3D打印让装备修复更加便利
进入21世纪,一款新的生产模式——计算机增材制造成为了新的时尚,由于它使用计算机控制喷头(或激光烧结系统)在一个平面工作台上直接“喷”出目标产物,就像用打印机打印出物品,因此它也得到了一个非常形象的绰号,3d打印技术。由于3d打印机门槛有高有低,低端的3d打印机一般的家庭即可购置,所以就在哔哩哔哩上,就有很多的up主是使用3d打印机来工作的。
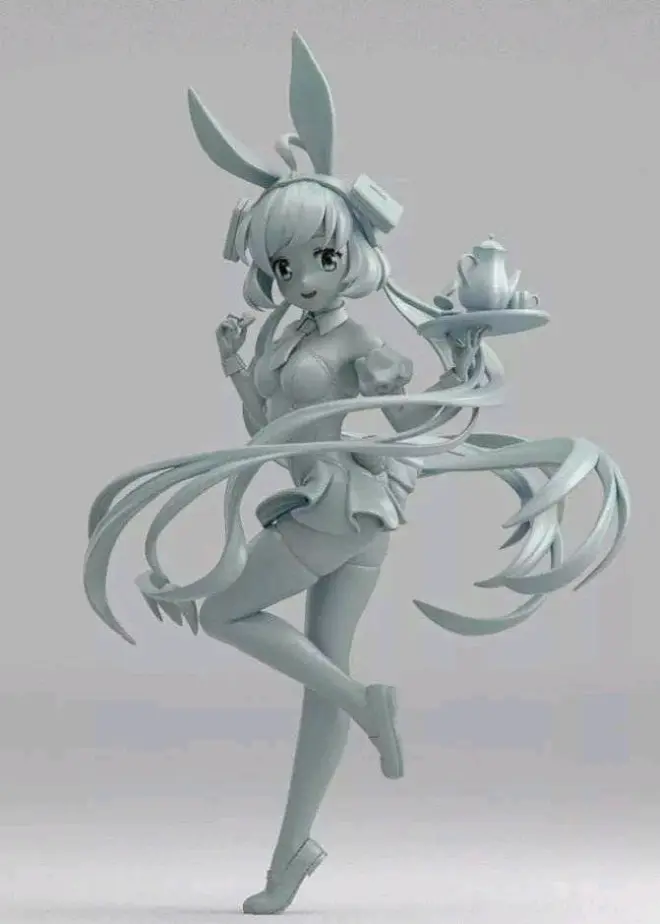
在军用领域使用3d打印技术也早已成为司空见惯的事情。在中国,歼11b战斗机的零件,从2016年起就有很多使用3d打印制作的零件,在歼20飞机,在歼20飞机,以及美国的f35飞机上,都或多或少使用了3d打印成型件。
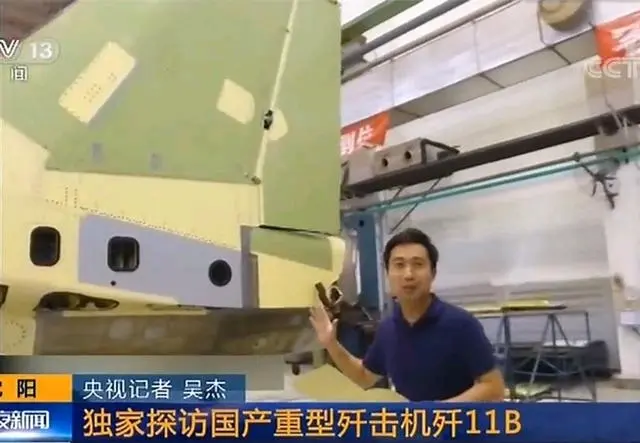
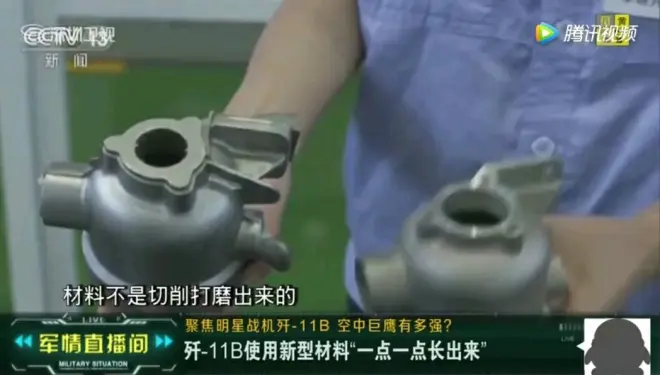
相比于传统机械制造技术,增材制造技术用于生产战斗机零部件的时候,可以将非常不容易采用传统机加工的零部件通过电脑控制的3D打印系统一次性加工完毕,这种增材制造能够一次性形成复杂的内表面和外表面结构,大幅降低了时间。同时,3d打印往往可以采用六角形填充方式将内部填充,以六角形的蜂窝结构替代固实填充,使得整体的重量比起整体结构更加轻便,同时强度又不至于降低,大量使用该类零部件,可以大幅度降低飞机的重量。
这些内容已经被我们广而所知。然而,3d打印技术虽然很好,但是也有一些缺点,在生产结构较为简单,并且模具相对容易制造的零件的时候,3d打印生产效率比起一般机械加工、铸造成型要低很多;同时由于3D打印技术在相当长一段时间里面,它只是将材料简单的堆积在一起,缺乏一个紧固和压缩的过程,所以它的强度比起传统锻造还要差一些,所以这导致3d打印技术,往往只是生产小部分特种部件,大量的零件生产仍然依托于传统的机加工技术。
所以,到底什么领域能够让3d打印小批量生产,单件生产,特种形状零件生产的优势发挥的淋漓尽致呢?这就该进入今天的主题3d打印技术是如何助力于产品修理领域。

2019年俄罗斯的航空部门颁发了一个特别的奖项,用来奖励俄罗斯航空专家在修复苏联时代生产的米格31战斗机时,所创新性使用的工艺工法。但当奖项公布的时候,所有人都大吃了一惊,原来修复如此一架昂贵的战斗机,所使用的设备居然是一台不到2000人民币的中国产3d打印机。这又是什么原理呢?请让我们看一看这篇报道的新闻原文。
俄罗斯联合航空制造发文《3D打印的米格战斗机》
海外网2019年12月21日电 最近一台来自中国的3D打印机在俄罗斯火了。原来,俄罗斯一位飞机工程师日前透露了快速修复米格-31战斗机的秘密——利用3D打印技术,且这台打印机是他花1800元从中国网购的。
俄罗斯联合航空制造集团20日发布了一则新闻稿《3D打印的米格战斗机》。文章称,集团日前举办了内部生产系统改进项目年度竞赛。经过激烈角逐,米格公司下属的下诺夫哥罗德“雄鹰”飞机制造厂首席设计工程师阿列克谢,凭借3D打印技术快速修复米格-31战斗机,一人揽得两项年度大奖。
俄媒称,这引发了现场巨大轰动,以往很少有人能独揽两项大奖。于是在场同行纷纷向阿列克谢及其团队请教,使用的3D打印机是从哪里弄来的。
“阿列克谢,你使用的打印机是买零件自己组装的,还是购买的成品?”被台下同行提问后,阿列克谢答道:“我们买零件,自己组装的。”同行继续追问:“零件从哪里买的?”阿列克谢笑着回答:“中国,我们在阿里巴巴(AliExpress)网购的。”
据悉,阿列克谢及其团队从中国海淘来这台3D打印机,在短时间内解决了困扰下诺夫哥罗德“雄鹰”飞机制造厂的米格-31零部件生产难题,让一批积压在“雄鹰”厂待修的米格-31战斗机重新服役。
据阿列克谢介绍,今年他和他的团队在进行米格-31战斗机的维修和现代化过程中遭遇了巨大难题——原厂零件装不上。由于俄罗斯后勤管理系统落后,每次修理都未被精准记录在案,部分修理厂在修理过程中使用了加强垫片,还有一些修理厂擅自改变了固定孔的位置。这就导致米格-31战斗机在返厂大修时,原装零件反而装不上去。
阿列克谢在了解到外国同行已经利用3D打印技术,进行战斗机零件的快速制作后,他就通过阿里巴巴全球购从中国购得一台3D打印机零件及耗材,一共花了1.6万卢布,约合1800元人民币。
据悉,在第一次试用之后,阿列克谢及其团队就发现,原先传统工艺制作一个试模件需要11道工序,而3D打印只需要4道;原先一个零件从设计到制造需要340小时,3D打印只需要29个小时,效率比原先提高了11倍;原先一批样件制作需要耗资100万卢布,而3D打印只需要1.2万卢布,平均成本降低98.7%。
“这个项目的成功告诉我们,每个人都有机会证明,一个战士在战场上为解决特定问题而表现出来的巨大智慧。”阿列克谢说,虽然3D打印的解决方案不能用于大规模生产,但它却可以解决类似小的难题。
俄工程师这个大胆创意赢得了俄罗斯网友的点赞:真的非常方便,还物美价廉,可以想什么时候制造,就什么时候制造。中国网友也感叹,这也太厉害了吧,还喊话俄罗斯:中国海淘,值得拥有。(海外网 张琪)
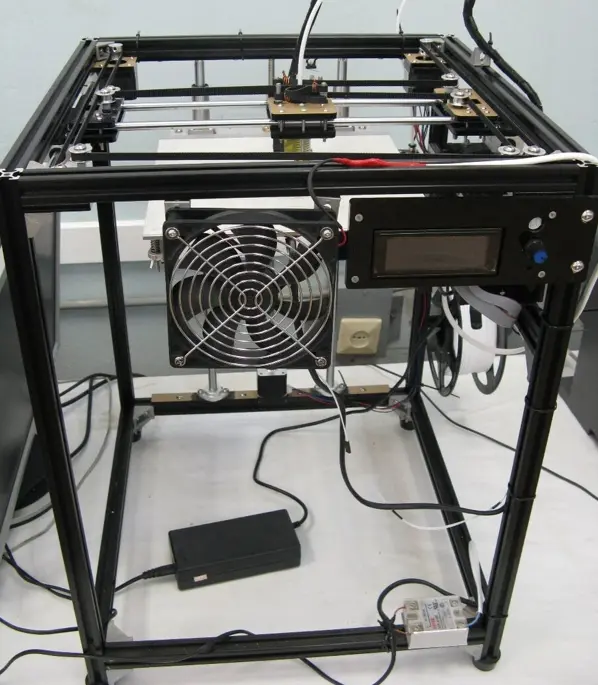
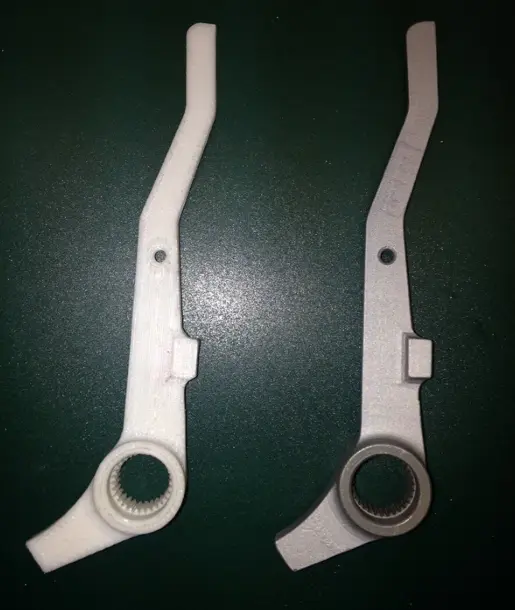
这篇生动详实的新闻报道,非常清晰阐述3d打印的诸多优势。
首先3d打印特别适合于复杂零件的生产,这种零件往往不太容易使用机械加工技术,这种零件在上文中已经提及,不再赘述。
第二就是3d打印特别适合于生产,单件不重复的零件。我们很清楚,在生产结构尺寸相同,规模大量的零件时候特别适合于使用铸造或者是模压的手段,只要制造出一个模具,就可以使用压铸机、注塑机或者模压机大量生产相同型号相同尺寸,相同规格的零件由于模具可以重复利用,所以只要制造出一个模具,有了材料和机械,就等于可以在任何时候生产出任何数量的物品,成本就非常的非常的低。但是在生产仅仅一件产品的时候,这种生产模式所浪费的资源和花费的成本就非常高了。比如要生产出一个扳手型的物体,对于传统的加工方式来讲,首先需要制造一个高强度的合金模,然后再使用压铸技术或者使用模锻技术将一块型钢按照模具做成相关的形状,这样一来,生产这一个扳手就要单独生产出这一个模具,为他单独开一次耗电量极高的水压机或者开一锅熔炉。而生产完毕之后,这套模具也随之报废,不能再为以后的生产所用,所以生产这种产品是非常不划算的。而在这个时候无需提前制模,只要打开电脑即可使用的3d打印技术,自然是不二之选。
第三就是3d打印机它的部署更加容易便利,一般的3d打印机往往由几个零部件组成,比如控制喷头,激光头移动的芯片和电路板,喷头(或者激光烧结头),供料机构,托盘,冷却系统,以及最后的控制计算机。小型的3d打印机甚至可以分解成几个零件,一辆小汽车即可携带,非常便利。但一个相同加工精度的五轴小型加工中心,它的成本和它的尺寸都是远远超越小型3d打印机的,而且部署条件更加苛刻,需要非常专业人才才能操纵,成本也非常高昂。
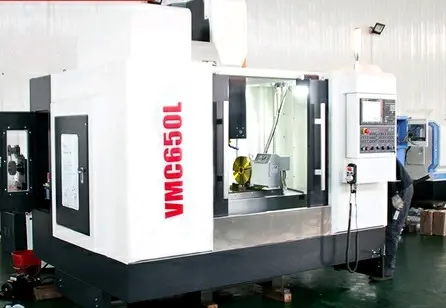
因此大家就能看出来3d打印技术,对于特别需要生产形状不统一,单位批次有限,结构复杂,用时限制比较短的零件非常具有竞争力。这对于野战环境下修理因战斗造成的设备损伤,有着非常重要的实践意义。
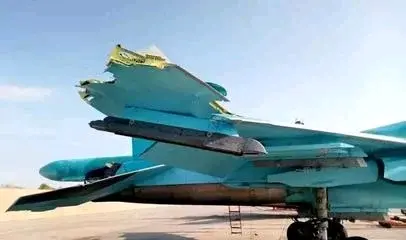
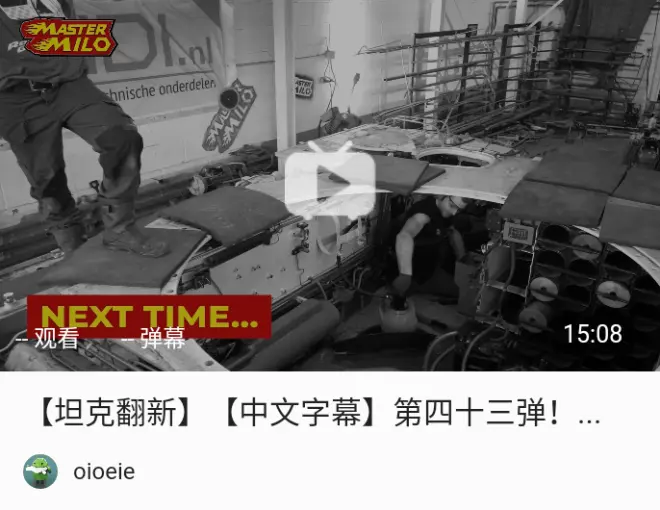
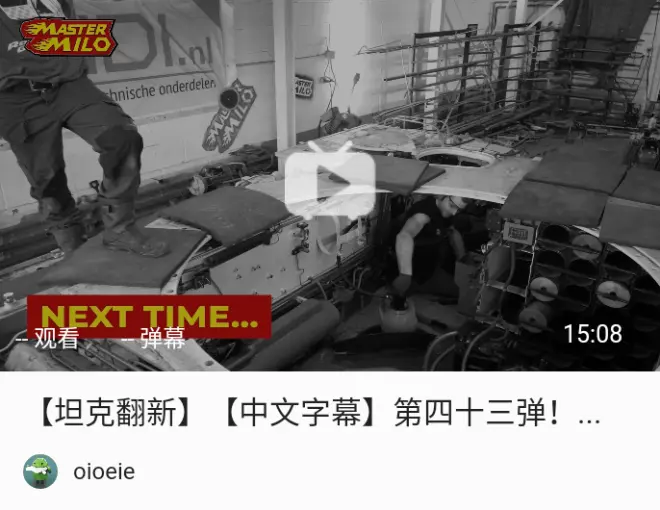
这个由荷兰军迷进行的69式坦克修理的视频已经连载超过几年。他们面对的一个很大的问题,就是因为这辆坦克是在伊拉克战场被摧毁的,因此它的零部件大多因战火和岁月的侵蚀,已经损坏严重,而且它的原厂已经不再生产同类尺寸的零件,所以他们的很多零件都是通过咨询改装车同行们,以各种能够找到的市场上的零件,或者以机床生产尺寸接近的零件进行替代的。而这样一来,为每一个系统寻找相同的零件所消耗的时间,就是非常长的时间了。从他们开始修复到今日已经过去两三年,这辆坦克底盘上的相关零件还没有完全找齐。而这一点在战场上是绝对不能接受的。虽然战场上为了应付这种情况,往往会预留很多的零件,比如整体的汽车,发动机,坦克发动机,甚至还有整个的坦克炮塔作为预备。但是如同这里的军迷遇到的问题一样,对于有些遭受损坏,无法进行整体拆卸更换的设备,就必须使用大小规格相同的东西来修复。这导致有很多坦克无法就地维修,只能送回原厂,全面拆解之后才能进行大修。而如果有了便携式的3d打印机,在战场上面对一些小的,结构比较复杂的零件,修理工程师就会通过3d打印技术,生产出结构相同,尺寸相同的替代零部件给坦克换上。这样无疑能够大幅降低装备修复的时间。
好钢要用在刀刃上,对于特别需要考虑单件生产,特异零部件生产的野战修理环境来讲,3d打印无疑是一个非常好的发展方向。在3d打印技术非常成熟的我国,早在几年前就已经成功开始了此类实践工作。
本报(解放军报)成都2015年8月10日电 欧阳治民、记者张放报道:武器装备部件也能打印?8月9日,记者在“补给行动-2015”军需物资油料保障演练现场,见证了这神奇一幕。
当天10时30分许,由成都军区抽组的应急兵站油料保障分队一辆6管加油车被炮火“毁伤”。经检测,系加油车联轴器损坏。因联轴器为非易损部件,应急兵站无库存,油料保障分队立即启用油料装备修理工程车,利用3D打印机现场打印制作联轴器。
记者在工程车内看到,油料装备维修队士官董凯毅打开软件,调出联轴器三维模型。同时,另一名操作员刘得俊根据联轴器构成,在打印机内装入高分子材料。董凯毅一按鼠标,打印机喷头便喷出粉末状材料,逐层打印和粘合。不久,联轴器底端便初显雏形。
军区联勤部领导告诉记者,在高原高寒山地作战,携运行的装备零部件有限,装备受损需换件时,常面临“带来的用不上,用得上的没带,后方筹措又太慢”等窘况。他们经论证试验,在油料装备修理工程车上加装3D打印机,并建立齿轮、棘轮、卷盘、轴等各类零配件的三维模型。此次演练,他们首次将这一成果运用于保障实践,在高原演兵场建起“配件制造车间”,创造了首次运用3D打印技术维修后勤装备的先例。
联轴器打印完毕,修理工立即对受损加油车换件维修。经技术测试,加油车性能恢复正常,重新投入加油作业。“小小1台打印机,能抵5个修理工!”董凯毅感慨地说,用传统方式自制零配件需要各类机床,并经过“车、钳、洗、刨、磨”等复杂工序。现在3D打印机的投入使用,使维修告别了许多笨重的“坛坛罐罐”,野战抢修效率大大提高。
本人相信,随着更多的高新技术的广泛使用,我国的装备保障技术将会得到更进一步的飞跃!
20200626增补:针对部分小伙伴有关于3D打印零部件的疑虑,本人现将一篇新闻报道摘抄如下:
由华中科技大学机械学院张海鸥教授主导研发的一项金属3D打印技术“智能微铸锻”,在3D打印技术中加入锻打技术,能生产结实、耐磨的金属产品,打破了3D打印行业存在的最大障碍,有望开启人类实验室制造大型机械的新篇章。
传统机械制造中,浇铸后的金属材料不能直接加工成高性能零部件,必须通过锻造改造其内部结构,解决成型问题。但是对超大锻机的过度依赖,导致机械制作投资大、成本高且制作流程长、能耗巨大、污染严重、浪费严重并难以制作梯度功能材料零件。
作为后起之秀的常规金属3D打印技术因能够解决传统制造业的以上弊病而受到青睐。然而,常规3D打印同样存在致命缺陷:一是没有经过锻造,金属抗疲劳性严重不足;二是制件性能不高;三是存在气孔和未融合部分;四是大都采用激光、电子束为热源,成本高昂。因而形成了“中看不中用”无法高端应用的局面。
为解决这一世界性难题,张海鸥团队经过十多年潜心攻关,研制出微铸锻同步复合设备创造性地将金属铸造、锻压技术合二为一,实现了首超西方的微型边铸边锻的颠覆性原始创新,从而大幅提高了制件强度和韧性,提高了构件的疲劳寿命和可靠性。不仅能打印薄壁金属零件,而且能打印出大壁厚差的金属零件,省去了传统巨型锻压机的成本。
“常规3D打印金属零件的过程是打印算一层,铸造算一层,锻压又一层,三者要分开依次进行,即前一个步骤完了,后一个步骤方可进行,中间还要腾出金属冷却的时间”。张海鸥介绍,智能微铸锻技术可以同时进行上述步骤,打印完成了,铸锻也就同时完成了。
“我们将原先需要8万吨力才能完成的动作,降低到八万分之一,也就是不到1吨的力即可完成,同时一台设备完成了过去诸多大型设备才能完成的工作,绿色又高效。”他说。
该技术以金属丝材为原料,材料利用率达到80%以上,丝材料价格成本为目前普遍使用的激光扑粉粉材的1/10左右。在热源方面,使用高效廉价的电弧为热源,成本为目前普遍使用的大多需要进口的激光器的1/10。

泵喷推进器主要应用于船舶重工等领域,是船舶航行的重要动力装置。此次通过金属3D打印“微铸锻”技术制造成功的大型泵喷推进器桨叶,选用不锈钢316L原材料,成型尺寸达到直径0.6米、高度1米,总重量160千克。通过验收与测试,制造周期相比传统方式缩短了2/3,构件的力学性能得到了大幅度提升,制造精度差由以前的0.5mm提高到0.1mm,没有检测到铸造缺陷如气孔、裂纹等。
在我国研制的新型战斗机上,一种新型复杂钛合金接头的制造也已经开始和张海鸥团队合作,用该技术打印出来的钛合金抗拉强度、屈服强度、塑性、冲击韧性均超过传统锻件。
目前,该技术正在西航动力公司、西安飞机制造公司等新产品开发中应用,已经试制了高温合金双扭叶轮、铝硅合金热压泵体、发动机过渡段等零件,以及大型飞机蒙皮热压成形双曲面模具、轿车翼子板冲压成形FGM模具等,应用前景广阔。
目前,根据空客公司对飞机零部件的需求,张海鸥团队正在进行研发,“一旦继续获得认可,我们将赢得空客的零部件生产的订单,同时还可能获得更多国际民用航空巨头的青睐。”张海鸥说。
此前跟据报道,张海鸥教授团队的“智能微铸锻增材制造”发明专利技术,在金属微熔铸的同时同一工位复合锻造工艺,“铸锻复合,边铸边锻”可以获得增材制造锻态无织构12级超细等轴晶、高强韧、高可靠性能的复杂形状金属锻件,突破性地解决了传统制造流程长、污染重、能耗高、材料利用率低、需要超大型锻机的世界性难题,同时克服了常规金属增材制造没有经过锻造,容易出现气孔、裂纹等缺陷,产生高致密性、各向同性、等轴细晶,强度、韧性较传统制造更高,可以增强关键重要零部件的性能,改变了“铸锻分离”的传统制造模式,较传统制造方法可缩短制造流程60%以上,节能90%以上,成本降低60%以上,有望开启绿色短流程制造金属锻件的新模式,为高端制造业颠覆性创新技术。该发明专利技术已经试点应用于航空、航天、海洋工程、核能、高端装备等高性能核心复杂零部件制造。
最近,国家科学技术奖励工作办公室日前公示了2020年度国家科学技术奖受理项目名单。其中,“大型复杂高端零件微铸锻同步超短流程制造技术与装备”,即“金属3D打印‘微铸锻’”技术提名2020年度国家技术发明奖一等奖。提名意见认为:“该重大原创性成果能够有力支撑我国高端装备自主创新,引领短流程制造技术革命和传统工业绿色转型升级。”