一种新型3D打印可能会将该技术带入主流
A new type of 3D printing may bring it into the mainstream
一种新型3D打印可能会将该技术带入主流
It is to the old version as the printing press is to the pen
这种技术之于旧版,就像印刷机之于笔
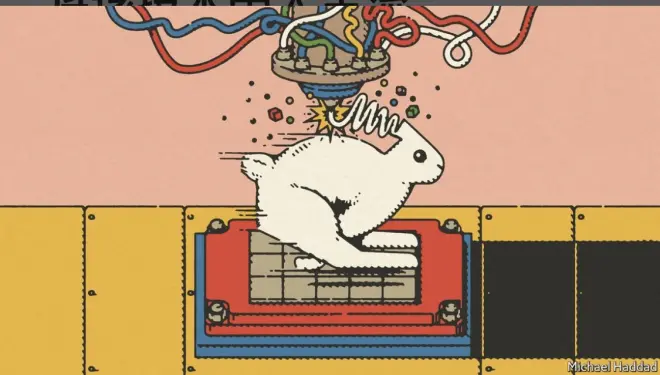
EARLY FORMS of additive manufacturing, or 3D printing as it is popularly called, began to emerge in the 1980s. But it took more than a decade for the technology to start taking off. Initially, it was used to make prototypes. Now, intricate components are routinely 3D-printed in plastic and metal, for use in products ranging from jet engines and robots to cars.
增材制造有个通俗的名字叫3D打印,它的早期形式始于上世纪80年代。但这项技术经过十年多才真正起步。起初,它被用于制作原型机。现在,人们已在常规化地使用3D打印制造复杂的塑料和金属部件,用于喷气发动机、机器人、汽车等各种产品。
Sales of 3D-printing services and machines grew by more than 17% in 2021, to reach around $15bn, according to preliminary estimates for a report by Wohlers Associates, a firm that tracks the industry. However, as useful as additive manufacturing has become, it struggles to compete on cost and speed with more established ways of making things, such as injecting molten plastic into moulds or stamping out metal parts with a giant press.
追踪这一行业的公司Wohlers Associates在一份报告里初步估计,2021年3D打印服务和设备的销售额增长了17%以上,达到150亿美元左右。不过,尽管增材制造已变得很实用,但它在成本和速度方面仍难与更成熟的制造方式匹敌,比如注塑成型或是用巨型压力机冲压出金属零件。
As a result, most manufacturers use 3D printers to produce low-volume, high-value parts. The extra time and expense this takes can be worth it for certain items. Making things additively produces objects layer by layer, so tricky internal structures can be incorporated more easily into a design. Shapes can also be optimised for strength and lightness, saving materials. But what if these advantages could be had at the speed and cost of conventional factory processes? A new form of additive manufacturing aims to do just that.
因此,大多数制造商用3D打印机来生产数量少、价值高的部件。对于某些部件来说,多花些时间和费用是值得的。增材制造是逐层生成物件的,所以就更容易将复杂的内部结构整合成一整个设计。还可以优化形状以满足强度和轻巧度的要求,节省材料。但是,如果既能有这些优势,又能兼具传统工厂加工的速度和成本呢?一种新型增材制造就是要做到这一点。
The origin of this process, trademarked “Area Printing”, goes back to 2009. That was when James DeMuth, having finished his master’s degree in mechanical engineering at Stanford University, started work at the National Ignition Facility, part of the American Department of Energy’s Lawrence Livermore National Laboratory (LLNL). This uses some of the world’s most powerful lasers to study nuclear fusion.
这项注册名为“区域打印”的工艺可以追溯到2009年。当时詹姆斯·德穆思(James DeMuth)在斯坦福大学获得了机械工程硕士学位,开始为国家点火装置(National Ignition Facility)工作,该装置隶属于美国能源部的劳伦斯利弗莫尔国家实验室(Lawrence Livermore National Laboratory,LLNL)。它用世界上最强大的一些激光来研究核聚变。
One of the challenges Mr DeMuth was given was to find a way to use a highly specialised type of steel to manufacture a 12-metre wide fusion chamber containing many complex features. He considered a form of 3D printing, called Laser Powder Bed Fusion (L-PBF), for the job. This employs a laser beam to weld together particles on a thin bed of powdered metal, to form the required shape of the object’s first layer. Then more powder is added and a second layer is welded on top of the first. And so on, until the item is complete.
德穆思接到的任务之一是要想办法用一种非常专门化的钢材建造一个12米宽的包含诸多复杂特征的聚变室。他考虑使用一种被称作激光粉末床熔合(Laser Powder Bed Fusion,L-PBF)的3D打印技术。它用激光束将薄薄一层金属粉末中的颗粒烧结在一起,形成物体第一层所需的形状。然后添加更多粉末,在第一层上面烧结第二层。以此类推,直至整个构造完成。
The problem is that, as with most other forms of 3D printing, there is an inverse relationship between resolution, which governs the level of detail that can be printed, and the speed of the process. Hence, some large components with fine details can take days, if not months, to print. Producing the chamber looked as if it might take decades. L-PBF was clearly unfeasible for such an application.
问题是,与大多数其他类型的3D打印一样,精度(可被打印的细节水平)和打印速度呈反比关系。因此,打印一些构造精细的大型组件可能需要几天甚至几个月。建造这个聚变室看起来要花上几十年。在这种情况下用L-PBF显然不可行。
This got Mr DeMuth and a group of colleagues thinking about how to speed things up without compromising quality. After some work, they started using a device called an optically addressed light valve, which had been developed at LLNL. This permits a pulsed infrared laser, with its beam shaped to have a square cross-section, to be patterned with a high-resolution image. Working a bit like a photographic negative, the image can block or pass light, creating millions of tiny laser spots, much like the pixels that make up a digital image.
这促使德穆思和他的一帮同事思考如何在不影响质量的情况下加快速度。一番研究之后,他们开始使用LLNL开发的一种设备,名叫光寻址光阀(optically addressed light valve)。这个设备让脉冲红外激光器发出的激光束(截面呈正方形)按照一幅高分辨率图像来构成图案。图像的作用有点像照相底片,可以阻挡激光或是让激光通过,从而产生数百万个微小的激光点,就像组成数字图像的像素一样。
When projected onto a bed of powder, this patterned laser light can weld a complete area in one go. Mr DeMuth likens the process to producing documents with a printing press instead of writing them out individually with a pen.
当激光投射到一层粉末上时,按预定图像透过的激光可以一次性烧结一个完整的区域。德穆思将这一过程比作用印刷机生成大量文件,而不是用笔一份份写出来。
Not such a dotty idea
这点子可不疯
In 2015 Mr DeMuth co-founded Seurat Technologies, to commercialise the technology. This Massachusetts-based firm is named after Georges Seurat, a post-impressionist French artist who pioneered a painting style called pointillism that builds pictures up from dots. Several companies, including GM and Volkswagen, a pair of carmakers, Siemens Energy, a division of a large German group, and Denso, a big Japanese components firm, have partnered with Seurat to explore the use of its first prototype area-printing machine.
2015年德穆思和其他人一同创立了修拉科技(Seurat Technologies),将这项技术商业化。这家总部位于马萨诸塞州的公司以乔治·修拉(Georges Seurat)的名字命名。修拉是一位后印象派法国艺术家,他开创了一种叫做点彩的绘画风格,用点组成图画。有几家公司已经与修拉科技合作,共同探索使用其首款区域打印机的原型机,其中包括汽车制造商通用和大众,德国大型集团西门子的子公司西门子能源以及日本大型零部件公司电装(Denso)。
This prototype produces a series of small, patternable squares on the powder bed. Their size depends on the material. Aluminium requires 15mm squares. Titanium requires 13mm. Steel requires 10mm. Individually, these squares might seem small. But 40 of them can be printed adjacent to each other every second, so a large area can be covered quickly. The prototype was designed to work at this scale to keep the size of the laser and the amount of energy it consumes to a practical level.
这个原型机在粉末层上生成一系列可以制作图案的小正方形。方形的大小取决于材料。铝需要15毫米的方形。钛需要13毫米。钢需要10毫米。这些正方形单个来看可能很小,但是每秒钟可以打印40个相互邻接的正方形,所以能快速覆盖大面积区域。该原型机以这种规模工作,就可以将所用激光器的大小和所消耗的能量保持在合理可行的水平上。
With the equivalent of 2.4m pixels projected in each square, the machine can print parts with layers just 25 microns (millionths of a metre) thick at a rate of 3kg an hour. This is ten times faster than a typical L-PBF machine at such a fine resolution, says Mr DeMuth. Production versions of the area printer are now being built, and future generations of the machine should end up being 100 times faster.
这台机器在每个正方形上投射了240万个激光点,以每小时3千克的速度、每层仅25微米(百万分之一米)的厚度打印零件。德穆思说,在如此高的精度下,它比一般的L-PBF机器快10倍。这款区域打印机的量产机正在制作中,未来几代的机器应该会快100倍。
All that, says Mr DeMuth, means area printing will be competitive with mass-production factory processes, such as machining, stamping and casting. As an example, he believes that by 2030 it will be possible to produce silverware (utensils that nowadays are made from stainless steel) for $25 a kilo. “That means we could actually print silverware cheaper than you could stamp them out,” he adds.
德穆思表示,这一切意味着区域印刷将能与大规模生产的工厂工艺竞争,如机械加工、冲压和铸造。比方说,他相信到2030年有可能以25美元一公斤的价格生产不锈钢餐具。 “这意味着我们打印餐具的成本其实比冲压生产要低。”他补充道。
Other laser-based 3D printers are getting faster, too. L-PBF machines, for example, may be fitted with several beams—though the complexity involved could limit their number. And many non-laser ways to print things are improving as well, using all manner of materials to make items ranging from buildings to bridges to biscuits. One way or another, then, 3D printing seems at last to be ready to give traditional factories a run for their money.
其他基于激光的3D打印机也越来越快。例如,L-PBF机器也许可以安装多个激光束——不过数量不能太多,不然结构就太复杂了。许多非激光的打印方法也在改进,用各种材料来制作从建筑、桥梁到饼干的各种东西。无论如何,3D打印似乎终于准备好与传统工厂竞争了。