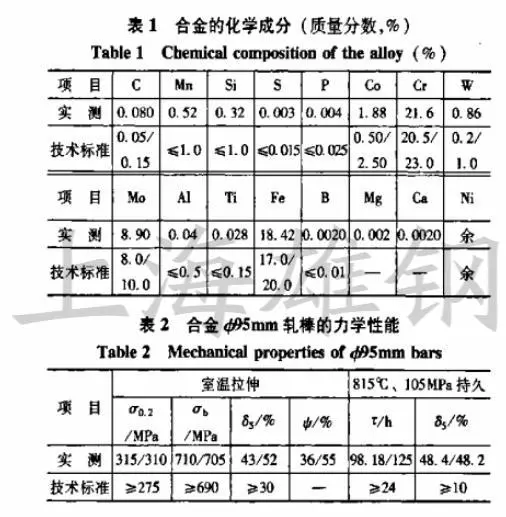
4.2φ34mmx2.5mm轧管质量检查
经过2号辐底炉处理的轧管晶粒度不均匀(图1a),且不同轧管的晶粒度差别较大。经测量裂纹深度为0.1mm(图1b),属表面裂纹。
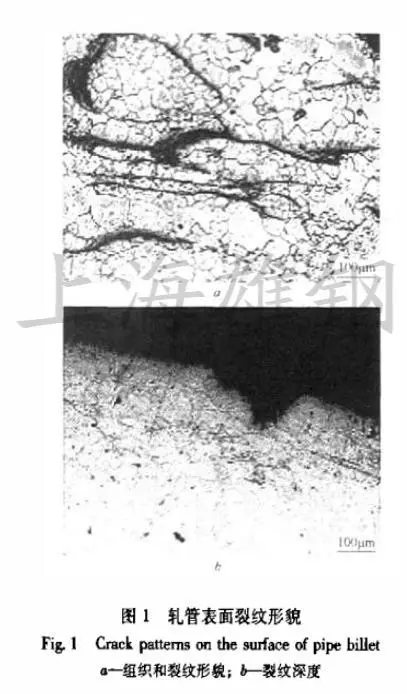
4.3φ18mm×1.5mm轧管经不同温度热处理后质量检查
在实验室经过1130、1150、1170、1190℃×30min热处理后的组织如图2所示。可见,合金在1130℃发生回复;1150℃开始再结晶;1170℃再结晶完成,晶粒度5.5级;1190℃再结晶完成,晶粒长大到3.5级。热处理温度与晶粒度的关系符合一般高温合金冷加工材的晶粒长大规律。
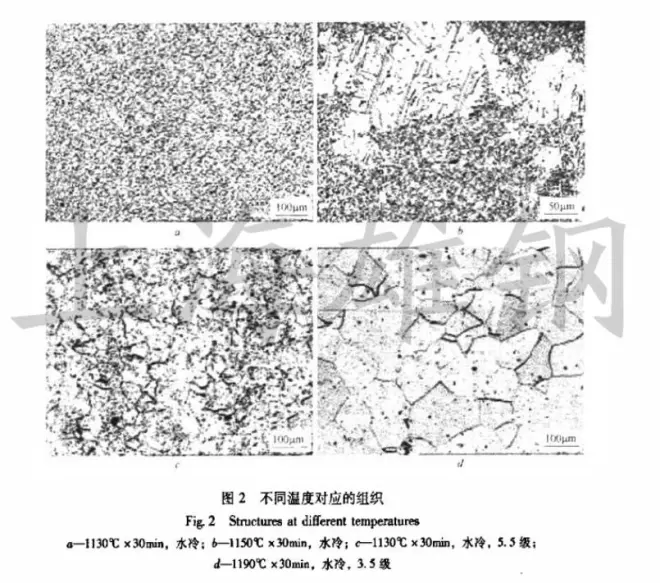
5分析和讨论
5.1φ95mm轧棒的质量评估
由表1可以看出,合金的主元索成分都符合相应技术标准要求。tw(Mg)的含量为0.002%,根据以往的研究资料,W(Mg)含量在0.0008%~0.007%之间不会对合金的冷加工塑性产生影响。由表2看出,φ95mm轧棒的机械性能都满足技术条件的要求且富余量较大。因此,φ95mm轧棒的质量稳定可靠。
5.2裂纹产生的原因分析
实验表明,经过2号辗底炉仪表温度为1150~1160℃处理的φ34mmx2.5mm的冷轧管的品粒度不均,有粗晶组织,且不同轧管的品粒度差别牧大。出其出见,炉膛实际温度控制不准确,仪表温度和实际温度相差较大,造成轧管的晶粒粗大,使合金的塑性下降。后经校正证实:2号棍底炉的实际温度比仪表温度高60~70℃,所以由于合金在热处理过程中温度偏高,造成晶粒粗大,这是导致出现表面裂纹的原因之一。
另外,在冷加工过程中的冷轧变形是一个减径、压下和定径过程,是一个不均匀的变形过程。管材在轧制时,其表层和心部的变形是不一致的,而表层的压下程度和变形速度均大于心部,导致表层的变形程度要大于心部,所以表面出现裂纹。另外,由于在整个冷加工过程中,每道次的平均变形量均不超过50%,因此并没有出现完全开裂或较深的裂纹。同时在实际生产中也发现一个现象:即表面产生裂纹后,对其进行整体磨抛处理干净,再次进行轧制时,会重新出现表面裂纹,此结果有待于进一步的试验,以改进轧制工艺。
6结论
(1)GH3536合金轧棒(管坯)的质量稳定可靠。
(2)裂纹是2号辑底炉的实际温度偏高,造成轧管的晶粒粗大,使合金的塑性下降。同时合金在轧制过程中表层变形过大,从而导致出现表面裂纹。
(3)GH3536合金的冷轧管的热处理温度应控制在1150~1170℃之间。
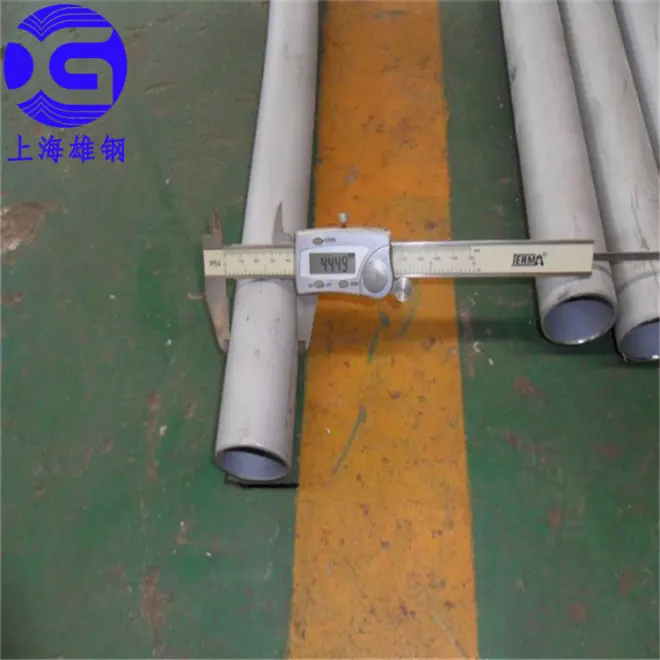