滚刀的加工效率与滚刀参数及齿轮结构有什么关系?
在齿轮的大批量生产中滚刀的结构尺寸将影响其加工效率,一种滚刀的好用与否,只能针对某种加工场合而言!而没有一种滚刀在任何一种加工场合下都能发挥其最高效率!
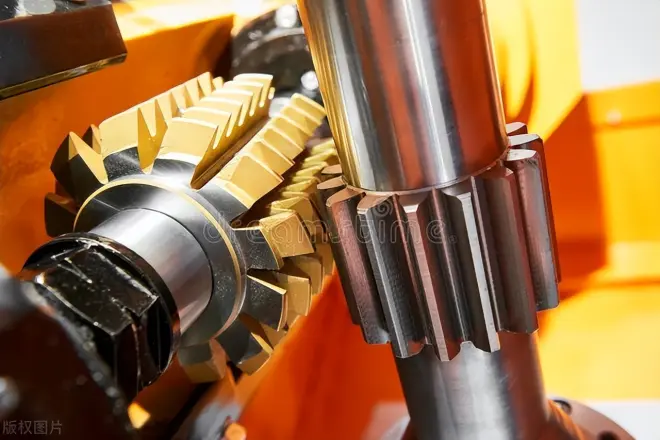
在选择滚刀时,要根据不同的加工对象来确定滚刀的结构尺寸,以达到机床的占用成本和刀具消耗成本最低, 加工质量又能达到工艺要求的水平. 这也要考虑被加工齿轮的材料及热处理条件, 所用机床的状况和装夹条件等相关因素:
不同结构尺寸的滚刀,效率区别很大
实例1:
模数Mn1.35 齿数Z59 齿轮的外圆直径 91.25mm, 全齿高 3.88mm;
选择一:滚刀外径Ø70mm,16槽的单头滚刀, 轴向走刀量为2.13mm/工件转, 切削速度是73m/min, 单件工时为1.5min, 在串刀部份的每一个刀齿切削长度是2.55米齿长.
选择二:Ø70mm, 11槽, 4头的滚刀加工,轴向走刀量2.2mm/每转, 切削速度不变, 单件的加工时间是0.35min. 串刀部份每一刀齿的切削长度可达到5米左右;
实例2:
本例加工齿轮模数 10, 齿数23, 螺旋角13度, 外径260.4, 齿宽290mm, 全齿高24mm,
选择一:滚刀外径Ø240mm, 14槽的单头滚刀, 切削速度45m/min, 轴向走刀量1.42mm/转,单件的加工工时为85分.
选择二:滚刀外径保持不变,增加槽数到21槽,改为双头滚刀, 仍然采用45m/min的切削速度, 走刀量可采用3mm/转.。此时齿形的包络误差为0.003mm, 加工走刀痕迹的深度也不超过0.003mm,完全满足精加工的要求.。单件的加工时间缩短到24分.。
从上面两种计算结果可看出, 加工同一种齿轮,选用不同结构的滚刀,选择不同的切削用量,其加工效率存在明显的区别。
切削参数选择注意事项
当工艺系统的刚性不佳时,将不能使用理想的切削用量。有时会遇到机床采用大于2mm的走刀量就会产生巨大的噪声,使得操作人员望而生畏! 并造成齿形和齿向精度的严重超差。
采用多槽多头的滚刀要配用适应的机床,否则不能采用大的走刀量,提高不了加工效率, 机床不能自动窜刀,或窜刀的长度很短短,刃长较长的滚刀不能全部得到充分使用,虽然刀具费用提高了, 但加工齿轮的数量不能增加, 相对增加了刀具的成本!
刀具结构对切削用量的影响
刀具结构尺寸对选择切削用量的影响是经常被忽略的,那么如何按所加工齿轮的条件来确定合适的滚刀结构尺寸,使其适应所用的机床, 实现加工效率,加工精度和刀具成本三者统一?
要实现这一目的, 除要清楚齿轮的结构,机床和工件装夹的状况外,了解切齿三大切削参数的选择原则是必需的:
1.切削深度对刀具耐用度的影响最小,首先要选择尽可能大的切削深度,绝大多数滚削是采用一次走刀切至全齿深,除非有较严格的齿面粗糙度限制才需增加精切序。
2.走刀量. 对刀具寿命影响最大的是切削速度! 切削速度是与刀具材料及其涂层和被加工齿轮的材料,热处理及模数相关。根据不同的刀具材料推荐的滚削速度很容易找到,根据上述条件选用滚削速度是很有效可行的办法。影响走刀量选择的因素较多, 走刀量对加工效率的影响很大, 同时走刀量的选择又受到滚刀结构的牵制. 根据齿轮结构参数确定加工该齿轮的刀具结构, 使其能够采用尽可能大的走刀量,以保持正常刀具消耗的情况下提高加工效率。
表一. 推荐的轴向走刀痕迹深度
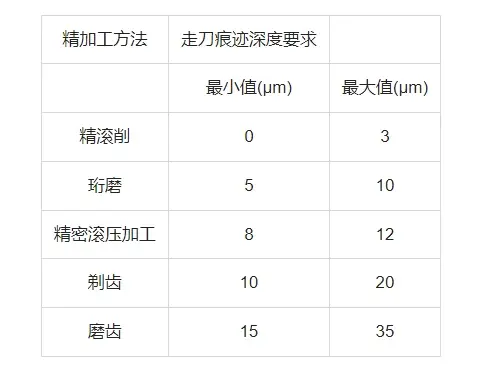
工件表面粗糙度将影响滚削的走刀量的选择, 滚削的生成表面必须达到后序加工的工艺要求 或在表一中选取走刀痕迹深度的允差 以确定所用的走刀量。
表二. 当前常用材料的滚刀可采用的滚刀齿顶切屑厚度
对此感兴趣的小伙伴可以私信我,获取完整版内容。
我是woodykissme,定期分享有关,机械传动及齿轮加工方面的内容,对这方面感兴趣的小伙伴,可以关注我。希望能够与大家讨论一下:
齿轮的设计及加工方法,加工齿轮所用的刀具设计、制造及使用方面的相关问题。
齿轮刀具设计计算方法,相关应用程序的开发,CAD二次开发自动绘图等的相关技术问题。
刀具应用方面,刀具的切削参数、涂层和使用寿命,加工中遇到的问题和解决办法等问题。
今天就分享到这,感谢您抽出宝贵的时间阅读!