H13模具钢回火工艺对渗氮层的影响
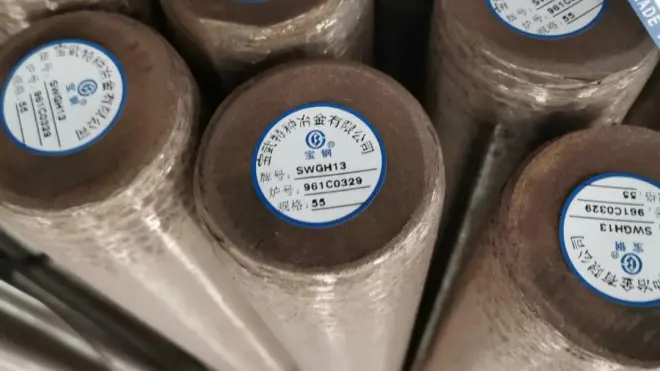
H13模具钢回火工艺对渗氮层的影响
摘 要:用光学显微镜 、扫描电镜及 X 射线衍射仪等研究了淬火 +不同回火工艺处理 H13 模具
钢再经相同气体渗氮处理后的渗层组织, 用显微硬度计测试了渗层横截面的硬度, 分析了回火工艺对渗氮层的影响。
结果表明:经淬火+两次 350 ℃回火的试样再渗氮后渗层较致密, 硬度变化较平缓, 但渗层厚度低于淬火 +两次600 ℃回火后渗氮试样的;淬火+两次 600 ℃回火试样渗层的化合物层下有微裂纹, 硬度变化较大;而淬火态直接渗氮试样未能获得具有良好综合性能的渗层。
关键词:H13 模具钢 ;回火;渗氮层
引 言
H13钢是一种重要的热作模具钢, 具有优良的热强性、塑韧性 、抗氧化性及热疲劳抗力 。为了提高模具的表面硬度 、耐腐蚀 、抗粘结等性能, 通常需要对其进行表面渗氮处理, 在保持模具心部原有强度与韧性的同时再有效提高模具的表面强度。
为了获得渗氮后模具心部与表层性能的良好配合, 渗氮前都应对模具进行适当的热处理, 其一般为淬火 +两次高温回火。但高温回火易使热作模具钢发生热磨损和坍塌失效 ;而采用 350 ℃左右的中低温回火后, 心部具有较好的强韧配合和热疲劳性能,同时也不会出现蓝脆现象。
经 580 ℃高温回火与经 350 ℃中低温回火的同种模具使用寿命相当, 但经高温回火的模具在使用过程中有早期失效现象,而中低温回火因存在较高含量的残余奥氏体, 对提高其韧性有一定的作用 。
但关于中低温回火是否适合作为渗氮前的热处理, 一直缺乏系统的研究, 而这将直接影响实际生产成本与生产效率。为此, 作者对渗氮前进行淬火 、淬火+两次中低温回火 、淬火 +两次高温回火三种不同热处理( 主要是回火工艺不同) 的 H13 钢渗氮层的组织与硬度进行了研究, 分析了回火工艺对渗氮层的影响, 为实际生产工艺的制定提供参考。
1 试样制备与试验方法
1 .1 试样制备
试验材料为退火态的 H13 钢, 取自上海渊钢公司, 其 名义化学成 分( 质量分 数/ %) 为 0 .32 ~
0.45C, 0 .8 ~ 1 .2Si, 0 .2 ~ 0 .5M n, 4 .75 ~ 5 .5Cr, 1 .1~ 1 .75M o, 0 .8 ~ 1 .2V, ≤0 .03P, ≤0 .03S 。
采用线切割加工成 10 mm ×10 mm ×40 mm 的试样 。经1030 ℃盐浴保温 10 min 、油淬冷却后, 在箱式电炉内分别进行 350 ℃×2 h 、600 ℃×2 h 两次回火,采用铸铁屑、木炭、砂子( 质量比为 2 ∶2 ∶1) 的混合物作防脱剂, 将试样埋于铁盒中加热。试样淬火态硬度为 57 HRC, 经 350, 600 ℃回火后硬度分别为53.9和48.0HRC 。
渗氮前试样表面经 1000#金相砂纸磨光 、酸洗、水洗及无水乙醇清洗、吹干。渗氮工艺采用气体渗氮, 渗氮介质为氨气, 流量为 500 ~ 1 000 L ·h-1, 炉内压力为 1 .3 ~ 1 .6 kPa, 其它工艺参数如图 1 所示。
1 .2 试验方法
将渗氮后试样用线切割成 10 mm ×10 mm ×10 mm的 4 段, 分别进行不同测试。试样经镶样、抛光和饱和苦味酸酒精溶液中侵蚀后, 用蔡司光学显微镜和FEI QUAN TA-200 型环境扫描电镜( SEM) 分析显微组织和测量渗氮层的厚度;用扫描电镜附带的能谱仪( EDS) 分析渗氮层的成分;用 SIEM ENSD5000型X 射线衍射仪( XRD) 分析渗氮层表面的物相组成,铜靶, 扫描角度10°~ 90°, 管电压 35 kV, 管电流30 mA, 时间 0 .2 s, 采样间隔 0 .02 s ;用 401MVA 型显微硬度计测试渗层截面上由外向内 6 个不同点的显微硬度, 载荷 0 .98 N, 保载 10s 。
2 试验结果与讨论
2 .1 显微组织
由图 2 可知, 各试样的显微组织都由心部的回火马氏体和表层的氮化物组成。淬火 +渗氮试样的渗氮层最薄, 仅 30 ~ 40 μm, 淬火 +350 ℃回火 +渗氮试样的渗氮层厚为 50 ~ 60 μm, 高于前者的, 但低于淬火 +600 ℃回火 +渗氮试样的( 70 ~ 80 μm) 。文献[ 4] 表明, H13 钢渗氮层形成合金氮化物的机理主要是含合金元素的碳化物与渗入的氮原子相互作用而在碳化物界面上形成的, 渗氮前回火温度越高, H13 钢中含合金元素的碳化物越多, 因此渗氮层越厚。
由图 3 可知, 三种试样渗氮层中化合物层的厚度依次约为 1, 2, 5 μm 。淬火 +渗氮试样化合物层组织呈粗大的条状, 较疏松 ;淬火 +两次350 ℃回火+渗氮试样化合物层的组织较细密 ;淬火 +两次600 ℃回火 +渗氮试样化合物层也较致密, 但是与扩散层交界处出现了裂纹, 这将导致化合物层在使用过程中容易脱落, 使模具表面粗糙度加大, 导致磨损加快, 从而造成早期失效 。渗氮前回火温度越高, H13钢中合金元素以碳化物形式析出越多, 铁素体中的合金元素越少, ε相的厚度随着铁素体中合金元素量的增加而减少[ 6 -8] , 因此回火温度越高,表面化合物层的厚度越大。
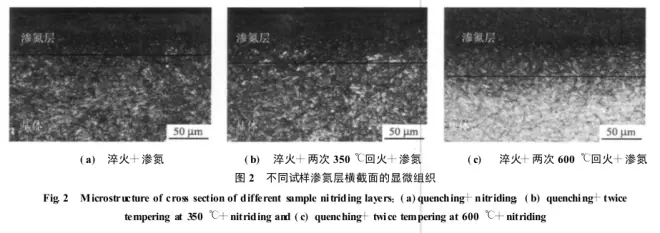

2 .2 硬度分布
由图 4 可知, 三种渗氮试样的表面硬度均比心部的有较大提高, 距离外表面约 20 μm 处的硬度分别为 840, 800, 870 HV( 换算为洛氏硬度分别为 65,64, 66 HRC) 。由表层到基体硬度逐渐减小, 淬火 +渗氮及淬火 +高温回火 +渗氮试样的硬度降低较快, 淬火+中温回火 +渗氮试样的硬度变化较为平缓, 这可保证模具钢在后续使用过程中不会因为硬度的突变而导致过早开裂失效。
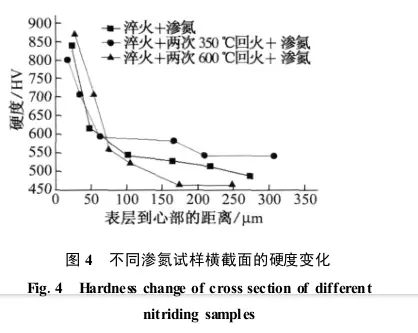
由表 1 和图 5 可知, 两种试样的氮含量由表层到心部是逐渐减少的, 即离表层距离越远, 氮含量越少。氮含量越高, 生成高硬度氮化物则越多, 这就是渗氮试样从表层到心部硬度变化的原因 。
表 1 不同试样不同微区的氮含量(质量分数)
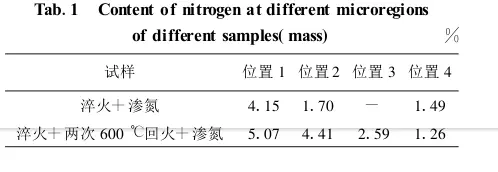
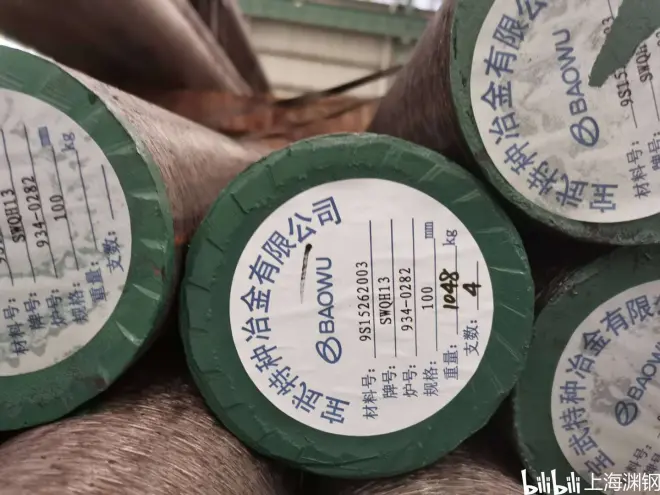