好书推荐《热处理手册》
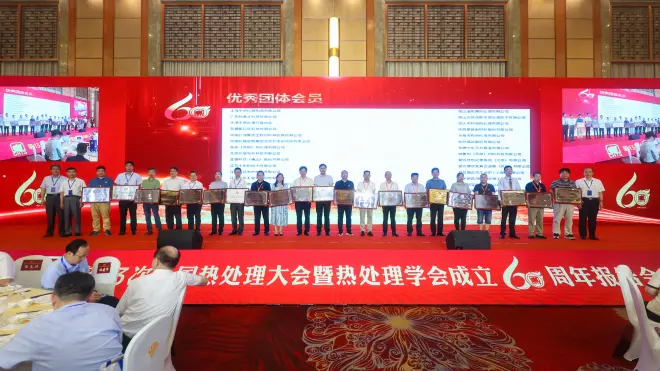
《热处理手册》是我国热处理领域最为权威的综合性工具书,笔者有幸参与了第5版《热处理手册》第2卷典型零件热处理的编撰工作。在编撰过程中,第2卷全体参编人员有感于当前热处理技术的迅速发展,对手册内容进行了大幅更新,第2卷更新比例可达50%。
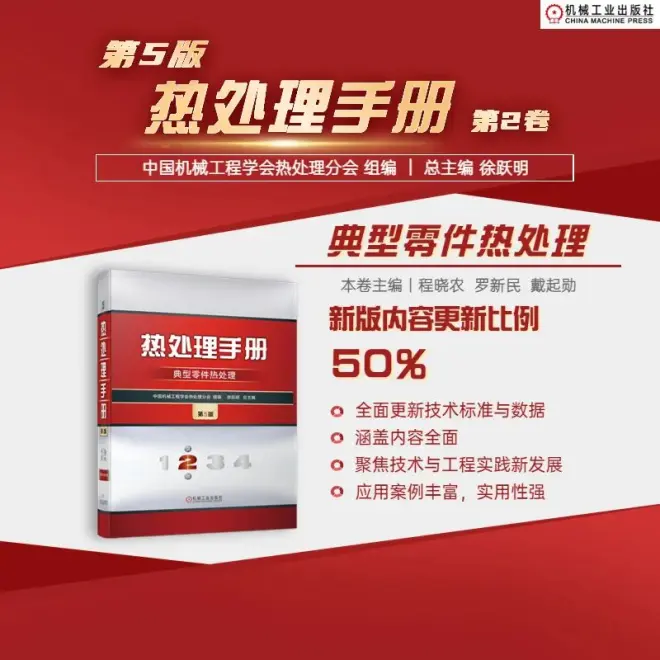
与第4版《热处理手册》相比,新版主要做了以下修订:
由第4版的19章修订为24章。“第1章零件热处理工艺性与设计原则”由第4版的第1章和第2章整合优化而成。将第4版第3卷和第4卷的相关内容进行整合,在第2卷中增加了“第2章热处理质量管理”“第3章热处理清洁生产与绿色工厂”两章。结合新兴行业发展,增加了典型零件热处理新技术、新材料和新工艺的内容,包括“第20章耐磨材料典型零件的热处理”“第22章航天零件的热处理”“第23章风电齿轮箱零件的热处理”和“第24章零件热处理典型缺陷和失效分析”等。其他章节除顺序略有变动外,还对一些内容进行了修订,并增加了相关内容,如在“第8章大型铸锻件的热处理”中增加了“大型转子锻件的热处理”和“大型筒体与封头锻件的热处理”,在“第10章模具的热处理”中增加了“典型模具热处理”,在“第21章航空零件的热处理”中增加了“飞机后机身承力框的热处理”“飞机梁的热处理”“三联齿的热处理”和“交流伺服电动机定子和转子的热处理”等内容。
其中,《大型铸锻件的热处理》一章反映了大锻件在锻后热处理和性能热处理高质量精密热处理工艺方面的重要进展,解决了大型锻件热处理工艺参数数据匮乏的重大难题。在编撰新版手册时,作者对旧版手册中原有内容进行了重大更新,新增了“大型筒体与封头锻件的热处理”工程应用实例。
全球气候危机向人类生存环境持续发出警告,减少二氧化碳排放的高效清洁绿色能源的开发与利用成为人类命运共同体息息相关的议题。随着核反应堆单堆容量的增加和反应堆用锻件向整锻化方向发展,核岛中压力容器、稳压器和蒸发器等合金钢锻件厚度不断增大、重量不断增加。受热处理淬火冷却条件的限制,大锻件淬火时心部甚至性能要求厚度处淬火冷速不足,可能导致出现不合格组织,限制了锻件性能向高质量方向的持续提高。
大型筒体与封头锻件的热处理结合大型锻件的生产特点,尤其是化工和核电行业,大型锻件总结了此类锻件生产质量控制要点和方法。对选材和工艺过程参数优化用全流程工艺曲线分析并结合锻后热处理和性能热处理的实际问题进行了详细介绍。
大型筒体与封头锻件锻后热处理的主要目的是消除锻造应力, 细化组织, 改善可加工性。在钢锭中氢含量较高的情况下, 需在锻后进行扩氢处理防止形成白点, 故大型筒体与封头锻件的锻后热处理工艺规范尤其重要;为了保证锻件心部达到规定温度, 完成奥氏体转变, 并实现均匀化, 通常在均温后需进一步保温, 保温时间须根据锻件的有效厚度确定。手册从数据支撑出发,克服了原有数据准确性低、完整性差、难提取共享等问题,介绍了大型筒体和封头锻件常用材料牌号及化学成分;一般化工容器和核电容器筒体、封头锻件用钢的力学性能要求;典型大型筒体与封头锻件锻后热处理及性能热处理工艺规范;图文并茂地介绍了大锻件锻后热处理和性能热处理的有效厚度计算方法。这些实用数据和方法对指导相关产品的热处理生产具有非常重要的指导意义。
适值《热处理手册》第5版面世之际,为让广大热处理专业人士先睹为快,现将《热处理手册》第2卷中关于“大型筒体与封头锻件的热处理”的内容摘录如下。
下面就让我们对书中内容先睹为快~
⬇⬇⬇
01精彩样张
8. 8 大型筒体与封头锻件热处理
8. 8. 1 大型筒体与封头的种类和技术要求
大型容器的壳体是由筒体和封头两大类锻件构成的一个密闭容器。大型容器在国民生活中普遍存在,主要应用于石油、 化工、 核电等领域。因此, 大型筒体与封头锻件一般分为化工容器用筒体和封头锻件、核电蒸汽发生器用筒体和封头锻件、 核电压力容器用筒体和封头锻件, 以及核电稳压器用筒体和封头锻件等。化工容器、 核电容器均在一定的压力、 温度和介质条件下长时间工作, 因此对于壳体材料, 除了要求有较高的常温力学性能, 根据其不同的使用工况, 还要求有一定的高 / 低温性能。表 8-39 列出了大型筒体和封头锻件的常用材料牌号及化学成分, 表 8-40 列出了一般化工容器和核电容器筒体、 封头锻件用钢的力学性能要求。
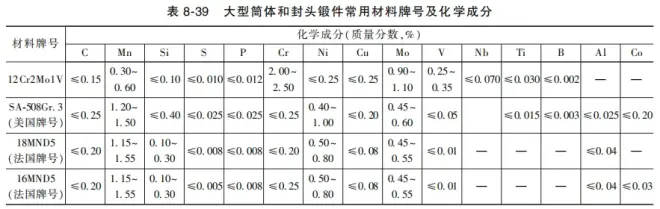
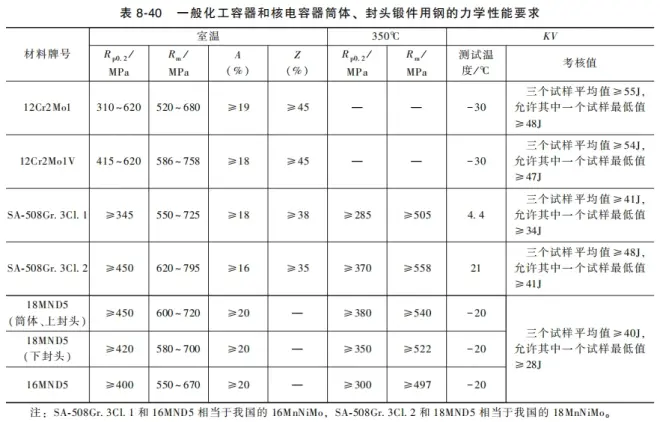
8. 8. 2 锻后热处理
大型筒体与封头锻件锻后热处理的主要目的是消除锻造应力, 细化组织, 改善可加工性。在钢锭中氢含量较高的情况下, 需在锻后进行扩氢处理防止形成白点。大型筒体与封头锻件锻后热处理工艺规范如图 8-65 所示。为了保证锻件心部达到规定温度, 完成奥氏体转变, 并实现均匀化, 通常在均温后需进一步保温, 保温时间根据锻件的有效厚度确定。典型大型筒体与封头锻件锻后热处理的有效厚度计算方法见表 8-41。
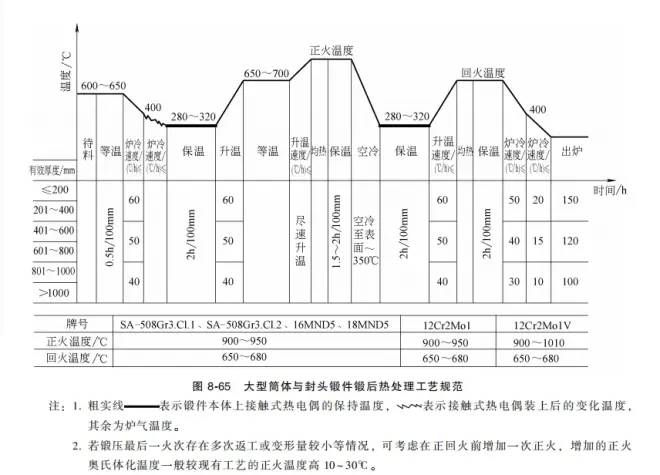
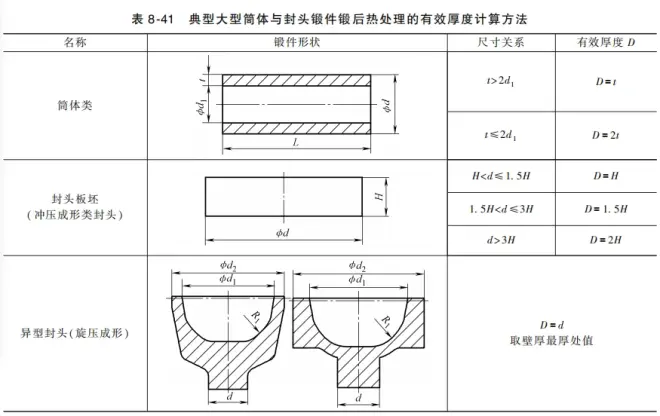
8. 8. 3 性能热处理
大型筒体和封头锻件的性能热处理一般采用调质处理, 其工艺规范如图 8-66 所示。性能热处理中的保温时间根据锻件的有效厚度确定, 典型大型筒体与封头锻件性能热处理的有效厚度计算方法见表 8-42。
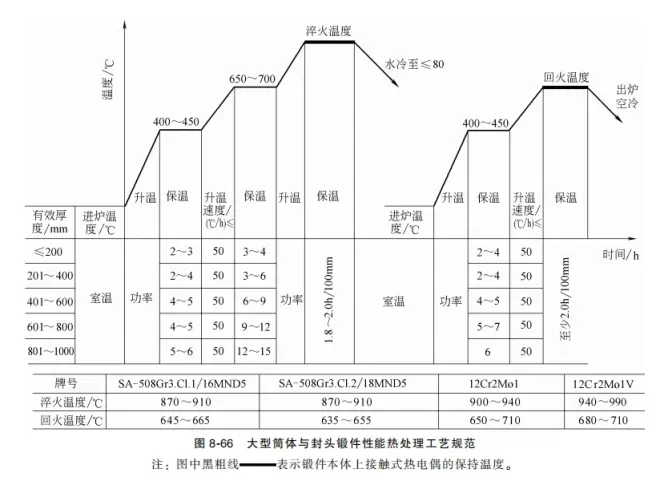
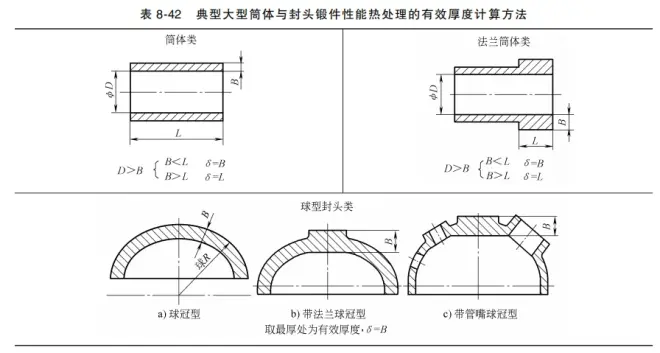
02目录
前言
第1章零件热处理工艺性与设计原则1
1.1零件热处理工艺性1
1.1.1零件热处理工艺性概述1
1.1.2钢的淬透性2
1.1.3钢的变形和开裂倾向5
1.1.4钢的回火脆性和白点敏感性6
1.1.5钢的回火稳定性和热稳定性8
1.1.6钢的其他热处理工艺性10
1.1.7铝合金的热处理工艺性11
1.1.8钛合金的热处理工艺性14
1.2零件材料的选择与热处理技术要求15
1.2.1零件热处理技术要求设计15
1.2.2选择材料的基本原则、思路及合理性17
1.3零件热处理的结构工艺性20
1.3.1改善零件热处理工艺性的结构设计20
1.3.2改善零件结构热处理工艺性的其他措施22
1.4零件加工工艺路线与工序安排28
1.4.1零件的工艺路线与毛坯选择28
1.4.2零件热处理工序安排29
1.5零件热处理工艺设计原则与要素32
1.5.1零件热处理工艺设计原则32
1.5.2零件热处理工艺设计要素34
1.5.3零件热处理工艺性审核36
参考文献38
第2章热处理质量管理39
2.1概论39
2.2热处理质量管理体系40
2.2.1质量策划40
2.2.2热处理工艺管理42
2.2.3人员管理42
2.2.4设备管理42
2.2.5物料管理43
2.2.6热处理工艺材料管理44
2.2.7热处理作业环境管理44
2.3热处理过程控制45
2.3.1待热处理零件的控制45
2.3.2防渗处理45
2.3.3热处理装料45
2.3.4热处理零件的清洗45
2.3.5热处理工艺过程控制45
2.3.6热处理典型工艺的管理46
2.4热处理质量检验48
参考文献49
第3章热处理清洁生产与绿色工厂50
3.1热处理环境技术要求51
3.1.1污染的分类和来源51
3.1.2污染物的控制与排放技术要求51
3.2清洁绿色热处理技术要求53
3.2.1基本要求53
3.2.2热处理厂房53
3.2.3设备54
3.2.4热处理工艺材料58
3.2.5热处理工艺58
3.3清洁绿色热处理工厂59
3.3.1绿色工厂59
3.3.2基本要求59
3.3.3绿色热处理企业要求59
参考文献63
第4章齿轮的热处理64
4.1齿轮受力状况及损坏特征64
4.1.1啮合齿面间的摩擦力及齿面磨损64
4.1.2啮合齿面的接触应力及接触疲劳64
4.1.3齿轮的弯曲应力及弯曲疲劳65
4.2齿轮的材料热处理质量控制与疲劳强度67
4.2.1铸铁齿轮的材料热处理质量控制与疲劳强度67
4.2.2调质齿轮的材料热处理质量控制与疲劳强度68
4.2.3表面淬火齿轮的材料热处理质量控制与疲劳强度70
4.2.4渗碳淬火锻钢齿轮的材料热处理质量控制与疲劳强度70
4.2.5渗氮齿轮的材料热处理质量控制与疲劳强度74
4.3齿轮材料76
4.3.1齿轮用钢76
4.3.2齿轮用铸铁78
4.3.3齿轮用铜合金84
4.4齿轮的热处理工艺87
4.4.1齿轮的调质87
4.4.2齿轮的表面淬火91
4.4.3齿轮的渗碳和碳氮共渗107
4.4.4齿轮的渗氮128
参考文献143
第5章滚动轴承零件的热处理144
5.1滚动轴承的工作条件及对用钢的基本性能要求144
5.2滚动轴承常用钢(合金)及其应用范围145
5.3一般用途滚动轴承零件的热处理149
5.3.1高碳铬钢轴承零件马氏体淬火150
5.3.2高碳铬钢轴承零件贝氏体等温淬火和马氏体分级淬火166
5.3.3高碳铬钢轴承零件在各种设备中的热处理工艺167
5.3.4高碳铬钢轴承零件的感应热处理167
5.3.5高碳铬钢轴承零件预渗氮和碳氮共渗表面改性热处理172
5.3.6轴承零件的真空热处理174
5.3.7轴承零件表面的激光淬火176
5.3.8渗碳钢制中小型轴承零件的热处理179
5.3.9中碳合金钢轴承零件的热处理180
5.4特大、特轻、微型、精密等轴承零件的热处理182
5.4.1特大及重大型轴承零件的热处理182
5.4.2特轻轴承零件的热处理184
5.4.3微型轴承零件的热处理184
5.4.4高碳铬钢精密轴承零件的热处理186
5.4.5铁路车辆轴箱轴承零件的热处理187
5.4.6汽车轴承零件的热处理190
5.5特殊用途轴承零件的热处理193
5.5.1耐蚀轴承零件的热处理193
5.5.2含氮不锈轴承钢及其热处理197
5.5.3高温轴承零件的热处理199
5.5.4防磁轴承零件的热处理208
5.6其他轴承零件的热处理211
5.6.1保持架、铆钉等轴承零件的热处理211
5.6.2冲压滚针轴承零件的热处理213
参考文献218
第6章弹簧的热处理219
6.1弹簧的分类、服役条件、失效形式和性能要求219
6.1.1弹簧的分类219
6.1.2弹簧的服役条件和失效形式220
6.1.3弹簧产品的性能要求222
6.2弹簧材料及其热处理223
6.2.1弹簧常用原材料供货状态及其热处理224
6.2.2特殊用途的弹簧材料及其热处理232
6.3典型弹簧制造过程中的热处理235
6.3.1乘用车和商用车悬架弹簧的热处理235
6.3.2乘用车和商用车稳定杆的热处理237
6.3.3车用悬架扭杆弹簧的热处理239
6.3.4车用驻动器弹簧的热处理240
6.3.5汽车用内燃机发动机气门弹簧的热处理240
6.3.6汽车用自动变速器弹簧的热处理241
6.3.7汽车用离合器螺旋弹簧和膜片弹簧的热处理242
6.3.8汽车行李舱扭杆弹簧的热处理243
6.3.9轮轨列车转向架弹簧的热处理243
6.3.10轮轨列车驻动制动器弹簧的热处理244
6.3.11轮轨列车铁路地基隔振弹簧的热处理245
6.3.12工程机械大弹簧的热处理245
6.3.13碟簧的热处理246
6.3.14弹性挡圈(卡簧)的热处理247
6.3.15平面涡卷弹簧的热处理247
6.4弹簧的特殊热处理248
6.4.1弹簧的渗氮248
6.4.2弹簧的盐浴热处理249
6.4.3弹簧的喷丸强化处理249
6.4.4弹簧的加温加载(强压)处理249
参考文献250
第7章紧固件的热处理251
7.1螺纹紧固件的热处理251
7.1.1通用螺纹紧固件的热处理251
7.1.2专用螺纹紧固件的热处理263
7.2垫圈、挡圈、销和铆钉的热处理272
7.2.1垫圈和挡圈的热处理272
7.2.2销的热处理273
7.2.3铆钉的热处理273
7.3质量检验和控制274
7.3.1脱碳与增碳274
7.3.2淬火控制275
7.3.3回火控制276
7.3.4再回火试验277
7.3.5氢脆的检查和控制277
参考文献277
第8章大型铸锻件的热处理278
8.1大型锻件的锻后热处理278
8.1.1大型锻件中的白点与氢脆278
8.1.2大型锻件的扩氢计算279
8.1.3大型锻件的晶粒细化问题281
8.1.4锻后热处理工艺的制订原则与工艺参数281
8.1.5大型锻件锻后热处理的基本工艺类型与典型工艺曲线282
8.2大型锻件的最终热处理287
8.2.1大型锻件淬火、正火时的加热287
8.2.2大型锻件淬火、正火时的冷却290
8.2.3大型锻件的回火296
8.2.4大型锻件最终热处理工艺300
8.2.5大型锻件热处理后的力学性能300
8.3大型锻件的化学热处理305
8.3.1大型重载齿轮的深层渗碳305
8.3.2大型锻件的渗氮处理306
8.4热轧锻钢工作辊的热处理306
8.4.1热轧工作辊的种类、材质及技术要求306
8.4.2锻后热处理(正火+回火)307
8.4.3调质307
8.5冷轧锻钢工作辊的热处理308
8.5.1冷轧工作辊的种类和技术要求308
8.5.2冷轧工作辊用钢308
8.5.3冷轧工作辊制造工艺路线309
8.5.4锻后热处理309
8.5.5调质309
8.5.6淬火与回火310
8.6锻钢支承辊的热处理315
8.6.1支承辊的种类和技术要求315
8.6.2支承辊用钢315
8.6.3锻后热处理316
8.6.4预备热处理316
8.6.5最终热处理317
8.7大型转子锻件的热处理318
8.7.1大型转子锻件的种类和技术要求318
8.7.2大型转子锻件用钢320
8.7.3发电机转子与汽轮机低压转子热处理320
8.7.4汽轮机高、中压转子锻件热处理321
8.8大型筒体与封头锻件热处理323
8.8.1大型筒体与封头的种类和技术要求323
8.8.2锻后热处理323
8.8.3性能热处理324
8.9大型锻件的其他热处理工艺325
8.9.1锻件切削加工后的去应力退火325
8.9.2锻件矫直加热与回火工艺326
8.9.3电渣焊焊接件的热处理工艺326
8.10大型铸件的热处理327
8.10.1大型铸件热处理的种类与目的327
8.10.2重型机械类铸件热处理实例327
参考文献332
第9章工具的热处理334
9.1工具的服役条件及工具用钢334
9.1.1工具的服役条件334
9.1.2工具的失效方式334
9.1.3工具用钢334
9.1.4工具用钢的质量要求339
9.2工具钢的热处理工艺340
9.2.1碳素工具钢与合金工具钢的热处理工艺340
9.2.2高速工具钢的热处理工艺344
9.3工具钢热处理后的金相组织357
9.3.1碳素工具钢与合金工具钢热处理后的金相组织357
9.3.2高速工具钢热处理后的金相组织360
9.4影响高速工具钢工具使用寿命的因素364
9.4.1材料的影响364
9.4.2热处理的影响365
9.4.3力学性能的影响366
9.4.4显微组织的影响367
9.4.5表面状态的影响367
9.5典型工具的热处理368
9.5.1锉刀的热处理368
9.5.2手用锯条的热处理368
9.5.3手用丝锥的热处理369
9.5.4圆板牙的热处理369
9.5.5手用铰刀的热处理370
9.5.6搓丝板的热处理370
9.5.7滚丝轮的热处理372
9.5.8机用丝锥的热处理372
9.5.9麻花钻的热处理374
9.5.10车刀的热处理376
9.5.11拉刀的热处理376
9.5.12齿轮刀具的热处理378
9.5.13小型高速工具钢刀具的热处理379
9.5.14高速工具钢对焊刀具的热处理381
9.5.15常用五金和木工工具的热处理381
参考文献383
第10章模具的热处理384
10.1模具材料的分类384
10.2冷作模具的热处理386
10.2.1冷作模具的工作条件和要求386
10.2.2冷作模具的主要失效形式387
10.2.3冷作模具材料的选用387
10.2.4冷作模具的热处理工艺390
10.3热作模具的热处理395
10.3.1热作模具的工作条件和要求395
10.3.2热作模具的主要失效形式395
10.3.3热作模具材料的选用395
10.3.4热作模具的热处理工艺396
10.4塑料模具的热处理407
10.4.1塑料模具的工作条件和分类407
10.4.2塑料模具的主要失效形式407
10.4.3塑料模具材料的选用407
10.4.4塑料模具钢的热处理工艺408
10.5模具强韧化热处理411
10.5.1模具强韧化处理工艺411
10.5.2模具真空热处理工艺412
10.5.3模具表面强化技术及其应用416
10.6典型模具热处理424
参考文献439
第11章量具热处理441
11.1量具用材料441
11.1.1对量具用材料的要求441
11.1.2量具常用钢种及质量要求441
11.2钢制量具热处理工艺443
11.2.1量具制造工艺路线简介443
11.2.2预备热处理(或第一次热处理)443
11.2.3最终热处理(或第二次热处理)444
11.2.4量具热处理的技术要求445
11.2.5量块及高尺寸稳定性量规的热处理特点446
11.2.6热处理后机械加工(磨削)对量具的影响447
11.2.7表面涂层447
11.3典型量具热处理447
11.3.1百分表零件的热处理447
11.3.2游标卡尺零件的热处理448
11.3.3千分尺零件的热处理449
11.3.4螺纹环规和塞规的热处理450
参考文献451
第12章汽车、拖拉机及柴油机零件的热处理452
12.1活塞环的热处理452
12.1.1活塞环的服役条件和失效形式452
12.1.2活塞环的材料452
12.1.3活塞环的热处理工艺454
12.1.4活塞环的表面处理456
12.1.5活塞环的质量检验456
12.2活塞销的热处理458
12.2.1活塞销的服役条件和失效形式458
12.2.2活塞销材料458
12.2.3活塞销的热处理工艺459
12.2.4活塞销的质量检验461
12.2.5活塞销的常见热处理缺陷及预防补救措施461
12.3连杆的热处理462
12.3.1连杆的服役条件和失效形式462
12.3.2连杆材料462
12.3.3连杆的热处理工艺463
12.3.4连杆的质量检验466
12.3.5连杆的常见热处理缺陷及预防补救措施468
12.4曲轴的热处理469
12.4.1曲轴的服役条件和失效形式469
12.4.2曲轴材料469
12.4.3曲轴的热处理工艺469
12.4.4曲轴的质量检验475
12.4.5曲轴的常见热处理缺陷及预防补救措施475
12.5凸轮轴的热处理475
12.5.1凸轮轴的服役条件和失效形式475
12.5.2凸轮轴材料476
12.5.3凸轮轴的热处理工艺477
12.5.4凸轮轴的质量检验480
12.5.5凸轮轴的常见热处理缺陷及预防补救措施480
12.6挺杆的热处理480
12.6.1挺杆的服役条件和失效形式480
12.6.2挺杆材料481
12.6.3挺杆的热处理工艺482
12.6.4挺杆的质量检验485
12.6.5挺杆的常见热处理缺陷及预防补救措施485
12.7排气门的热处理486
12.7.1排气门的服役条件和失效形式486
12.7.2排气门材料487
12.7.3排气门的热处理工艺487
12.7.4排气门的质量检验495
12.7.5排气门的常见热处理缺陷及预防补救措施495
12.8半轴的热处理495
12.8.1半轴的服役条件和失效形式495
12.8.2半轴材料495
12.8.3半轴的热处理工艺496
12.8.4半轴的质量检验501
12.8.5半轴的常见热处理缺陷及预防补救措施501
12.9喷油泵柱塞偶件和喷油嘴偶件的热处理502
12.9.1喷油泵和喷油嘴偶件的服役条件和失效形式502
12.9.2喷油泵和喷油嘴材料502
12.9.3喷油泵和喷油嘴偶件的热处理工艺503
12.10履带板的热处理507
12.10.1履带板的服役条件和失效形式507
12.10.2履带板材料507
12.10.3履带板的热处理工艺508
12.10.4履带板的质量检验509
参考文献509
第13章金属切削机床零件的热处理510
13.1机床导轨的热处理510
13.1.1导轨的服役条件及失效形式510
13.1.2导轨材料510
13.1.3铸铁导轨的感应淬火511
13.1.4铸铁导轨的火焰淬火515
13.1.5铸铁导轨的接触电阻加热淬火517
13.1.6镶钢导轨热处理519
13.1.7机床导轨用材和热处理的进展519
13.2机床主轴的热处理521
13.2.1主轴的服役条件及失效形式521
13.2.2主轴材料521
13.2.3主轴的热处理工艺522
13.2.4机床主轴用材及热处理的进展526
13.3机床丝杠的热处理527
13.3.1丝杠的服役条件及失效形式527
13.3.2丝杠材料527
13.3.3梯形螺纹丝杠的热处理528
13.3.4滚珠丝杠的热处理531
13.3.5丝杠的特殊热处理工艺533
13.4机床基础件的去应力处理534
13.4.1机床基础件的服役条件及失效形式534
13.4.2自然时效534
13.4.3热时效534
13.4.4振动时效535
13.5机床其他零件的热处理536
13.5.1机床附件的热处理536
13.5.2机床离合器零件的热处理537
13.5.3弹簧夹头的热处理539
13.5.4蜗杆的热处理540
13.5.5花键轴的热处理542
13.5.6刀杆的热处理542
13.5.7分度齿轮的热处理544
13.5.8转盘的热处理544
参考文献545
第14章气动凿岩工具及钻探机械零件的热处理546
14.1凿岩机活塞的热处理546
14.1.1工作条件及失效形式546
14.1.2凿岩机活塞用材料546
14.1.320CrMnMo钢活塞的热处理546
14.1.435CrMoV钢活塞的热处理548
14.2冲击器活塞的热处理548
14.2.1工作条件及失效形式548
14.2.2技术条件和使用材料549
14.2.3制造工艺路线549
14.2.420Ni4Mo钢高风压活塞的热处理549
14.2.5技术要求及质量检验550
14.3凿岩机主要渗碳件的热处理551
14.3.1工作条件及失效形式551
14.3.2技术条件和使用材料552
14.3.3制造工艺路线552
14.3.4热处理工艺552
14.3.5渗碳件热处理的质量检验552
14.3.6热处理常见缺陷及防止方法552
14.4凿岩机钎头的热处理554
14.4.1工作条件及失效形式554
14.4.2技术条件和使用材料555
14.4.3制造工艺路线556
14.4.4热处理工艺556
14.5凿岩机钎尾及成品钎杆的热处理559
14.5.1工作条件及失效形式559
14.5.2技术条件和使用材料560
14.5.3制造工艺路线560
14.5.4热处理工艺561
14.5.5技术要求和质量检验563
14.6连接套的热处理563
14.6.1工作条件及失效形式563
14.6.2技术条件和使用材料563
14.6.320MnVB钢连接套的热处理564
14.7其他气动工具零件的热处理564
14.8牙轮钻机钻头的热处理566
14.8.1工作条件及失效形式566
14.8.2技术条件和使用材料566
14.8.3制造工艺路线566
14.8.4热处理工艺566
14.8.5质量检验567
14.9钻探机械钻具的热处理568
14.9.1工作条件及失效形式568
14.9.2技术条件和使用材料568
14.9.3制造工艺路线568
14.9.4热处理工艺568
14.9.5热处理质量检验570
14.9.6热处理缺陷及防止方法570
参考文献571
第15章农机具零件的热处理572
15.1农机具零件的服役条件、失效形式和性能要求572
15.1.1农机具零件的磨损失效572
15.1.2农机具耐磨零件的力学性能要求574
15.1.3农机具耐磨零件的组织要求579
15.1.4农机具零件的特殊性能要求582
15.2耕整机械典型零件的热处理585
15.2.1犁铧的热处理585
15.2.2犁壁的热处理588
15.2.3圆盘的热处理590
15.2.4锄铲的热处理592
15.2.5旋耕刀的热处理595
15.3收获与采集机械典型刀片的热处理597
15.3.1剪毛机刀片的热处理597
15.3.2往复式收割机刀片的热处理599
15.3.3秸秆和根茬粉碎还田机刀片的热处理600
15.3.4铡草和青饲料切碎刀片的热处理603
15.4农产品加工机械典型零件的热处理604
15.4.1脱粒机弓齿、钉齿与切草刀的热处理604
15.4.2粉碎机锤片的热处理605
15.4.3筛板的热处理607
15.4.4颗粒饲料压制机环模与压辊的热处理608
15.4.5轧棉花机、剥绒机锯片和肋条的热处理611
15.4.6榨油机榨螺的热处理613
15.4.7搅龙伸缩齿的热处理614
15.4.8搅龙叶片的热处理614
15.4.9链轮的热处理615
15.4.10输送风机叶片的热处理615
15.5拖拉机用牵引杆和拨叉的热处理615
15.5.1牵引杆的热处理615
15.5.2拨叉的热处理616
15.6小农具材料及其热处理616
15.7预防热处理缺陷的措施617
15.7.1空气炉加热防氧化脱碳617
15.7.2预防回火脆性618
15.7.3预防淬火开裂620
15.7.4热管冷却技术在提高淬火质量和节能、节水上的应用620
参考文献620
第16章发电设备零件的热处理622
16.1汽轮机转子和发电机转子的热处理622
16.1.1服役条件及失效形式622
16.1.2转子用钢622
16.1.3转子锻件的热处理629
16.1.4常见大型转子锻件热处理缺陷及预防措施633
16.2汽轮发电机无磁性护环的热处理633
16.2.1服役条件及失效形式633
16.2.2护环用钢633
16.2.3护环锻件的热处理634
16.2.4护环锻件常见热处理缺陷及预防措施635
16.3汽轮机叶轮的热处理635
16.3.1服役条件及失效形式635
16.3.2叶轮用钢635
16.3.3叶轮锻件的热处理636
16.3.4叶轮锻件热处理常见缺陷及预防措施638
16.4汽轮机叶片的热处理638
16.4.1服役条件及失效形式638
16.4.2叶片用钢639
16.4.3叶片毛坯的热处理644
16.4.4叶片的特种热处理646
16.5汽轮机螺栓的热处理646
16.5.1服役条件及失效形式646
16.5.2螺栓用钢647
16.5.3螺栓毛坯的热处理648
16.5.4螺栓热处理常见缺陷及预防措施649
16.6锅炉构件及输汽管的热处理649
16.6.1锅炉用钢管及钢板的服役条件和零件失效形式649
16.6.2锅炉钢管及钢板用钢649
16.6.3锅炉构件的热处理652
参考文献653
第17章石油化工机械零件的热处理655
17.1泥浆泵零件的热处理655
17.1.1液缸的热处理655
17.1.2缸套的热处理656
17.1.3阀体与阀座的热处理658
17.1.4活塞杆的热处理660
17.1.5小齿轮轴的热处理660
17.2钻机绞车零件的热处理661
17.2.1制动鼓的热处理661
17.2.2链条的热处理662
17.2.3链轮的热处理665
17.3钻探工具的热处理666
17.3.1吊环的热处理666
17.3.2吊卡的热处理667
17.3.3钻杆接头的热处理668
17.3.4抽油杆的热处理669
17.3.5公母锥的热处理670
17.3.6抽油泵泵筒的热处理672
17.3.7石油钻头的热处理672
17.4钻机齿轮的热处理675
17.4.1弧齿锥齿轮的热处理675
17.4.2转盘齿轮的热处理676
17.5化工机械零件的热处理677
17.5.1压力容器的热处理677
17.5.2典型容器的热处理682
17.5.3压缩机阀片的热处理683
17.5.4低温压缩机壳体的热处理684
17.5.5天然气压缩机活塞杆的热处理685
参考文献687
第18章液压元件的零件热处理688
18.1概述688
18.2齿轮泵零件的热处理 688
18.2.1齿轮的热处理688
18.2.2齿轮泵轴的热处理688
18.2.3泵体的热处理688
18.3叶片泵零件的热处理690
18.3.1转子的热处理690
18.3.2定子的热处理692
18.3.3叶片泵轴的热处理693
18.3.4叶片的热处理693
18.3.5配油盘的热处理693
18.4柱塞泵零件的热处理693
18.5转向助力泵零件的热处理696
18.6液压阀零件的热处理699
18.6.1滑阀的热处理699
18.6.2阀座的热处理699
18.6.3提动阀和提动阀座的热处理 699
18.7液压元件零件热处理的质量检验701
参考文献701
第19章纺织机械零件的热处理702
19.1纺织机械主机零件的热处理702
19.1.1锭杆的热处理702
19.1.2罗拉的热处理704
19.1.3钢领的热处理707
19.1.4专用轴承的热处理708
19.1.5钳板轴的热处理709
19.1.6化纤机械零件的热处理709
19.2纺织器材零件的热处理710
19.2.1针布的热处理710
19.2.2三角的热处理711
19.2.3针筒的热处理711
19.3热处理质量检验与控制711
19.4常见热处理缺陷及防止方法712
参考文献713
第20章耐磨材料典型零件的热处理714
20.1挖掘机斗齿的热处理714
20.1.1斗齿的服役条件及失效形式714
20.1.2斗齿材料714
20.1.3斗齿的热处理工艺716
20.2破碎机锤头的热处理719
20.2.1锤头的服役条件及失效形式719
20.2.2锤头材料719
20.2.3锤头的热处理工艺721
20.3破碎机衬板的热处理725
20.3.1衬板的服役条件及失效形式725
20.3.2衬板材料726
20.3.3衬板的热处理工艺727
20.4磨球的热处理730
20.4.1磨球的服役条件及失效形式730
20.4.2磨球材料730
20.4.3磨球的热处理工艺732
20.5磨机衬板的热处理734
20.5.1衬板的服役条件及失效形式734
20.5.2衬板材料734
20.5.3衬板的热处理工艺736
20.6铁路辙叉的热处理738
20.6.1辙叉的服役条件及失效形式738
20.6.2辙叉材料738
20.6.3辙叉的热处理工艺739
参考文献741
第21章航空零件的热处理743
21.1航空零件材料和热处理特点743
21.2飞机起落架外筒的热处理743
21.3飞机后机身承力框的热处理746
21.4飞机梁的热处理747
21.5飞机蒙皮的热处理749
21.6压气机叶片的热处理750
21.7涡轮叶片的热处理752
21.8涡轮盘的热处理756
21.9涡轮轴的热处理759
21.10燃烧室的热处理761
21.11航空齿轮的热处理762
21.12三联齿的热处理766
21.13交流伺服电动机定子和转子的
热处理768
参考文献769
第22章航天零件的热处理770
22.1航天零件材料及热处理特点770
22.2运载火箭领域典型零件的热处理771
22.2.1大型薄壁壳体类零件的热处理771
22.2.2支座类零件的热处理772
22.2.3阀门类零件的热处理773
22.2.4杆类零件的热处理774
22.2.5耐磨零件的化学热处理775
22.3空间飞行器领域典型零件的热处理776
22.3.1框类零件的热处理776
22.3.2桁条类零件的热处理777
22.3.3薄壁支架类零件的热处理779
22.3.4接头类零件的热处理780
22.3.5开关臂类零件的热处理780
22.3.6框架类零件的热处理781
22.3.7导电滑环典型零件的热处理781
22.3.8耐磨零件的化学热处理783
参考文献784
第23章风电齿轮箱零件的热处理785
23.1风电齿轮箱简介785
23.2风电齿轮的失效分析786
23.3风电齿轮箱零件用材料及其热处理788
23.3.1风电齿轮箱零件用钢及其热处理788
23.3.2风电齿轮箱零件用铸钢及其热处理795
23.3.3风电齿轮箱零件用铸铁及其热处理797
23.4风电齿轮的热处理工艺804
23.4.1风电齿轮的调质804
23.4.2风电齿轮的渗碳淬火807
23.4.3风电齿轮的清理抛丸与强化喷丸813
23.4.4风电齿轮的渗氮816
23.4.5风电齿轮的感应淬火819
参考文献822
第24章零件热处理典型缺陷和失效分析824
24.1概论824
24.1.1热处理缺陷824
24.1.2热处理件失效826
24.1.3热处理全面质量控制827
24.2热处理缺陷分析828
24.2.1热处理裂纹828
24.2.2热处理变形830
24.2.3热处理残余应力832
24.2.4热处理组织不良834
24.2.5力学性能不合格835
24.2.6脆性836
24.3热处理件失效分析838
24.3.1变形失效838
24.3.2韧性断裂839
24.3.3解理和准解理脆性断裂839
24.3.4沿晶脆性断裂841
24.3.5疲劳断裂842
24.3.6应力腐蚀断裂845
24.3.7腐蚀失效846
24.3.8磨损失效846
参考文献848
978-7-111-72974-7
热处理手册 第2卷 典型零件热处理 第5版
03简介

04折扣链接以上图文来自机械工业出版社出版的《热处理手册 第2卷 典型零件热处理 第5版》,更多精彩内容您可扫描下方二维码购买本书阅读学习。
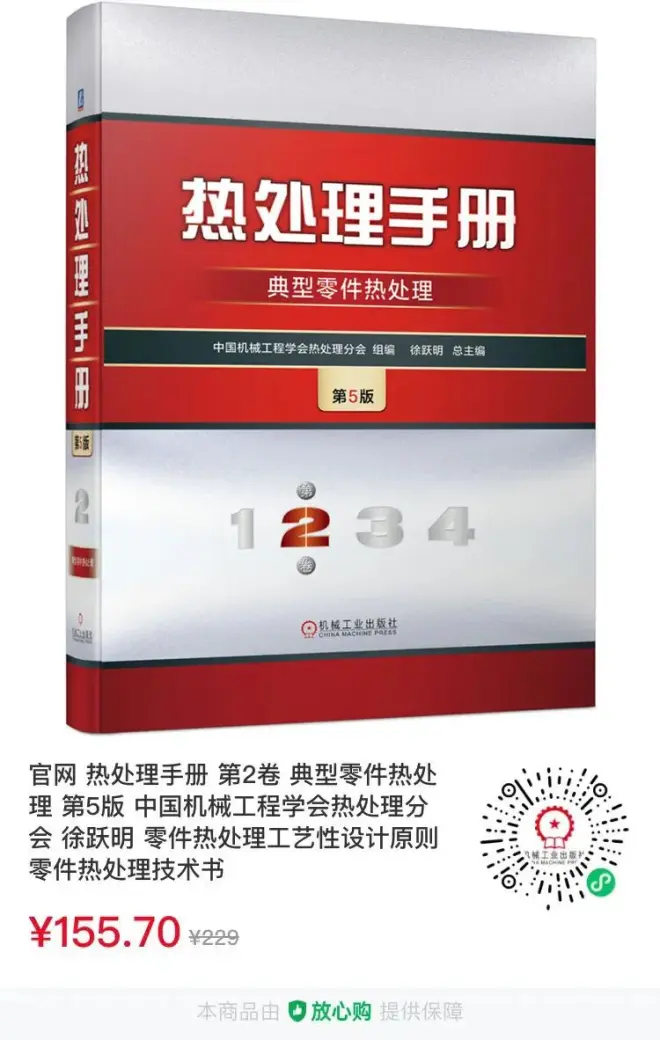