GH4049镍基合金钨夹杂射线检测工艺研究
在目视检验某机低压涡轮叶片时,发现在叶盆面与榫头转接R处存在一直径约1mm的缺陷,缺陷位置及形貌见图1和2。将缺陷处用砂纸打磨并腐蚀后观察,发现缺陷处较基体不易腐蚀,呈白亮色。将叶片放入扫描电镜进行能谱分析,发现缺陷部位主要成分为W80.7%,Ni7.8%,Co2.3%,Si3.7%和Cr2.1%等,可初步判断缺陷性质为钨夹杂。
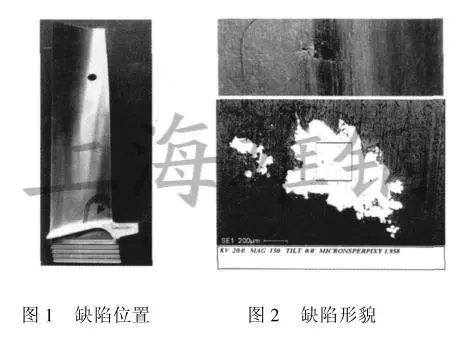
一般来说,钨夹杂多是在采用钨极氩弧焊打底+手工电弧焊或者钨极氩弧焊时,钨极崩落的碎屑留在焊缝内形成的高密度夹杂物(俗称夹钨)。虽然钨的熔点很高,但在GH4049电渣锭开坯及轧制温度下仍有一定的塑性,会随变形方向分布(包括点状、条状及连续点状等)。作为一种体积型缺陷,由于夹杂的存在,将导致合金屈服强度与抗拉强度差距明显缩小。当GH4049合金叶片等零件内部存在钨夹杂时,夹杂将引起应力集中,并成为交变载荷下的疲劳源,严重影响航空发动机涡轮叶片、箍段和箍套等零件的使用可靠性。经查,钢厂提供用于制造某发动机零件的GH4049合金棒材(φ32mm,φ28mm和φ8mm三种规格)已全部投产加工。为保证零件质量和使用的可靠性,研究并确定有效的射线检测工艺迫在眉睫。
1GH4049合金材料的特点
GH4049合金是复杂合金化的镍基高温合金,950℃以下有较高的高温强度,适宜制造900℃以下长期工作的航空发动机涡轮叶片或其它高温部件。GH4049合金经标准热处理后,组织是在γ固溶体的基体上分布有呈方形及球形的γ/[Ni3Al或Ni3(Al,Ti)],沿晶界呈细小链状分布的M6C,MC以及少量的M23C6(均为碳化物)和M3B2(硼化物),MC和M3B2是初生相沿变形方向分布。长期使用(时效)后没有新相析出,只有γ/[Ni3Al或Ni3(Al,Ti)]的集聚长大,以及M6C和M23C6碳化物的增多和形状的改变。
2射线检测工艺
2.1设备与器材的选择
透照采用XYD-3010固定式X射线机,所用辅助器材主要有铅箔增感屏、GYL-Ⅲ型胶片、GB5617-1985丝型像质计及暗袋和铅字等。
2.2曝光参数的确定
2.2.1焦距
焦距直接影响射线照相的几何不清晰度值,进而影响总的不清晰度值和小细节的射线照相对比度。因此选取焦距时应考虑:必须满足射线照相对几何不清晰度的规定,必须给出一定大小的均匀透照区。前者限定了可采用的焦距最小值,后者是有效透照区所要求的焦距。目前对钢铁等重金属材料常采用的规定方式如下:
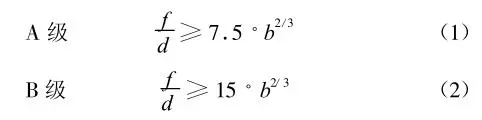
式中 f—射线源至物体源侧表面的距离,mm;
d—射线源尺寸,mm;
b—物体源侧表面至胶片的距离,mm。
当物体源侧表面与胶片间的距离较小时(如小于零件厚度的20%),b常指零件本身的厚度T。由于涡轮叶片、箍段和箍套等均属于航空零部件关键件,所以必须采用B级射线检测技术。将源尺寸d=3.0mm,被检测厚度Tmin=2mm和Tmax=21mm分别代入式(2),求得f分别为71.4和342.5mm。实际透照时,依据涡轮叶片、箍段和箍套等零件的不同结构特点和批次数量,采用的焦距为1200~2000mm,完全满足最小焦距要求。
2.2.2透照参数
按照射线检测的基本原理,当采用一定焦距透照同一材质、不同厚度的零件时,需考虑厚度宽容度,即在这个厚度差内射线照相灵敏度和射线照片黑度都应符合规定的要求。射线照相厚度宽容度决定于透照时所选用的射线能量和射线胶片。因此,在透照某发动机涡轮叶片、箍段和箍套等零件时,根据所用X射线机曝光曲线,通过试验确定了透照参数,具体数值及获得的底片影像质量见表1。
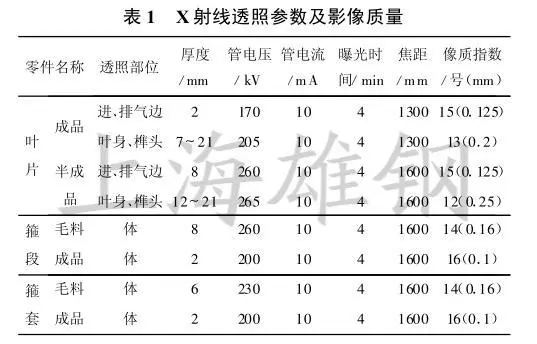
2.2.3X射线检查结果
对故障叶片(编号18A01807)缺陷处进行X光检查,发现在叶盆面与榫头转接R处存在的缺陷,在底片上反映出其内部实际上长度近6mm;对钢厂同期生产的GH4049棒材加工制造的所有叶片、箍段和箍套等零件(合计10855件)的成品和半成品进行X射线检查,发现另有5件叶片、4件箍段的半成品存在夹杂(图3)。
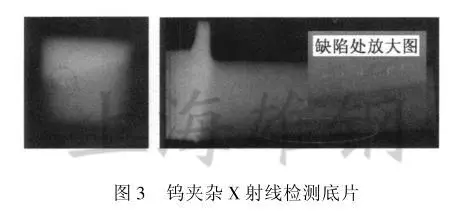
3夹杂性质及成因分析
3.1金相分析
(1)将X光底片上有夹杂显示的、编号为18A01035的叶片横截面磨制成金相试样进行组织观察和成分分析。缺陷在叶片中所处的位置见图4所示,缺陷位于叶身中部近叶背位置,其横截面大小约为0.4mm×0.18mm。经显微镜和扫描电镜观察为缺陷横截面呈“海绵”状,缺陷和基体相互包容,交界处未见分离现象(图5)。在叶片近叶盆部位发现有另一处长约0.4mm的缺陷,缺陷的组织形态与叶背处缺陷相同(图6)。能谱分析为:由于缺陷呈“海绵”状,在含钨量较高的白亮区中间掺杂着黑色的基体成分,所以用能谱进行不同区域的成分分析时不具有规律性,钨含量在55%~60%之间,两个位置缺陷的分析结果相同。
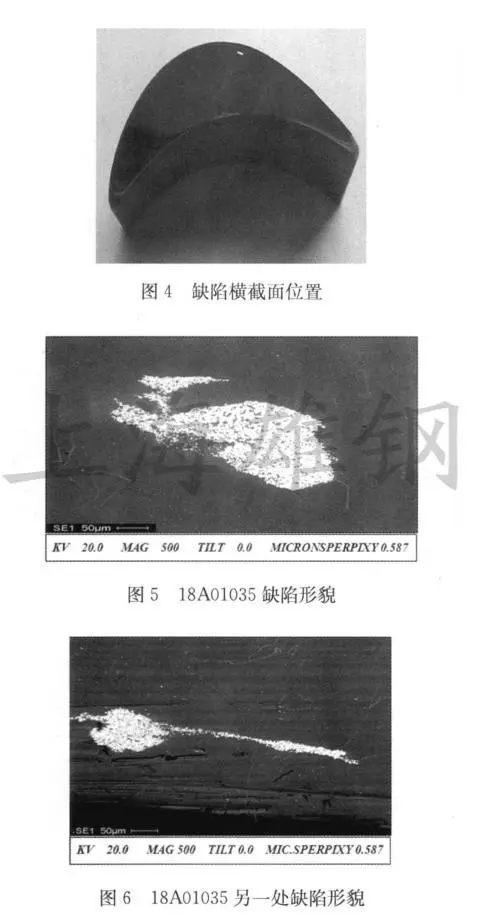
(2)将X光底片上有夹杂显示的、编号为18A03033的叶片横截面磨制成金相试样进行组织观察和成分分析。缺陷位于叶身中部近叶背位置(图7)。经显微镜和扫描电镜观察得:缺陷横截面有两块,大小约为0.22mm×0.08mm和0.3mm×0.18mm,均呈不规则固体形态,大块中间有破碎现象,缺陷与基体界限分明,但未见分离现象(图8)。能谱分析为:块状缺陷从中心部位到与基体交界处钨含量略有下降趋势(90%~82%),中间破碎的黑色区为基体成分,但钨含量较正常值偏高(约为16%,正常值为5%~6%)。
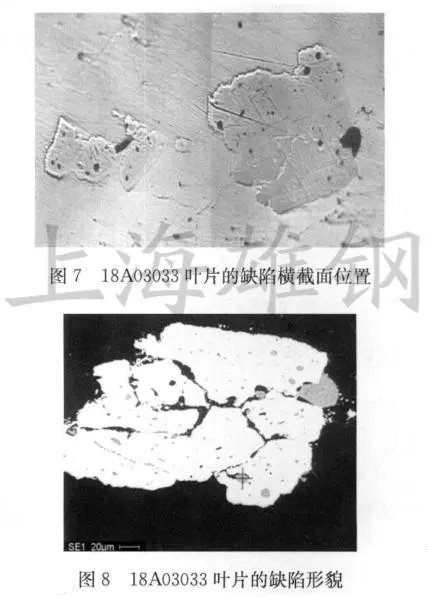
由以上分析可知,X光显示缺陷均为钨夹杂,其中18A01087叶片暴露于表面的缺陷呈不规则块状,缺陷与基体界限分明,但未见分离现象;18A01035叶片缺陷均呈“海绵”状,缺陷和基体相互包容,交界处未见分离现象;18A03033叶片两个缺陷呈不规则固体形态,大块中间有破碎现象,缺陷与基体界限分明,但未见分离,缺陷和基体交界处成分有互溶现象。
3.2钨夹杂的成因分析
钢厂现行GH4049合金冶炼工艺为真空感应加电渣重熔,并采用小炉配大炉的生产工艺,根据其工艺要求电渣重熔电极需要四根合金锭焊接成一支电极进行。即采用200kg真空感应炉熔炼浇注成φ80mm电极棒,每炉三支电极棒和成分相近的、另一炉的一支电极棒通过手工钨极氩弧焊连接一起。GH4049合金中含有5.0%~6.0%的钨,但是在真空感应熔炼时,钨是以W30%,Ni70%的Ni-W中间合金形式加入,熔炼时有足够的时间熔化,况且电渣重熔只是电极重熔而已,不再加入钨或钨的中间合金,因此可以肯定合金冶炼时不会产生高密度钨夹杂,钨夹杂只能是在焊接电极时产生。导致焊接电极时产生高密度钨夹杂的可能性有两种:一是由于操作不慎钨丝粘在电极棒上;二是钨极蒸发沉积到陶瓷管内边缘,沉积较多时被氩气吹入到焊缝中而带入。以上两种情况都可将高熔点钨带到电渣重熔中,3380℃熔点的钨不可能完全熔化而保留在钢锭中,在棒材锻轧过程中沿纵向被拉长成长条状。一般钨丝粘在电极棒上的表现为实体状形态;钨极蒸发沉积到陶瓷管内边缘的表现为疏松状形态。在理化解剖钨夹杂叶片的金相图上,这两种形态的钨夹杂都存在,进一步证明上述两种产生高密度钨夹杂的可能性同时存在,是导致GH4049合金产生高密度钨夹杂的根本原因。
4钨灯丝X射线检查试验
为验证X射线对钨夹杂检测的灵敏度,从25W的灯泡中取出两段长约4~5mm的钨丝(其直径为φ0.01mm),将其分别放在成品叶片的进排气边、叶身及箍段上。经X射线透照,在底片上均可见白亮的钨丝影像,具体透照参数及试验中射线照相的相对灵敏度见表2。
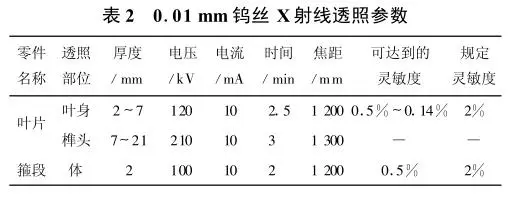
5结论
(1)通过对含钨夹杂的GH4049材料零件的X射线检查可以看出,由于钨的密度较基体高很多,使得透射射线的强度相差很大,在X光底片上钨夹杂的影像呈现很亮的白点、连续或断续的线等,极易分辨。而且X射线底片无论从黑度上,还是从影像质量上都完全符合标准规定的黑度要求。如对于厚度为2~7mm的叶身,像质指数可达到15;对厚度变化较大的榫头(最厚处约21mm),像质指数可达到13。从表2中可以看到,对所选择的透照参数,零件底片影像上的像质指数(灵敏度)均高于X射线照相检验标准中规定的要求,采用X射线检测高温合金中的钨夹杂是完全可行的。
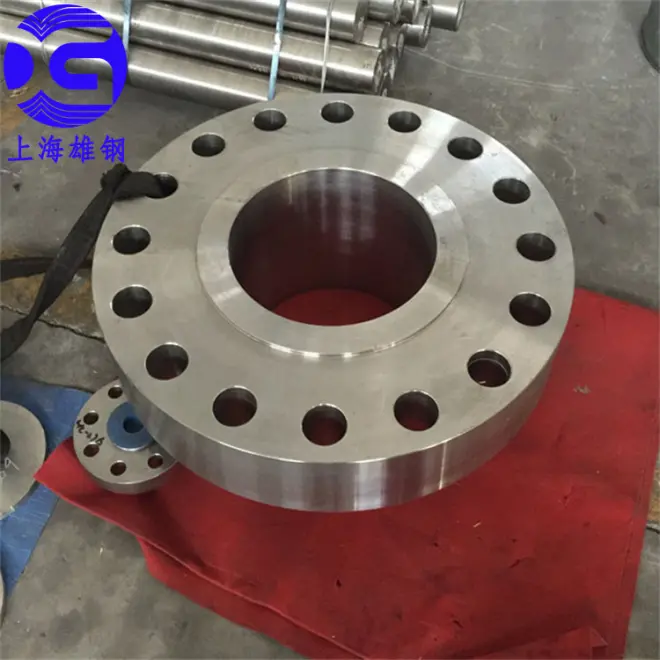