《创建精益文化》第十章(3 of 6)
*本翻译文本仅供学习、交流用途(原书出自:Creating a Lean Culture_ Tools to Sustain Lean Conversions (2014, CRC Press),by Mann, David)

第十章、快速解决问题和改进流程
结构化的解决问题的流程
把追求完美作为目标是一回事,而把允许你向目标前进的工具落实到位是另一回事。结构化的问题解决流程是这个旅程中的重要一步。起初,这可能并不比要求人们在出现问题时运用五个为什么更困难。培训和指导一线领导传授五个为什么的问题解决方法,可以确保人们接受培训的内容与领导支持和加强他们的工作之间的一致性。更复杂的方法可以在后续学习。引入这些想法的最有效的方式往往是,带领人们逐一完成这些步骤,并且每个步骤都有紧随其后的实际应用。
稍后,或者最初,如果相关领导者的准备好了,如果你还不熟悉问题解决流程,可以找到六步法(或七步法或八步法)解决问题的流程,并学习如何使用它。与应用密切相关的传统培训可以发挥作用。或者,你可能只是想在情况需要时,一步步地开始要求这些步骤,并辅导你的领导如何执行每个步骤。根据你需要接触到的人数,当需要下一个步骤时,及时提供培训就足够了,而且这也是你的领导和团队成员最愿意学习的时机。无论你使用哪种品牌的流程,无论你如何培训人们,其基本步骤都是类似的:
步骤1:识别并定义问题。
步骤2:控制隔离问题并立即采取其他补救措施。
步骤3:让合适的、有相关知识的人参与进来。
步骤4:进行根本原因分析。
步骤5:确定根本原因解决方案,评估它们,并测试优先方案。
步骤6:实施针对根本原因的解决方案。
步骤7:根据性能数据监视和修改解决方案。
谁来做改进?
以原因分析为导向,一步一个脚印地追求完美,很快就会产生超出技术专业支持小组能力的改进机会。在传统的批量环境中,这只是让工程、质量、生产控制或其他人员,对生产车间领导提出的工艺改进要求进行工作的另一个典型瓶颈。这是因为在传统的组织中,改进是 "留给专家 "的。
在这种传统的情况下,技术项目团队进入生产区,然后离开并留下了旨在永久修复的东西。有时,这些修复只在纸面上发挥作用,在这种情况下,它们很快就消失不见了。然而,有时项目组的修复措施工作得相当好。但是,由于它的工作,没有得到进一步的关注。这个流程就一直保持不变,经常是多年没有任何改进。没有做出进一步的改变,这可能是因为领导者的心态(“它没有坏!”)使他或她看不到进一步的机会。或者,领导者可能不知道如何用他们自己的资源来领导改进工作。可能等待技术项目组回应的时间往往很长,以至于不值得发起请求。
短期、中期和长期的改进
在精益环境中,人们期望每个人都有两个责任。第一是每天管理和运行你的那部分业务,即使那只是单一的工作站。第二是不断改善业务,或为改善业务做出贡献。我们已经看到了这种双重责任的例子,那就是每天的责任制流程及其任务分配板。精益管理中的改进工作通常分为三类(根据经验在不同的类别之间变动),由改进任务的范围、规模和时间决定。表10.1列出了这些类别。
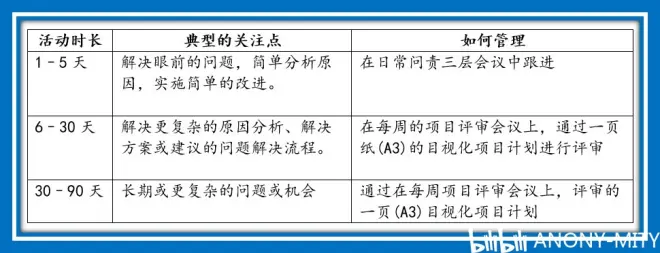
*注:虽然这些类别没有明确包括对员工的改进建议采取行动,但任何这样的建议都可以很容易地纳入这三者之一。第十一章详细介绍了员工改进建议体系。
简单的问题或直接的改进可以在日常问责流程三级会议上,进行分配和管理。例如,班组长可能被指派为目前放在抽屉里的工具制作影子板,这些工具在需要时经常丢失。或者,他或她可能被指派为橱柜门和架子制作标签,以识别存放在那里的材料和用品。有了影子板或标签,班组长可能会被指派创建简单的日常审核规则,以维持对“物有其位、物在其位”的遵守。下一个任务可能是更新班组长的标准化工作,包括以下项目:
在轮班结束时,确认工具已放回到指定的位置。
确认材料和用品在指定的地方,并根据需要补充。
建议未来的改进
从日常任务分配中进行初步调查的另一个结果是,为该区域未来的改善活动清单推荐项目。例如,对于装配线上的间歇性备份原因的调查发现,由于零件和材料的组织性差,造成了包装操作的中断,常常导致操作人员不得不离开工作站去寻找合适的材料。在这种情况下,开展了两次连续的针对包装区的组织、材料补充和零件展示的改善。这两次活动持续时间为一周,间隔约六周。第二次活动根据前一次实施的经验,完善了第一次活动的工作。同样,解决了一个问题就会发现其他问题,并有更多的机会去改进,这是很常见的情况。

翻译的过程也是再创作的过程,每篇文章的翻译都结合了我个人二十余年的精益学习、实践和理解。如果你觉得本翻译版本值得推荐,请注明出处,并使用本文链接。同时,如有不足之处,也非常欢迎大家批评指正。
如果你在阅读本文章后,有所收获或心得,欢迎大家在评论区,与大家分享。