GH3030镍基合金钎焊管接头裂纹分析
GH3030是早期发展的固溶强化型高温合金,在800℃以下具有满意的热强性和高塑性,并具有良好的抗氧化、热疲劳性和焊接工艺性能。它主要用于1100℃以下,要求具有抗氧化性,但承受载荷很小的高温部件"。某GH3030构件在试验过程中被发现有2个钎焊管在钎焊接头处发生泄漏。试验温度约为400℃,钎焊管在正常工况下受交变应力。2个钎焊管焊接结构和焊接工艺相同,但其中一个泄漏严重。钎焊管材料为GH3030高温合金,壁厚为0.2mm,外径为0.8mm,前室材料为GH3128高温合金,将前室钻头打孔扩到0.8mm左右(与钎焊管间隙约0.03mm)后通过钎焊(1050℃,6h)将管与前室连接,随后将前室与铜散热板钎焊连接,使用AgCu焊料。
本研究通过采用外观观察、裂纹宏微观观察、断口观察、能谱分析、金相检查、硬度检测等手段,确定2个构件钎焊管的裂纹性质,并对其失效原因进行综合分析,根据分析结果提出改进建议,以期为后续构件钎焊管的安全使用提供参考,对于同类钎焊管焊接过程的控制具有指导意义。
1试验过程和结果
1.1表面观察
发生泄漏的2个钎焊管(A、B)表面均发现裂纹,且裂纹均位于距铜散热板约1mm的钎焊管焊脚处。其中,构件A钎焊管可见明显开裂,开裂处表面暗于钎焊管表面,为焊料覆盖特征;构件B钎焊管焊接影响区颜色明显亮于钎焊管基体,并可见微小裂纹,裂纹附近侧表面也可见焊料覆盖(图1)。
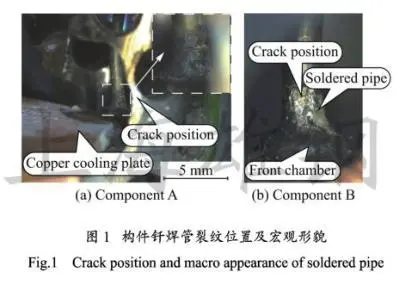
使用线切割将钎焊管取下,对其进行微观形貌观察和成分分析,结果见图2、表1。构件A钎焊管在开裂处已经完全断开,断口附近侧表面可见钎料堆积和与正常管壁的过渡形貌(图2a)。能谱分析可知:钎料堆积处(图2a中标注1)成分主要含C、O、Ag、Cu等元素,为焊料成分;过渡处(图2a中标注2)成分主要含C、O、Cu等元素,仍含有焊料成分。
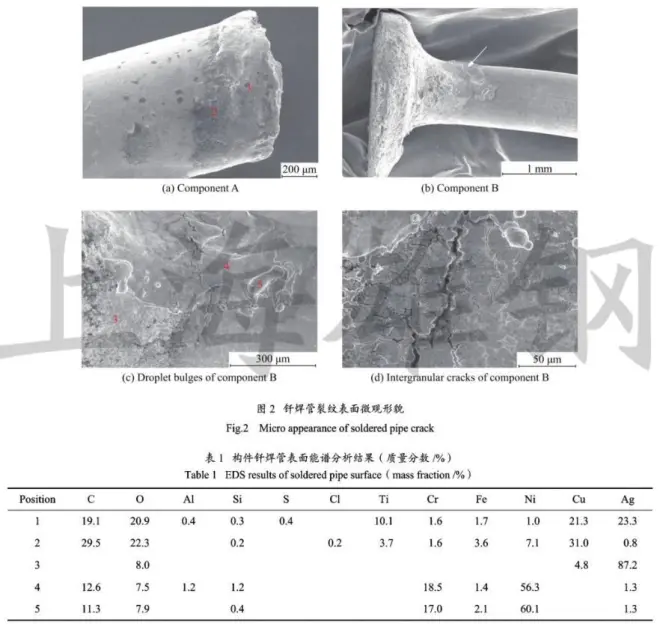
构件B钎焊管裂纹区域呈自由凝固表面形貌,裂纹较为曲折,并可见沿晶分叉形貌,主裂纹扩展方向为周向(图2b~图2d)。能谱分析可知:焊脚处(图2c中标注3)成分主要含Ag、Cu等元素,为焊料成分;裂纹两侧(图2c中标注4)成分主要含Ni、Cr等元素,并含有少量Ag、Fe元素,其中Ag应来源于焊料;裂纹附件可见一处自由凝固形成的熔滴突起(图2c中标注5),成分主要含Cr、Ni等元素,为钎焊管基体材料元素,说明该处的温度已达到GH3030的熔化温度。GH3030和GH3128合金的成分见表2。

1.2断口观察
对构件A钎焊管进行断口观察可见,整个断面较为平整,大部分区域为沿晶断裂特征。将断口分为4个区(图3a):断口1区为沿晶氧化特征,局部晶界氧化严重出现圆滑特征,并可见熔融颗粒形貌(图3b中标注6);断口2区除沿晶氧化特征外,断口内壁可见氧化颗粒形貌(图3c中标注8),中部可见剪切韧窝形貌(图3d);断口3、4区主要为沿晶氧化特征。由此可知,构件A钎焊管主要为沿晶开裂,且在焊接过程中已经产生,最后发生过载断裂。
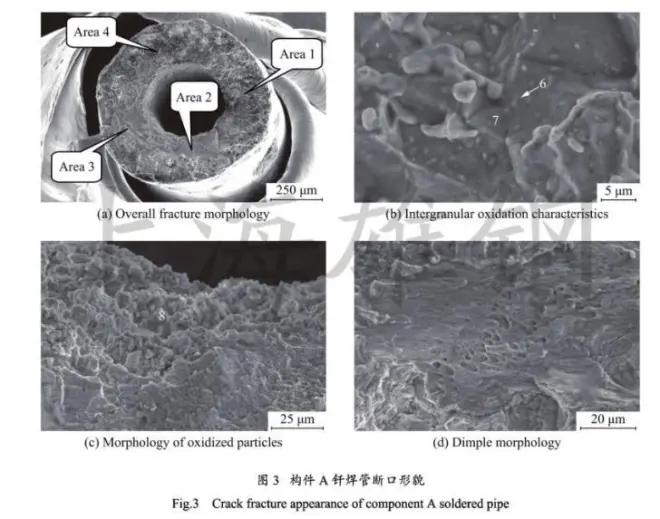
对应图3、图4中标注的位置,断口能谱分析结果见表3,由结果可知,构件A和构件B钎焊管沿晶断口局部均可见Ag、Cu等外来元素,说明钎焊管的原始裂纹在焊接过程中已经产生,性质均为过热沿晶裂纹,随后裂纹发生疲劳扩展后过载断裂或直接引起过载断裂。
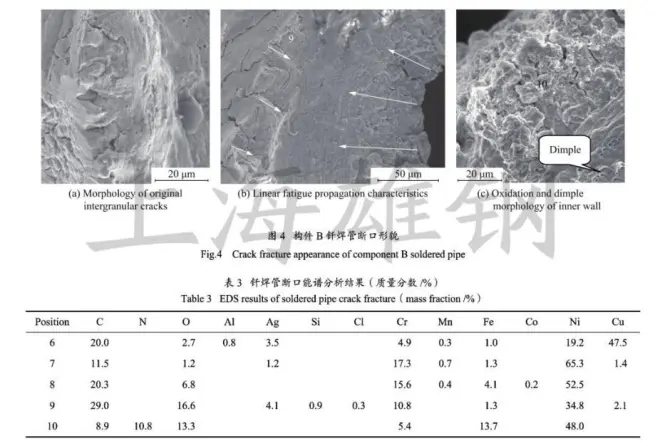
1.3组织观察
在构件A钎焊管断口处取纵向金相试样,对其组织进行观察,结果见图5,能谱分析结果见表4。在背散射图像下观察,在钎焊管断口钎料堆积处可见白亮相,钎料堆积深度最深达118um,钎料堆积处主要含Ni、Cu、Ag元素,为低熔点共晶相2(图5b中标注A)。断口附近可见沿晶开裂二次裂纹和晶界粗化形貌(图5c中标注B),晶界粗化区域可见Cu元素,局部晶界在背散射下为白亮色(图5c中标注C),此处的晶界含有Cu、Ag元素,这些均说明Ag-Cu焊料与GH3030合金发生了反应,且反应主要作用于晶界,晶界是腐蚀元素进入镍基合金基体的通道。钎焊管近表面处还发现有灰色颗粒状相(图5d中标注D),此处含有较高的Cr元素,应为高温形成的宫Cr相。
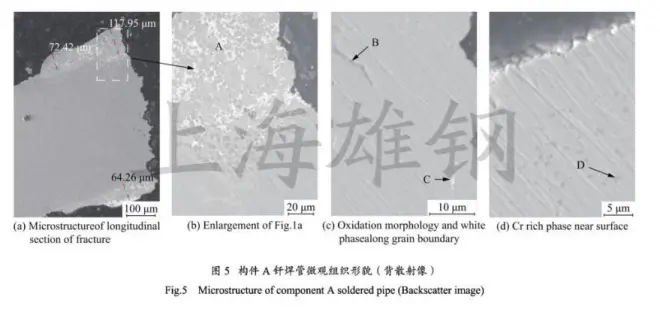
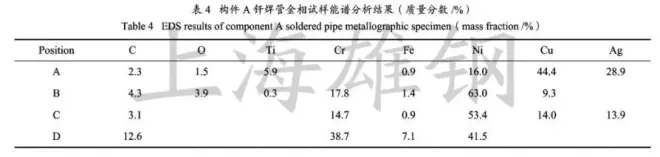
在构件B钎焊管断口附近取横向金相试样,对其焊接结构进行观察,实测前室孔的直径为0.8mm,GH3030钎焊管外径为758um,前室钎焊管之间为钎焊过渡区,前室与铜散热板的焊缝在背散射像下亮于两侧基体,呈“黑白条纹”状,为AgCu共晶组织,即黑色条纹为Cu,白色基体为Ag6。钎焊管内壁可见约10um的颜色变化区(对应断口上的内壁氧化区),变化区可见径向小裂纹(图6),能谱分析结果见表5,各基体材料成分与名义成分基本一致,前室钎焊管之间的钎焊过度区主要含Ni、Cr、Fe、Si元素,焊缝两侧的GH3030和GH3128成分中的Fe元素高于名义成分,应为钎料中的Fe元素反应扩散所致,钎焊管内壁的变色区其成分含有N元素,与钎焊管断口上发现的N元素相一致。
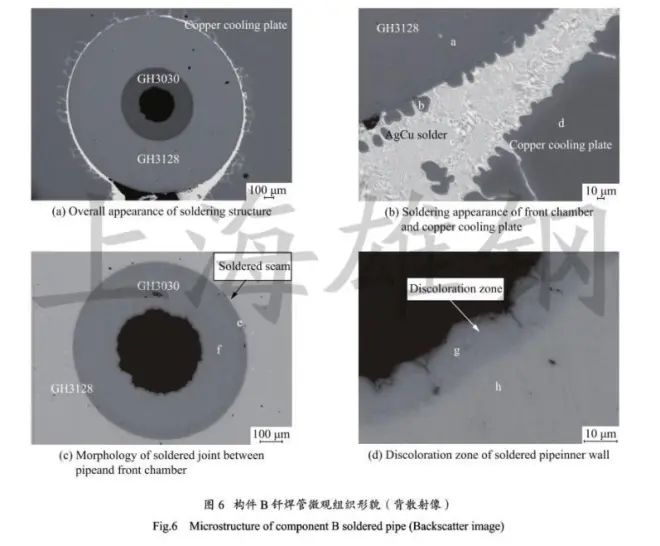
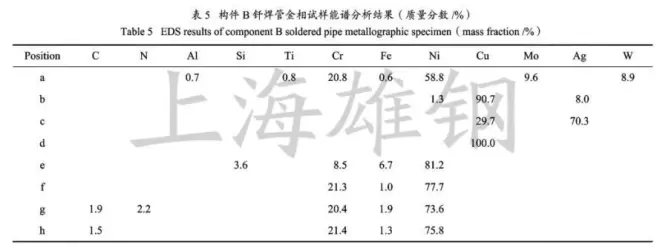
将构件A钎焊管纵向金相试样进行腐蚀后观察,可以发现,有焊料影响的区域晶界开裂情况严重,晶粒尺寸也大于正常晶粒,而远离焊缝的晶粒组织正常(图7)。
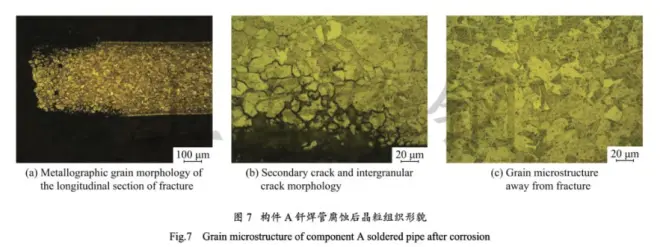
1.4显微硬度
对构件A钎焊管纵向金相试样的硬度进行检测,结果见表6,可知裂纹附近的硬度明显大于基体。
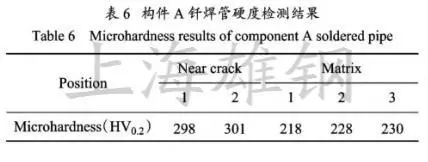
2分析与讨论
1)失效性质分析。
构件A钎焊管断口呈沿晶氧化特征,晶面存在熔融和氧化现象,为过烧特征7。晶面上有附着物,含有Ag、Cu、Fe等钎焊焊料中的元素,断口附近侧表面可见钎料覆盖,断口局部可见剪切韧窝形貌。因此,构件A钎焊管首先在焊接过程中发生高温沿晶开裂,随后发生过载断裂。
构件B钎焊管裂纹附近区域呈自由凝固表面形貌,裂纹呈沿晶分叉形貌,断口上裂纹对应位置发现少量的C1、Ag、Cu等钎料元素,局部有沿晶特征,说明构件B钎焊管在焊接时外表面已存在沿晶裂纹,同时钎焊管内表面也存在径向小裂纹,随后断裂在内、外壁表面裂纹处线性起源,并在交变应力下形成大量疲劳条带。因此,构件B钎焊管的裂纹性质为首先在焊接过程中存在沿晶小裂纹,随后发生疲劳扩展,最后在人工打开的外力作用下断裂。
2)失效原因分析。
2个钎焊管失效的共同点是均存在沿晶裂纹,且沿晶裂纹产生于焊接过程中。
从焊接工艺上看,钎焊是采用比母材熔点低的金属材料作钎料8,钎焊管和前室的钎焊温度为1050℃,高于钎焊管材料GH3030的固溶温度(980~1020℃),如钎焊过程温度控制不当,将会使钎焊管材料出现过热现象。构件B钎焊管裂纹附近的自由凝固表面也说明了焊接过程中局部温度超过了GH3030的熔点,该裂纹为金属过热过烧引起的沿晶裂纹。
从结构上看,2个焊接位置相距不到1mm,由于钎焊管尺寸细小,在第二次与铜散热板焊接的过程中极易产生焊料溢出甚至粘附在钎焊管表面的现象(2个钎焊管表面均有焊料粘附),这将对钎焊管的表面强度造成一定影响并增加其表面残余应力。同时,在高温条件下,Cu、Ag等焊料元素会沿晶界扩散,弱化晶界结合力,腐蚀后的晶粒组织形貌也说明了这一点。此外,铜散热板尺寸较大,距钎焊管的距离又近,铜散热板在工作中产生的应力可能会直接作用于钎焊管,应力集中区域的焊接缺陷是影响疲劳寿命最主要的因素10。如果将前室和钎焊管的焊接位置(焊接点1)与铜散热板焊接位置(焊接点2)的距离增大(图8),会从一定程度上改善焊接结构受力和焊接质量。
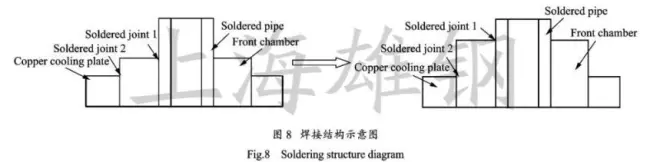
从环境上看,2个钎焊管断口内壁均行在教化特征,局部有小裂纹特征,金相图中也可见内壁仔在约10um的变化区及径向小裂纹,且这些位置
均发现有一定量的N元素,这说明:焊接气氛(氮气)对材料内壁表面状态及成分造成了一定影响,N元素渗人会使材料脆性增加.影响力学性能
综上所述,构件钎焊管的失效原因主要与焊接过程有关。构件A钎焊管大部分区域为沿晶特征,为高温沿晶开裂,最后发生过载断裂;构件B钎焊管在焊接过程中存在沿晶小裂纹,随后在交变应力作用下发生疲劳扩展,最后在人工应力下完全断裂。
构件钎焊管焊接裂纹的产生与2个焊接位置相距较近有关,焊接时存在互相影响,且存在焊接
温度控制不当的情况,建议严格控制焊接过程开对构件的焊接结构进行改进。
3结论
1)构件A钎焊管为高温沿晶开裂,最后发生过载断裂;构件B钎焊管在焊接过程中存在沿晶小裂纹,在交变应力作用下发生疲劳扩展,最后在人工应力下完全断裂。
2)构件钎焊管焊接裂纹的产生原因是2个焊接位置相距较近,焊接时互相影响,且存在焊接温度控制不当的情况。建议严格控制焊接过程并对构件的焊接结构进行改进。
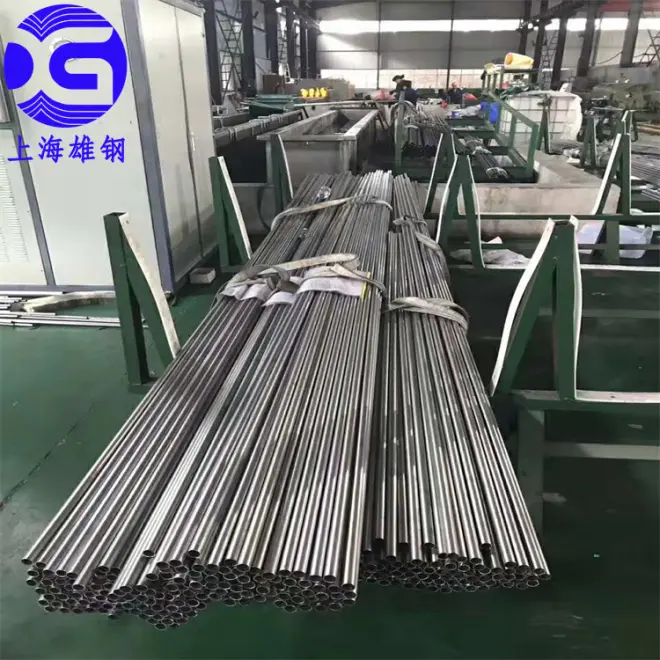