拧紧螺栓背后的知识,你真的都了解么?
以下内容已制作视频发布:
【[催眠警告] 拧紧螺栓背后的知识,你真的都了解么?】 https://www.bilibili.com/video/BV1oe4y1k7gx?share_source=copy_web&vd_source=78d3bab1595a9ec7b3a4c2d798397327
应部分网友要求,释放文案。
在B站看各种汽车类和机械类的视频时,我经常能发现一些对螺栓的错误认知或者操作。比方说最经典的,1.用气动冲击扳手,也就是风炮来拧紧螺栓。除此之外还有:2.对所有的螺栓追求使用扭矩扳手。3.将某些部位的铝合金螺栓的应用,视作厂商对成本的考虑。4.对一次性螺栓的使用,归咎于厂商处于赚钱的目的。5.盲目追求强度区分大的螺栓。而所有错误里错得最厉害最根本的其实是这句话:6.只有用扭矩扳手上到指定的扭矩,才能把螺栓上到合适的紧固程度。
是不是很意外,但这是事实,这个理解是错误的。因为评价螺栓缔结程度的量根本就不是紧固力矩,而是预紧力。这三个字会在这个视频里反复出现,我就是要用这个视频,像洗脑一样,把这三个字刻在你脑子里。
预紧力英文是“Pre-tension Force”,日语里叫“締結力”(ていけつりょく/Teiketsuryoku),但一般我们称之为“軸力”(じくりょく/Jikuryoku),他是螺栓的螺纹部位在旋入对手件的内螺纹后,弹性拉伸螺栓杆部所产生的反力。本着万物皆可弹簧的原则,我们其实可以用这样一个模型来看待预紧力的产生。预紧力是评价螺栓是否紧固到位,是否发生松动的指标。我们可以用“预紧力发生下降”来定义描述螺栓发生松动。
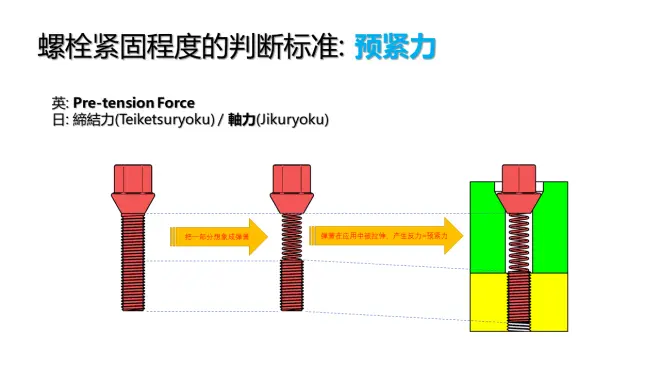
但是,如此重要的一个指标,在实际的生产活动中,却很难直接进行调查和管控。因为大部分时候螺栓埋在对手件里,它的弹性变形看不见也摸不着。如果我们一定要直接测量预紧力,不是对螺栓结构产生破坏,就是这种测量后的状态不能当作商品去出售。因此,包括汽车工业在内,大部分实际应用中,我们用管控紧固力矩的方式来间接地管控预紧力。那有网友要说了,废话了那么半天,那最后不还是用扭矩扳手管控紧固力矩么?手段是这个没错,问题出在,紧固力矩不是唯一影响预紧力的变量,还有另一个非常非常重要的变量,那就是螺纹对之间,以及螺栓头部承载面之间的摩擦系数。
这里我想问各位网友一个问题,你们觉得这个摩擦系数是越大,螺栓不容易松动,还是越小,不容易松动?我相信你们的直觉肯定是,那当然是摩擦系数越大,这些面上的摩擦力就越大,螺栓更容易自锁,不容易松动,对不对?但你们肯定也会觉得,如果这个问题要是那么简单,我肯定没有必要单独拎出来问你们。没错,如果紧固前后的摩擦系数不会变化,那么实际上摩擦系数越小,螺栓更不容易松动。
为什么呢?因为,虽然螺栓发生松动的原因及方式可以分为很多种,但是大部分时候,我们可以简单粗暴地认为,在参与缔结的所有零件都不发生失效(崩塌,断裂)的情况下,预紧力越大,这个缔结就越不容易松动,越可靠。而从预紧力的计算公式中可以看出,上述摩擦系数都在分式的下方作分母。那显然摩擦系数越大,预紧力就会越小。
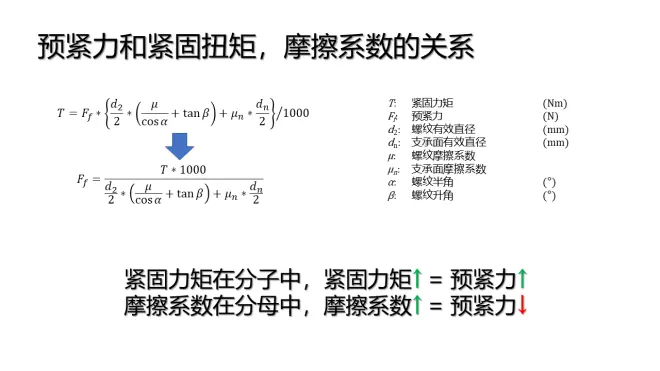
如果你依旧觉得这个说法很违反你的直觉,那我打个不恰当的比方,你可能就会懂了。某年某月某日,科学家发现富士山要发生万年一遇的大喷发,届时喷涌出的岩浆可能会毁灭大半个本州岛,导致日本这个国家消失。于是小日子过得不错的人们想出了一个办法,就是造一个巨型机甲,把一个大圆石块推到富士山顶,堵住喷口。显然,在机甲可以做的功有限的情况下,滚动石头上山时遇到的摩擦阻力越小,那能推到山顶的石块就越大,抵挡喷发的能力就越强。说白了就是在有限的能量下,在摩擦力上损失的功越少,就可以转化更多的能量到石块的重力势能。如果我们把紧固螺栓看作是通过转动扳手做功,把能量转化成螺栓的张力势能,那么浪费在摩擦力上的功越少,获得的张力势能就越大,因此抵御外力松动螺栓的能力就越强。讲人话,摩擦阻力抵消了一部分你对扳手的作用力,导致有效输出降低了。
在我的实际工作经验中,当我们供应商向主机厂提供的产品中,参与缔结的部件(螺栓或者对手件的缔结面)发生制程变化时,我们的客户都会关注摩擦系数的变化,要求我们通过试验证明,变化前后的预紧力是否发生下降,导致松动风险的提高。本田如此,马自达如此,尼桑亦如此。这说明,预紧力的重要性至少在日本的车企里,那是一个基础认知中的基础。
不过这种重视态度也不是来的无缘无故的。2002年1月10日,在神奈川県横浜市瀬谷区发生了一起,大型卡车左前轮脱落,飞奔50米的轮胎砸中外出步行的母子三人,造成29岁的母亲当场死亡的事故。这期事故牵扯到了对三菱扶桑卡客车的第二次召回隐瞒调查。一系列的召回隐瞒事件对三菱自动车的品牌形象产生及其负面的影响。在我和日本同事(老板)的交谈中得知,日本人眼里,三菱自动车这个品牌的衰败就是源于这一系列的召回隐瞒事件。而回到事故的原因,根本原因是卡车轴头(HUB)厚度不足的设计缺陷。而对轮毂螺栓的预紧力管理的懈怠,使得过高的预紧力加剧了轴头的金属疲劳,从而导致轴头断裂,轮胎脱落,是次要原因。这期事故在日本的影响巨大,以至于出现了一部以其为背景的电影[空飛ぶタイヤ(飞空的轮胎)]。你能想到,螺栓的预紧力问题,居然也是压垮了很多人喜欢的,创造了Lan EVO系列,4G63辉煌的三菱自动车的其中一根稻草。
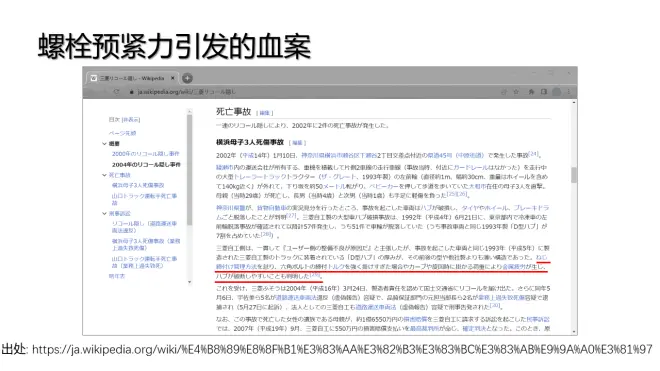
从上面这个事故中我们也可以看出,虽然预紧力高意味着不容易松动,但并不意味着因此我们就可以无限地追求预紧力。因为螺栓本身的强度关系和被缔结零件的强度关系,过高的预紧力会对螺栓自身或者被缔结件造成破坏。我在著名的扭矩管理工具制造商的东日(TOHNICHI)的技术资料里找到这样一张图,可以很好的说明,预紧力为什么要做到合适,而不是越大越好。FU和FL分别代表在实际应用中,预紧力的上下极限。当超过上限时,会依次发生,(螺栓的)外螺纹损坏,被缔结零件的损坏,(对手件的)内螺纹损坏,螺栓的支承面损坏。
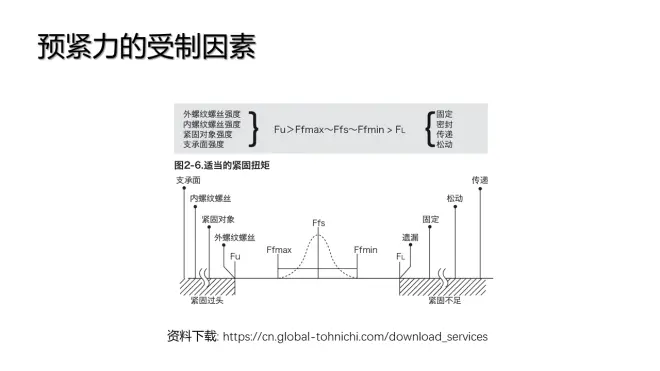
值得注意的是,这里的顺序是有意义的。很多时候我们在设计螺纹缔结时,会有意识地控制螺栓的强度区分,把螺栓外螺纹的强度,做的比对手件的内螺纹强度低。这样一来,如果发生没有管控预紧力,比方说使用气动冲击扳手来紧螺栓,导致预紧力超标了。那我们肯定是希望破坏发生在螺栓这侧,这样我们还可以用断丝取出器把断在里面的那截取出来。而如果是对手件的内螺纹坏了,那意味着对手件的报废。那可能是一个刹车卡钳,也可能是个发动机中缸。你们觉得哪一种损失更大?所以开头提到的错误5,盲目使用强度区分大的螺栓,不妥的地方就是把本来维修成本更低的外螺纹损坏风险,放到了维修成本更高的对手件内螺纹损坏风险之后了。
在这里做一下扩展,就是刚才提到的中缸。我们经常会看到一些改造发动机的视频里,改造者会更换更强的螺栓来承受大幅提升的缸压。但是实际上无论你的螺栓有多强,如果改造后的缸压分摊到每个螺栓上的负载,流到内螺纹上,超过了内螺纹的(疲劳)强度,那么你还是会有爆缸的危险。内螺纹的强度取决于材料强度和有效螺纹长度。这么一想,内螺纹部位的设计也是限制一台发动机改造潜力的因素之一。
其实还有第二个扩展点,就是风炮的使用问题。这个我在讲了预紧力管理后再说。回到这张图。我们再看预紧力不足时的四个问题。这里日东的中文版资料有翻译错误,日语原文的“もれ(漏れ)”这里不应该翻译成遗漏,而是泄露。我在之前做油底壳的视频就提到过,密封需要两个条件,一个是完整闭合的接触线,另一个就是接触线上抵抗流体外泄的接触压力。而很多密封应用中的压力来源,就是预紧力。比方说我们的油底壳放油螺栓(Bleed Screw),还有我们刹车卡钳和软管的这个连接点(Banjo Connector),还有发动机上各种堵头(Screw plug),都是这种情况。因此,如果此时的预紧力不足以产生抵抗流体外泄的接触压强,那么就会发生流体外泄。
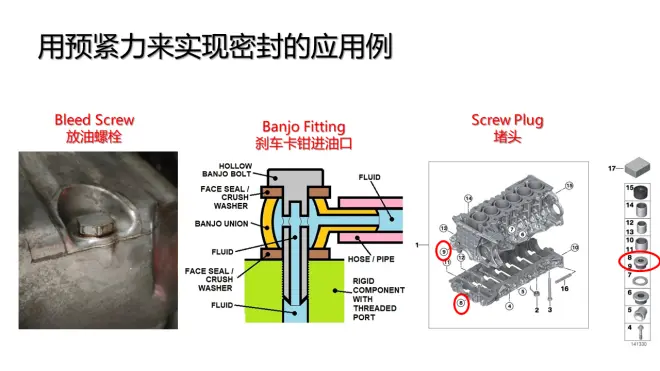
诶,说到卡钳和堵头,你们是不是想到某个品牌的卡钳在赛道上发生漏油的事情?没错,我看到那两个视频时的第一反应就是,大概率卡钳上那个堵头的预紧力不够!或者因为堵头螺栓的热膨胀系数和卡钳材料的膨胀系数不同,高温下内螺纹的膨胀量比外螺纹大,导致预紧力逐渐下降,螺栓逐渐松开,向入口处移动,最后直接连同封胶一起,被液压挤飞出去。当然了,以上只是我的推测,我无法对这个结论负责。但是借这个假设,我想说开头的错误3,就是有高温工况时,缔结件之间热膨胀系数不同,会产生松动的风险。不仅如此,螺栓材料和被缔结零件的材料的不同,还会导致异电位腐蚀。所以铝合金中缸上用铝合金螺栓,完全是技术导向的结果,根本不是成本出发的考量。
如果预紧力进一步下降,那么接下去被缔结部件就不能很牢固地被压在一起。再往下走,螺栓直接就松了。然后螺栓本身就成了负载传递的途径。这里我要解释一下最后这个传递问题。我的理解是,他和前面的固定是有关联的。当我们用螺栓紧紧地把两个零部件贴合在一起,对这两个部件施加两个方向相反的力时,实际上这个力并不是直接由螺栓来承受的。而是先用两个面之间的摩擦力来抵消。像我曾经参与过的轮毂轴承,它的设计理念就是如此。
还是拿我自己的宝马E90 335i举例。N55发动机的最大输出扭矩是400Nm,变速箱一档齿比4.17,差速器终齿比3.46,不考虑各种损耗,此时的两个轮子总计最大轮上力矩的账面数值是接近5800Nm,也就是单个轮上有2900Nm的输出力矩。再让我们来算算轮毂螺栓能够产生多大的摩擦力。考虑到摩擦系数难以精确获得,我在这里编排了几种不同的摩擦系数组合,分别代表各种有利和不利情况。这么一对比会发现,诶,除了最后一种特别有利的情况,其他都不够呀!
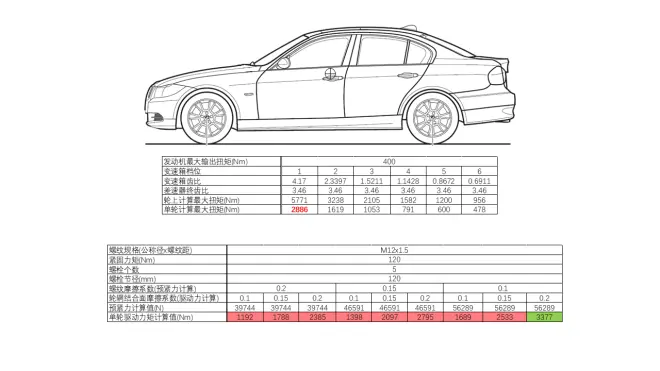
先别急。实际上1档时的最大的扭矩并不能完全用来加速,因为输出驱动力超过轮胎抓地力时,轮胎就打滑了。考虑到轮胎的路面附着系数的限制,我们要换个角度,从加速性能来考虑。对于一个1.8吨,轮胎直径635mm的车子,我大致计算了轮胎附着系数从0.1到1.2,轮胎能产生的最大驱动力矩。在轮胎附着系数为1的理想条件下,四驱后轮的结果最大,单个轮胎上的驱动力矩是2348Nm,即两个加起来大概4800Nm。这就比刚才的5800Nm要下降不少。这个时候,满足要求的螺纹工况就多了三个。再考虑到我这车的百公里加速基本上进不了5秒,这也符合实际道路工况中,轮胎地面附着系数在0.7到0.8左右的一般水平。这时候,有效的驱动力矩只有1600Nm左右。也就是说,只要轮辋结合面的摩擦系数不是最坏情况,那摩擦力就能满足驱动力的要求。
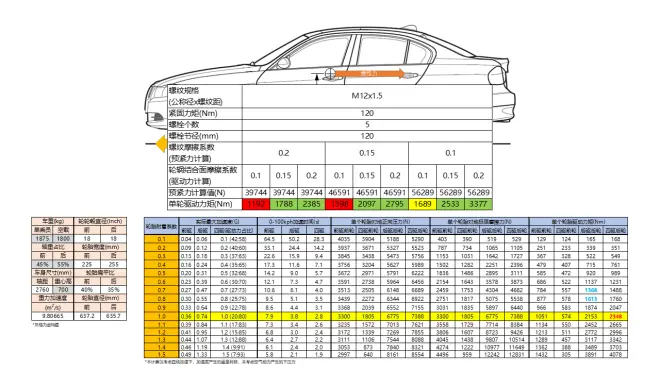
如果我们的轮辋以不利的条件安装在轴头上,那么轮毂螺栓将承担一部分驱动力,使螺栓产生弯曲乃至剪切负载。倒不是说螺栓完全不能承受这种负载,但是从我的工作经验来看,这不是一种合适的工况。当螺栓发送松动后,轮辋安装面丧失正向压力,也就没有办法产生摩擦力。这时候驱动力将完全由螺栓来承担,也就是上面所说的传递。
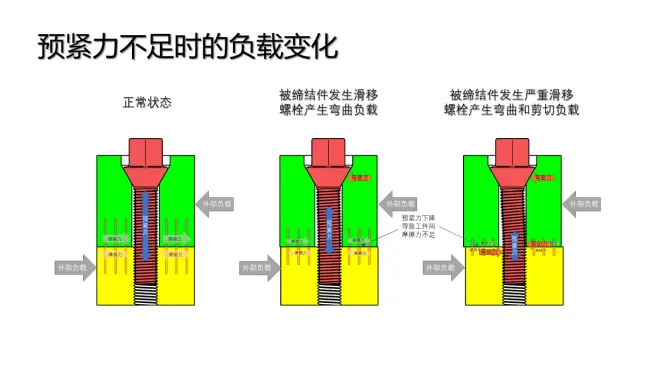
当然,我这种思维模式不一定是百分百正确的。这个计算非常的粗糙,没有考虑到车身自重,还有路面平整度带来的额外负载。而且335i也并非这个平台上驱动力最大的车型,它上面还有个M3,有着更大的输出,却使用着同样的轮毂螺栓设计。更甚至与,在最近和一些群友聊天时,我才明白,在赛车领域,这个部位的设计思维和我的设计经验也相去甚远。所以上面的内容,请大家选择性吸收。不过我想借这个计算引出这个视频的核心内容,就是预紧力管理。
前面这么长的铺垫就是想让各位理解,螺栓的预紧力应当被控制在一个合适的范围。下限防松,上限防崩。然而预紧力的管控手段非常有限,名义上,以东日列举的方法为例,有扭矩控制法,旋转角度法,扭矩斜率法,伸长率测量法,加力法,加热法这几种。然而实际生产活动中,基本上只用到了前两种,也就是扭矩控制法和旋转角度法。像表里提到的超声波测量伸长率这种方法,基本只在科研活动或者产品研发中才会用到。我在四年前解决本田的一个项目问题时,就请我们德国总部的同事用这个方法帮我们测了几个刹车卡钳进油口螺栓(Banjo Bolt)的预紧力,结果事后被那个部门Charge了1万欧元,直接把我整懵了。
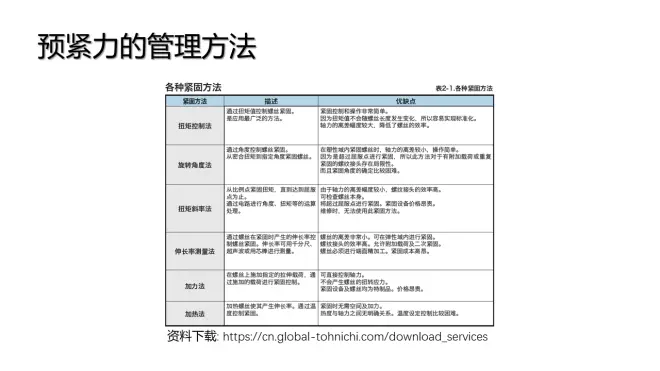
资料下载: https://cn.global-tohnichi.com/download_services
预紧力管控最常用的手段,就是用扭矩控制法。就是用扭矩扳手将螺栓紧到目标扭矩。使用的扭矩扳手可以是这种预置式的,也可以是这种指针式的,或者这种数显测量式的。但是无论你用哪一种扳手,说到底,你也只是控制了扭矩,而没有控制摩擦系数。而现实中摩擦系数的偏差反而是更大的那个。还是以东日给出的数据为例。在使用机械油的情况下,摩擦系数的范围在0.1到0.2之间,以平均值0.15为基准,偏差为±33%。即使使用预紧力稳定剂,偏差范围也有±10%。而你一把预置式扭力扳手,天天用,不校准,用上10年,偏差也不见的能大到30%。这就是为什么开头我说,第六个观念是错误的。如果你的缔结件因为什么原因,已经螺纹变形或者表面性状发生改变,导致摩擦系数超过了正常范围,那你就算用了扭矩扳手也不见得能获得合适的预紧力。
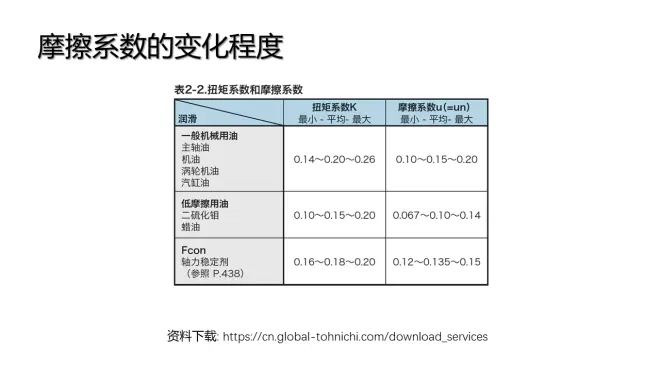
说到这里我不禁想起了若干年前,我看到溜溜哥去Endless的工厂参观的视频,在组装工位那里他指着工作台上一瓶小东西问是什么。Endless方的员工回答了一句“润滑用的”,然后飘过的弹幕都是,“那是防松胶”。没错,那确实是防松胶,日语叫做ゆるみ止め剤(ゆるみどめざい/yurumidomezai)。但是你们觉得,他们工人能不知道那是防松胶么?实际上防松胶不仅仅只有胶合的作用。在固化前,它确实具有一定的润滑性。这一点可以从Loctite的官方网站上找到证据。就我这些年和日本工程师打交道的经验来看,他们对化学粘连的作用确实还是抱持着一种保守的态度。他们更愿意用预紧力,摩擦系数这些量去评价螺纹的缔结程度。所以那位员工把本该是打辅助的润滑作用放到胶合作用之上,就我个人而言,是一个情理之中的回答。
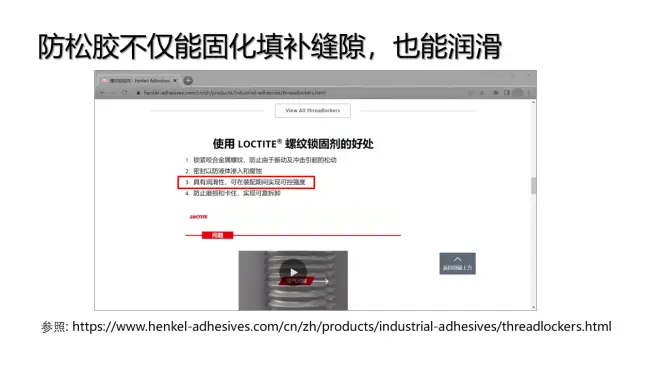
再说回扭矩控制法,还有一个不得不提的问题,就是风炮上螺栓。这是个老生常谈的问题了。普通修理厂用的风炮并不是一种精确的可调可控的工具,跟F1上用的Wheel Gun根本不能相提并论。虽然很多风炮都有几个级别可调,且需要多次敲击才可能达到设定级别里的极限扭矩,但是你无法准确的知道你敲出来的那几次最终给你上到多大的扭矩。以我手上的这把风炮为例。你别看他那么小,它最小的一档,在0.62MPa的供气压力下,持续敲击5秒,正转时能获得330Nm的紧固力矩。反转时的最大档能达到700Nm。那么我该怎么调整供气压力,敲几下,才能让我的螺栓不超过120Nm呢?我无从得知。
那有些网友要说了,这不是用了风炮以后还会再用扭矩扳手上一次么。这里就需要大家明白,一般修理厂里最常出现的,就是这种预置式的扭力扳手。这种扳手其实只能管理扭矩的下限。当你用这种扳手把螺栓上到预置的扭矩值,比方说90Nm,发生咔哒一声的时候,你仍然可以继续紧下去,比方说一直干到120,130。当你松开扳手,然后再一次去紧固螺栓时,扳手还是会在90Nm的时候发出咔哒一声,但实际上你的螺栓早已承受了120以上的扭矩。所以,它只能告诉你有没有高于某个值,但它没办法同时限制不要超过另一个值。在实际应用中,我们是在紧到一定程度后慢慢加力,到咔哒一声后立刻停止,使扭矩超越设定值(下限),但又不至于超过太多。先风炮后扭矩扳手的做法,如同我拿把扭矩扳手,直接用我最大的力气把螺栓干到底。这个过程中,咔哒是咔哒了,但是它没有起到管控的作用。所以哪怕你用的不是预置式的,而是用指针式,或者电子测量式的扳手,归根结底,在你进行管控前,扭矩就已经超过管控范围的话,你的管控不具有任何意义。这就是开头错误1背后的逻辑。如果你确实需要气动工具或者电动工具来提高效率,那你可以使用非常确定输出力矩低于目标值的工具,比方说我手上这个,这只是一把气动棘轮扳手(air ratchet wrench),而不是气动冲击扳手(air impact wrench)。他的最大输出扭矩只有34Nm,用在100Nm附近的轮毂螺栓上非常安全。
再说回预紧力管控方法。扭矩控制法因为摩擦系数偏差的限制,其管控精度是有限的。如果在只有一个螺栓固定的应用上,那在设计阶段,通过计算,确保在摩擦系数偏向最大,扭矩偏向最小时,依旧能满足最低的预紧力需求,那倒也没什么问题。但是对于多螺栓固定的应用,比方说发动机气门室和中缸的缔结,预紧力是否合适的定义不再局限于个体螺栓的预紧力结果,多个螺栓预紧力的一致性也成为一个非常重要的特性。
我曾经听过一个段子,就是AE86上那个4A-GE,有在雅马哈发动机组装的和在丰田工厂组装的两个版本(前期/中期以后)。但是雅马哈发动机的版本就是比丰田的版本,马力高上那么几匹。而其原因,就是雅马哈发动机在生产时,气门室螺栓的紧固管理做得比丰田更加严格。这个段子是真是假已经不可考。如果要我给出我的看法,我觉得合理。因为如果缸盖螺栓的预紧力有高有低,那么中缸内螺纹附近的材料应变也会有所不同,导致燃烧室缸壁圆度/圆筒度变差,损耗掉燃烧能量。
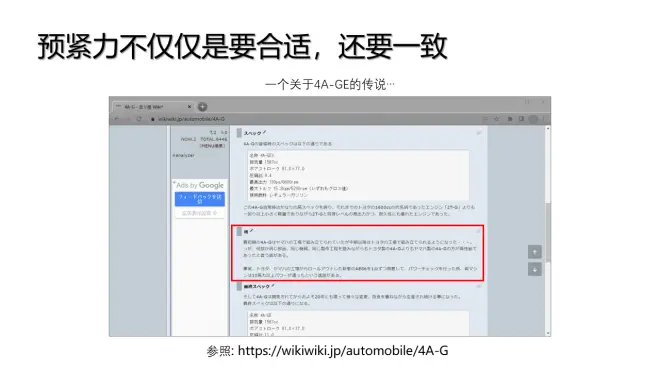
我的一个朋友曾经给我看过一个资料,里面引用了一个,轮毂螺栓预紧力不一致导致刹车盘Run-out达到80多个微米的调查结果。虽然这两个案例我都没法给出非常确凿的证据,但是我仍旧希望各位理解,多螺栓缔结应用中,螺栓预紧力一致性的重要性。
由此引出第二种预紧力管理法: 旋转角度法。B站上有很多修车师傅的视频都会告诉你,用这样的方法能实现螺栓的稳定紧固,但是我没见过有谁能把这个原理讲清楚的,毕竟他们中的大多数都只是照着维修指导书来操作的。而这种指导书都是设计工程师编写的。那工程师为什么要这么设计,这么指示呢?因为这种用法的核心思想是,通过强制拉伸螺栓到一定程度,使其进入屈服,利用屈服平台下应力变化较小的特性来保证预紧力的一致性。先理解强制拉伸。当一个螺纹规格确定下来时,它的螺纹距就把螺栓的旋转角度和螺纹前端的前进距离绑定了。比方说一个M12x1.5的螺栓,每旋转360度,和内螺纹嵌合的部分就向前推进1.5毫米。那么转180度,前进0.75毫米,转90度前进0.375毫米,以此类推。
接下来,我们需要引入螺栓材料的应力应变曲线来理解屈服。金属材料在受力拉伸时,会先表现出弹性特征,即应力和应变呈现线性关系。当把材料拉升到某个程度后,应力不再成比例增长,而是缓慢增长后反而下降。直观感受就是,你会发现,即使你继续拉伸这个零件,你需要提供的拉力,或者说你感受到的反力,也没有明显增加,甚至约拉约轻松。这就是所谓的屈服。再进一步拉伸到一个极限后,材料就会断裂。从屈服到断裂这段就是塑性变形,或者说永久变形的区域。
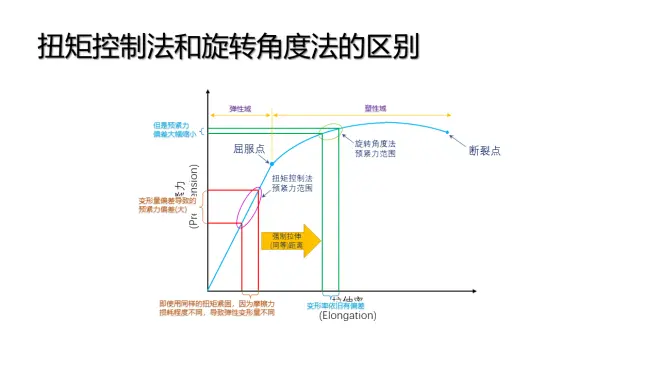
因为应变本身就是变形量,在拉伸过程中就是伸长率,而应力乘以零件受力部位横截面积等于所受拉伸负载,所以在坐标轴上没有数值的时候,我们可以直接把横纵坐标名称改为伸长率和预紧力(拉伸负载)。如此一来,我们就可以用这个图来描述扭矩控制法和旋转角度法各自用在哪个区域。
扭矩控制法利用的是螺栓的弹性变形区。因为摩擦力不同导致能量损耗不同,就算用扭矩扳手将不同的螺栓上到同等扭矩,最终的弹性伸长率仍然是有大有小,得到预紧力就有较大偏差。但是接下去如果我们使他们强制拉伸同样的量,超过屈服点后,因为屈服平台里应力变化较小的关系,他们的预紧力差异就变小了。而且,这样一来,还可以使预紧力基本和摩擦系数说拜拜了。摩擦系数取决于两个接触面的性状。而现实车辆设计生产中,螺栓和对手件往往是来自不同的供应商。如果摩擦系数超过正常范围,那么螺栓供应商,对手件供应商和主机厂三者之间免不了要掰扯一阵子。而用了这种屈服模式的管理方法,本质上,预紧力只和螺栓的屈服应力挂钩。只要保证螺栓材质和尺寸精度,就能获得很好的预紧力一致性。这大大降低了品质管控的门槛。而唯一牺牲的,就是螺栓的再利用性。过了屈服点后的变形是塑性变形,即使释放负载,螺栓也回不到原来的长度。工程师能在设计螺栓时,保证一次这样的操作,变形量不会超过断裂点。但是第二次,第三次以后,拉伸量会不会超过断裂点,这就不好说了。所以,所有使用旋转角度法(屈服模式法)的螺栓,都是一次性的。这就是对开头错误4的解释。这依旧是一个技术导向的结果。
顺带一提的是,虽然主机厂们大多使用了屈服模式来一致化缸头螺栓的预紧力,但是有些改装件厂商并没有这么做。一个网友曾告诉我,ARP出的高强度缸头螺栓,不使用旋转角度法。我大胆猜测,这是因为螺栓强度上去的同时,韧性下降了,即断裂伸长率下降了。以前面显示的应力应变曲线(S-S图)来说,大概率断裂点向前推进了很多,导致很难找到一个合适的范围,既能确定进入屈服模式,又能保证不会超越断裂点。于是只好退而求其次,使用传统的扭矩控制法。为此,不得不使用摩擦系数稳定剂,也就是所谓的专用润滑油。
既然提到了螺栓的一次性使用,就多说一句。汽车行业里,用到的一次性螺栓,其实有两种情况,一种是刚才提到的屈服模式应用。而另一种,其实我也已经提到了,就是预涂防松胶的螺栓。因为防松胶里的厌氧胶其实是被封在微胶囊里的。当拧紧螺栓时,微胶囊被挤破,其中的厌氧胶被释放固化,达到胶合和填充空隙的目的。所以这种涂了防松胶的螺栓也经常被称为微胶囊化螺栓(Microencapsulated screws)。而正是厌氧胶的非再用性造成了预涂螺栓的非再用性。换句话说,如果你能找到的同等性能的防松胶涂到螺栓表面,其实这种螺栓可以再利用。
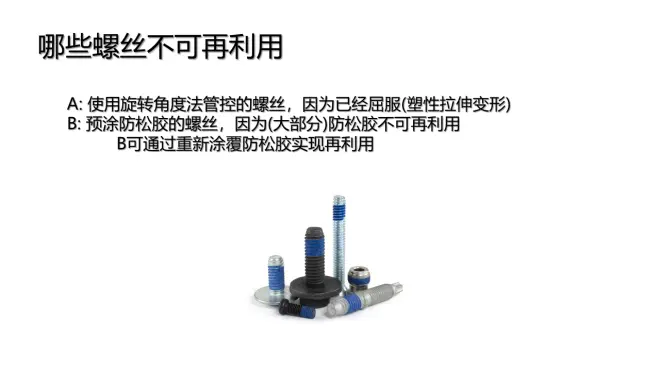
到这里,该解决的问题都解决得差不多了。最后聊一下。虽然上面讲了那么多预紧力重要性的内容,但是实际上并非所有螺栓缔结都需要管理预紧力,比方说被缔结部件之间没什么载荷,只做装饰固定。这其中还有一种客观无法进行预紧力管理的情况,就是用塑料做的被缔结件。因为要使螺栓产生预紧力,首先得有足够强度撑住螺栓使其弹性变形。然而包括工程塑料在内,绝大部分塑料都是所谓的非线性材料。他们没有金属材料那样有一段明显的直线弹性区域。在压缩塑料时,会很快进入一种,即使你再怎么压,它也不会给你很大的反作用力的状态。在实际应用中的直观表现就是,你总能觉得你还能再把螺栓上紧一点点。但往往,在你还没觉得你已经拧不动的时候,塑料件已经被螺栓压裂或者压塌了。因此,如果要在塑料零件上进行预紧力管理,比方说我手上这个装在电子手刹卡钳(EPB)上的马达驱动器单元,那么一定会像这样在塑料件里预埋一个金属环。用它来提供,或者说承受预紧力。反过来说,如果塑料件的螺栓通孔处没有这样的金属环,那就不需要预紧力管理,也就不需要扭矩扳手,用螺栓刀上到适可而止的程度就行了。
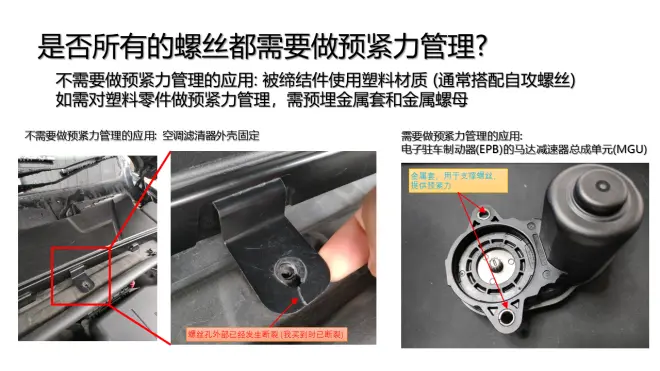
至此,把螺栓的预紧力管理也解释得差不多了,开头的错误理解也都给出了理由。基本的逻辑算是建立起来了吧。如果你听懂了,觉得有所收获,记得把它分享出去。让更多人明白其中的道理。那么,我们下次再会。