工业研磨自动化需要多维合作才能在市场共赢
吴佩知 博士,广东英达实业有限公司
广东江门鹤山市建设东路35号,lwu2020@icloud.com
摘要:对于工业研磨自动化,用户真正需求是效果+成本,所以只靠设备或者只靠磨具的单维度作战很难满足客户需求。市场需要设备,磨具,工艺等多维度合作创新才能实现真正有竞争力的方案,最终实现共赢。
关键词:工业研磨,自动化,合作共赢
1 前言
日趋上升的研磨人工成本,产业结构的优化升级,国家政策的大力扶持,这三大因素正在催生工业研磨自动化领域的春天。国家十四五规划明确表示,制造业高质量发展是当前重要任务,实现由主要依靠传统工业化道路向靠技术进步和可持续发展的新型工业化道路转型。在制造业转型升级的过程中,高质量企业将获得更多的市场机会,与之相反的,低质量(高能耗,高污染,低效率)的企业将面临淘汰,激烈的市场竞争将倒逼企业加速提升生产效率。
工业研磨作为制造业的一个环节这几年发展迅猛。尤其是工业机器人的快速发展加上用户对于品质稳定性的要求逐年上升。很多机器人集成商,磨料磨具供应商也为客户提供一体式的打磨方案。但是在实际操作的过程在,遇到很多问题:最终用户希望少投资多办事。作为设备集成商要想实现研磨工艺的各种指标,各种模块必须配备到位。但是设备模块到位了,成本也就上去了。对于磨料磨具供应商,生产磨具是强项,但是对于开发研磨工艺,解决千变万化的研磨技术要求,能力还有待提升。如何实现多维度合作,最终实现自动化设备效果+成本的更优(与人工打磨方案相对比)是当下最需要解决的问题。
1.目前工业研磨自动化的市场需求
人工成本
根据国家统计局公布数据,我国制造业人员年平均工资从 2000年 8750 元增长至 2020 年 74761元。另外随着我国老龄化人口结构占比不断升高,我国 2002 年以来 15-64 岁劳动人口比例从 2010 年最高的的 74.5%降至2020 年的 70.1%,人口红利正在消失。特别是研磨行业,根据我们走访的企业很多打磨工人的平均年龄都在45-55岁,没有年轻人愿意加入这个辛苦,污染大的行业。在广东地区,研磨工人的月工资普遍在10000元以上,且不愿意加班。作为制造大国,工业研磨领域的自动化替代人工的经济性愈加凸显。
对磨料磨具的新要求
除了人工的因素之外,这几年更多的新型材料逐步产业化,对研磨效果,效率提出了更高要求,例如,轻量化大量使用铝合金,碳纤维材料,超硬镀层等新型材料表面都需要新的研磨方案。这对于磨具行业就提出新的挑战:需要磨具更能适应于高速强压下的研磨,更少灰尘更环保,更加稳定的研磨效果,更长的使用寿命(图1-1)。
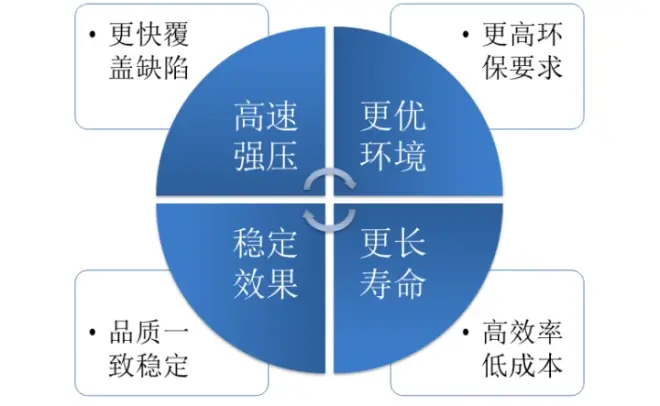
图1-1
效果+成本才是用户的最终需求
对于最终用户来说,研磨属于工件加工的一部分环节,其最重要的是保证研磨效果一致性。人工研磨由于加入了人的因素,需要工人具有一定的技术经验。机器相对于人效果更稳定,但是也缺乏灵活性。在传统的研磨方案中自动化研磨有需求并不意味着自动化研磨是唯一的选项。传统的人工+简易工具/设备仍然具有很大的灵活性对于小批量,多品种有着天然的加工优势。
对于研磨用户来说除了效果,成本是必须考虑的因素。 产品的最终用户也不会因为采用机器人加工而为此多付一分钱。
综上所述,机器替代人在工业研磨行业是大势所趋,核心是“如何”替代。
2. 目前存在的问题
由于目前工业研磨自动化的需求多数发生在行业龙头客户的典型应用。所以,当我们接到案子之后多数都会参考现有人工打磨工艺,磨料磨具,并在这个基础上设计设备,来实现对人工打磨的替代(图2-1)。
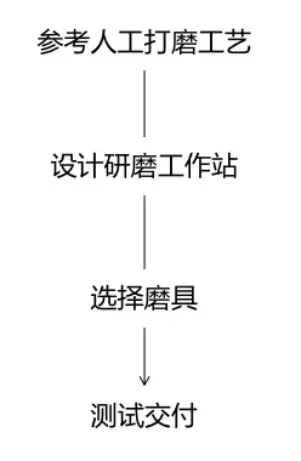
(图2-1)
但是由于现有的研磨工艺受制于之前磨料磨具或者设备参数的限制只是在人工打磨下系统相对最优,但并不意味着在设备打磨下系统效率也一定最优。例如在人工打磨时很容易对研磨压力,研磨位置做灵活调整,但是轮到设备打磨,首先要求来料的一致性,同时设备也无法像人眼或者人手那样灵活,随时根据现实的情况做快速调整。 如果要实现这些快速调整的功能,就需要上视觉,力控等模块。这些模块的增加反过来会增加机器研磨的投入成本和维护调整费用。这样算下来,设备打磨与人工打磨方案相比就未必占优了。
深究下去,实际上这是由于设备,磨具,加工工艺各行业之间不能做到融会贯通所导致的,换句话说只在一个地方发力。做设备的未必了解磨料磨具,做磨具的未必了解加工工艺的特点,做工艺的也不能完全了解磨具/设备。也正是因为这样,每个环节单独面对客户要求的时候,只考虑本专业的方法来解决问题。这种“深井”思路限制了行业的发展。
3. 解决思路
3.1 用系统思维寻找最优解
客户真正需要的是解决研磨问题,是为了研磨后的产品在市场上有竞争力,加工成本还不能高。所以我们提出要用系统的思路来解决这个问题。
系统思维是指:为了解决研磨问题,综合各方的优势来解决研磨问题。具体来说,做工艺的要懂设备/磨具,做磨具的要懂设备/工艺,做设备的要懂磨具与工艺。真正站到客户的角度去优化解决问题。
3.2 有效的协调机制
为了更好更早的找到工业研磨自动化系统最优解,就需要研磨参与的各方能够通力合作,而不是单打独斗。这就需要认同这种价值观的人能够走到一起。
首先是有能力快速开发新工艺,在接到案子之后能够快速测试各种研磨方案的效果。研磨行业都需要拿样品说话,快速研磨工艺实践是最重要的一环,这就需要磨具供应商和设备商的配合,能够用最小成本,最快速找到合适的解决方案。
在确定新工艺的基础上,再选用最优化的机器来实现:更多采用标准化的结构和产品快速实现设备的调整。不一定是最大的能力最强的设备,而是要选择合适的设备来工艺工艺上的问题。
在磨具方面,更是要发挥每一种研磨工具的特点,涂覆类产品就是用于磨削,尼龙类产品就用于表面处理。发挥每一种磨具的特点,来实现最优解。
整个整个过程并不是串联的,而是螺旋向上的一个过程,设备推动磨具,磨具推动工艺,工艺又反过来推动设备。不断循环,不断迭代的过程。最终找到更优解(图3-1)。
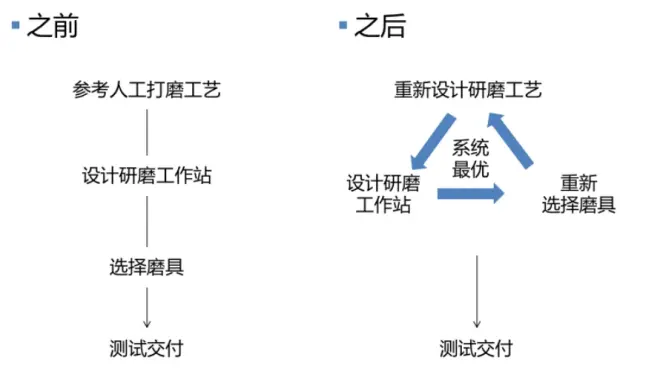
图3-1
3.3 实践案例
例如,我们最近接到一个碳纤维脱模剂去除的案子。通常人工打磨都会采用水砂纸,原因是因为碳纤维非常耐冲击,但是不耐磨。但是人工打磨存在工作环境差,品质不稳定,效率低等特点,所以客户希望进行自动化改造。
当我们接到案子以后,与设备商进行深入探讨:如果还是照抄现有的研磨工艺,只是把人换成机器人,成本一定无法接受。 原因是人手可以根据工件的形状进行调整,而机器要做到这点就需要力控,视觉才能解决。在经过快速尝试各种方案之后,最终我们选择一种新的研磨工艺。就不再需要力控,力量大一点小一点,进给多一点少一点,由具有弹性的磨具进行自动调整,即不会过磨又能达到去除脱模剂的效果(图3-2)。
核心上,我们要改变过去只从单维度优化的思路,要结合设备,工艺,磨具各方不同的优势,最终寻求系统最优(即:效果+成本综合最优)
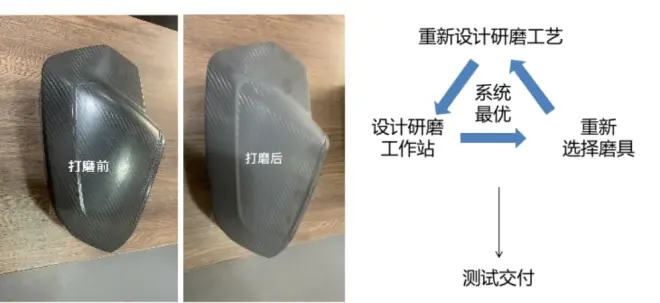
图3-2
4 结束语
送别2022,迎来2023。新的一年,研磨行业我们将迎来新的挑战和机遇。实现高质量发展是我们行业当前首要发展任务。回到工业研磨自动化的根本:为客户创造价值!我们会继续坚持跨行业多维合作,积极为客户提供更优的研磨技术方案。期待我们的中国制造2025!