技术篇 | 读了这篇文章,看谁还敢说不懂连杆(加工篇)
连杆加工工艺分析
连杆加工案例分享
连杆涨断工艺详说
连杆加工工艺分析
01孔精度
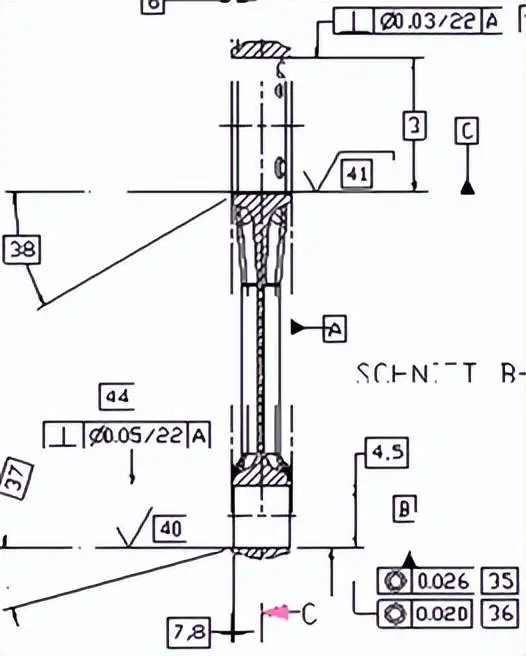
为了使大头孔与轴瓦,小头与活塞销能密切配合,减少冲击的不良影响和便于传热,大头孔于小头的衬套孔尺寸公差均为IT6.大头孔表面粗糙度Ra<0.8μm,衬套表面粗糙度Ra<0.4μm。
大头孔的圆度公差为0.005mm,圆柱度公差为0.01mm,小头压衬套的底孔的圆度公差为0.007mm,圆柱度公差为0.015mm小头衬套孔的圆度公差为0.004mm,圆柱度公差为0.008mm.
02平行度
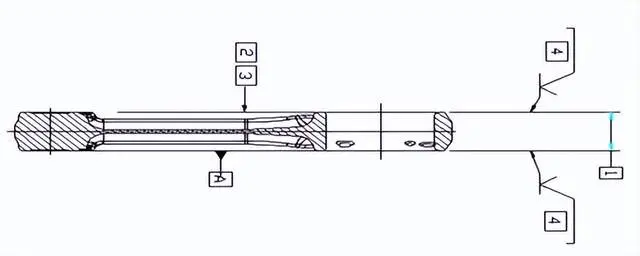
两孔轴心线在连杆轴线方向的平行度误差会使活塞在气缸中倾斜,从而造成气缸壁磨损不均匀,同时使曲轴的连杆轴径产生边缘磨损,两孔轴心线在连杆轴线方向的平行度要求较高。而两孔轴心线在垂直于连杆轴线方向的平行度误差不均匀磨损影响力小,因而其公差值较大。
此处规定为:两孔轴心线在连杆轴线方向的平行度在100mm长度公差为0.03mm。在垂直度连杆轴线方向的平行度在100mm长度上公差为0.06mm.
03中心距
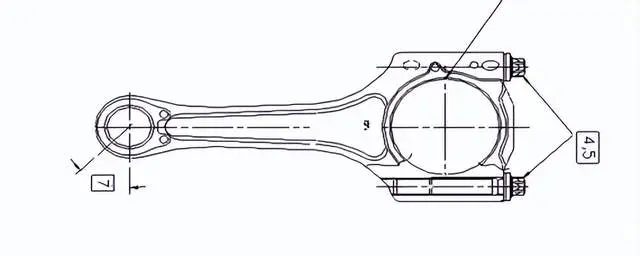
大小头孔的中心距影响到气缸的压缩比,即影响发动机的效率,所以规定比较高的要求:180±0.05mm.
04轴心线的垂直度
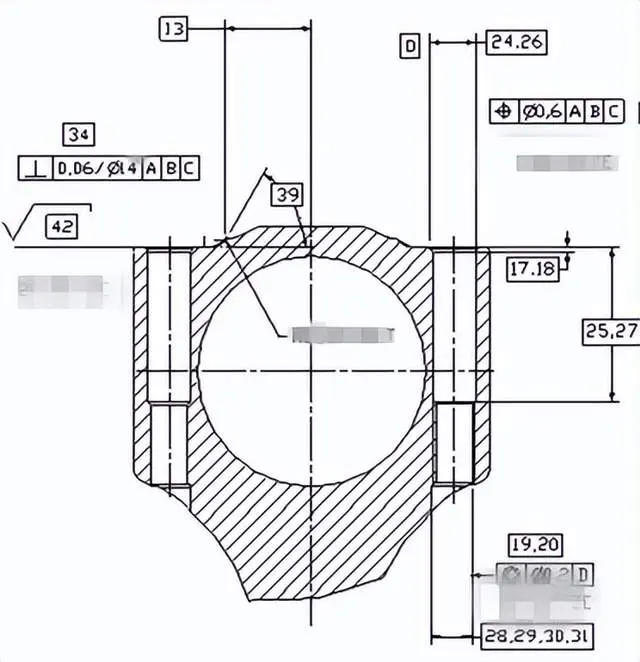
大头孔两端孔对大头孔轴心线的垂直度影响到轴瓦的安装和磨损;同时,这个垂直度在加工过程中将影响到加工小头孔两端面时的定位精度,所以对它也提出了一定要求;大头孔两端面对大头孔轴心线的垂直度在100mm长度上公差为0.1mm.
05螺栓孔
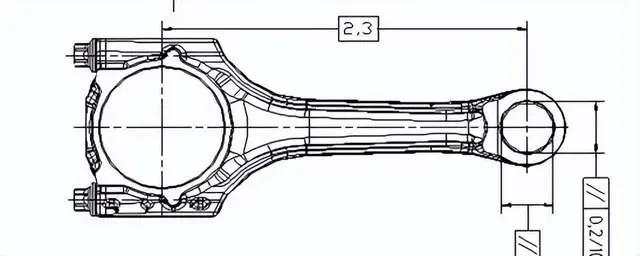
连杆在工作过程中承受着急剧变化的动载荷,这一动载荷又传递到连杆体和连杆盖的两个螺栓及螺母上。
因此除了对螺栓及螺母要提高的技术要求外,对于安装这动力螺栓孔及端面也提出了一定的要求;螺栓孔按公差等级IT8和表面粗糙度Ra<3.2μm,两个螺栓孔在互相垂直的两个方向的平行度在100mm长度上公差为0.15mm,螺栓孔两端面对螺栓孔轴心线的圆跳动在100mm长度上公差为0.2mm.
06结合面
连杆受动载荷时,结合面的歪斜使连杆盖及连杆体沿着结合面产生相对错位,使曲轴的连杆径和轴瓦结合不良,从而生产不均匀磨损。结合面的平面度将影响到连杆体,连杆盖和垫片贴合的紧密程度,因而也影响到螺栓的受力情况和曲轴,轴瓦的磨损.
连杆工艺流程
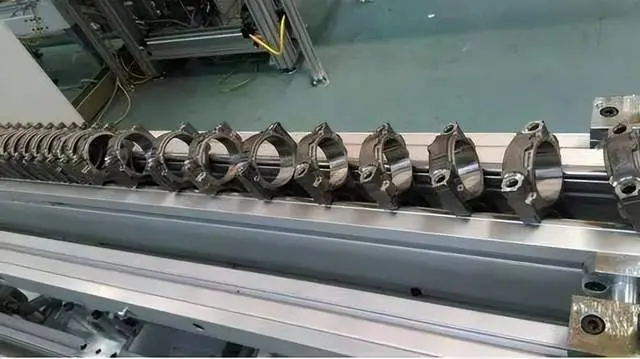
工艺流程简述(非标准):
两端面:粗铣 / 粗磨 / 半精磨 / 精磨.
小头孔:钻孔 / 扩孔 / 拉孔/
精镗 / 压入衬套后在精镗.
大头孔:粗镗 / 半精镗 / 精镗.
螺栓孔:钻孔 / 扩孔 / 铰孔.
连杆加工流程:
01OP10 粗/精磨
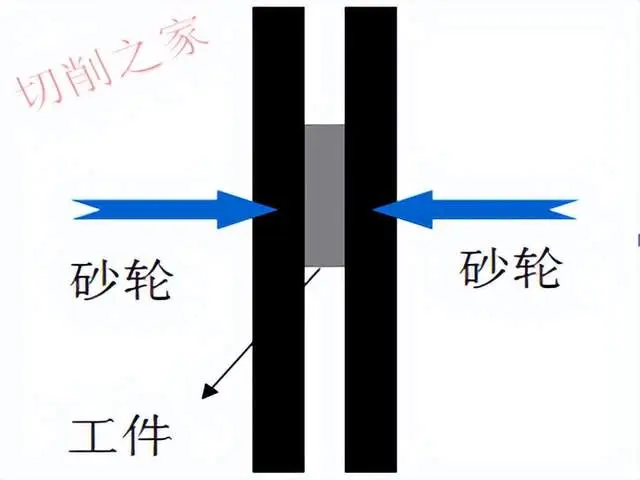
1.连杆通过一个传送带,被一个接一个的推入到进给盘的4个工件座内
2.连杆被推入到进给盘内工件座以后,随进给盘旋转到两片砂轮中间
3.在磨削第一个连杆端面期间,连杆通过2个砂轮的横向进给被加工,并且在运动出砂轮以前,砂轮停止向前进给,进行光磨
4.Marposs量仪负责测量工件厚度,并将测量值反馈给机床,用来自动补偿动力头的进给位置
02OP20 打号/螺栓角度等
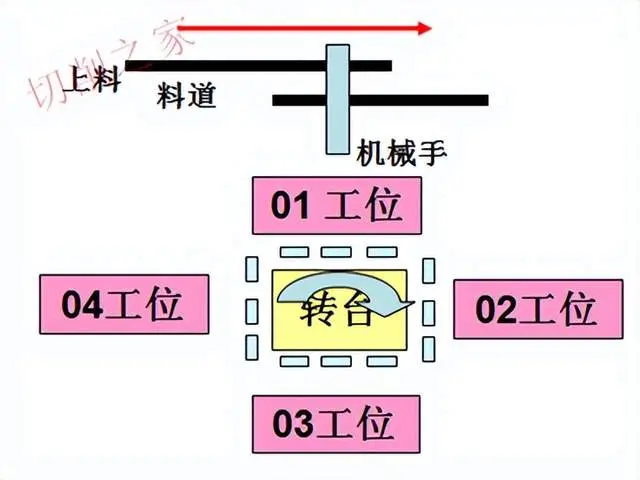
1.装夹毛坯检查是否夹紧,测量大小头孔并把测量值反馈给04工位
2.铣打号面及螺栓座面,粗镗大头孔并倒角,钻小头孔
3.工位负责钻阶梯孔、钻螺纹底孔、锪螺纹底孔出口的毛刺
4.攻螺纹、精镗大小头孔并倒小头孔两面倒角(两侧倒 角不一致
03OP30 涨断裂解
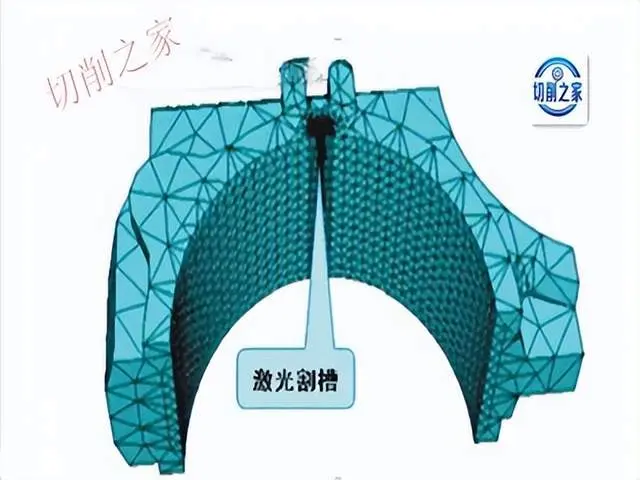
1.负责放置毛坯并测量连杆的裂解质量
2.激光分二次切割裂解槽
3.涨断裂解连杆
4. 装配螺栓并拧紧
5. 松开螺栓吹气清理连杆盖与杆之间的夹屑再次拧紧螺栓
6. 压装衬套并精整
04OP50精镗大小头等
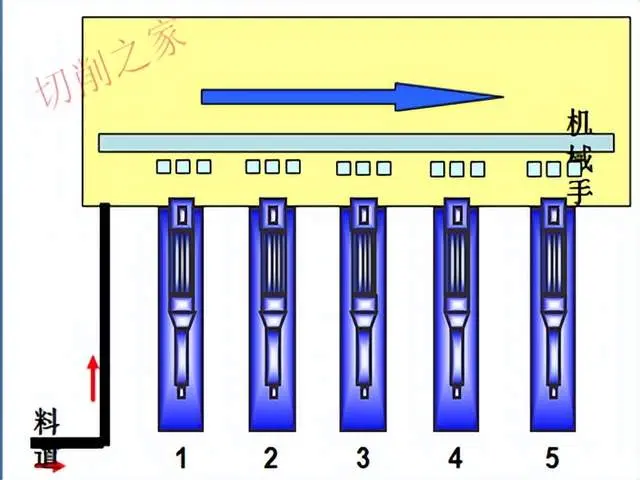
1. 上料并识别工件类型以及正反位置.
2. 先铣削工件标识面侧的小头阶梯,然后机械手将工件翻转铣削另外一面小头阶梯.
3.先铣削工件标记面侧小头楔形并小头孔倒角,同时初镗大头孔到工件中心线,然后机械手将工件翻转铣削无标识面小头楔形并小头孔倒角,同时初镗大头孔之中心线.
4. 对大小头孔进行精镗.
5. 对大小头孔进行测量并将测量值反馈给04工位,然后机械手将工件放下料道,不合格品剔除到不合格料道.
涨断工艺
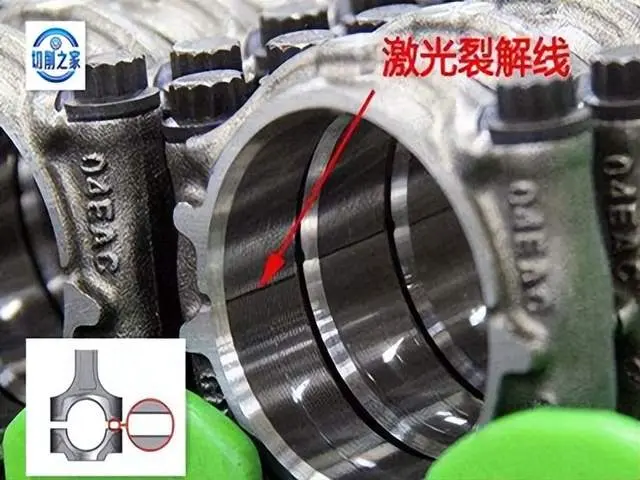
01涨断技术
一直以来无法精确地加工零件分离后的表面并组合一直是人们难以克服的问题,直到发明了涨断这种工艺方法,使得精确吻合及螺栓拧紧两断裂面成为可能。1995年,应用于连杆加工的革命性的激光涨断技术开始应用于欧洲市场。精确的激光刻痕及涨断力,使得精细的断裂面能够完美的组装到一起。
涨断技术极大的降低了成本并减少了50%的加工工序,与传统方法相比:机床投资低,材料成本低(仅1个毛坯),整个工艺的加工准备时间短。激光最大的优点在于不需接触材料表面即可进行加工,与拉削相比,激光不必接触工件就能为涨断工艺刻出所需的断裂线,因此没有任何道具的磨损。生产工艺的重复性和稳定性非常高。
另外,激光非常灵活,从而使用同一个激光器即能对各种各样的连杆进行最佳的切口加工。拉刀的寿命大约为400件,而激光光学透镜的寿命可高达1000000件.
02涨断特点
1.节省了连杆盖与连杆体的结合面的加工.
2.节省了螺栓定位孔的加工.
3.节省了连杆盖的单独输送.
4.凹凸不平的涨断面增大了连杆盖与连杆体的结合面的面积,这样增强了连杆总成在装机后的承载能力和抗剪切能力.
5.连杆体和连杆盖通过自然形成的涨断面组合装配,不但重复精度和定位精度好, 连杆大头孔的形状公差的精度(圆度、圆柱度)也保持得好.
6.通过统计和计算:与传统连杆加工方法相比,激光涨断技术可节省机床设备投资5%,减少机加工工序50%-60%,降低生产成本5%- 20%.
03注意事项
1、激光割槽原理:激光谐振器产出的激光束经导光系统中的镜片的反射、聚集后,成为功率密度极高的光束,该光束通过光纤电缆和喷嘴照射在连杆大头孔需要涨断的部位,金属开始熔化蒸发,形成激光割槽.
2、工艺参数的调整:我们通常通过调节激光的聚集点、脉冲波长和功率来控制激光割槽的深度及宽度。要定期检查激光割槽的深度,否则将影响涨断质量并加速涨断轴的磨损.
3、激光的性质:由于所用激光的强度等级为4级,是不可见光,容易灼伤皮肤和眼睛,在调整激光装置时应注意安全,必须佩带防护眼镜、穿白色工作服,以减少激光的漫反射的影响.
4、激光割槽对后续加工的影响:在激光割槽的过程中,由于激光束能量密度高,加工速度快,并且是局部加工,对非激光照射部位影响极小,热影响区也就小,所以,工件的热变形小,对后续加工(精缤、珩磨)的影响就很小.
Q&A
Q:OP20工序常出现的问题?
A:
1.转台涡轮由于扭矩过大断裂
2.连杆毛坯侧面状态不好,导致钻孔位置度不好
3.小头定位螺栓拧紧状态不好,加工状态不好
4.丝锥加工时排屑不畅,螺纹孔有铁屑
5.测量工位测量值超差,(测头或工件脏)上料工位工件类型错误.