常见的复合材料成型工艺概括
复合材料是指由两种或两种以上不同物理特性或不同化学物质通过复合,组成多相、三维结合且各相之间有明显界面的、具有特殊性能的材料;其主要是由增强材料和基体材料组成。它最大的特点是复合后材料的性能优于构成该复合材料的单一材料性能。
根据基体材料的不同可以将复合材料划分为:树脂基增强复合材料、金属基复合材料和陶瓷基复合材料。其中,树脂基复合材料的使用量最大,占所有复合材料使用量的90%以上。
树脂基复合材料具有在设计与制造上自由设计性、材料与结构一致性且产品形状的设计自由性。树脂基复合材料的成型工艺可以分为三大类:
(1)对模成型:
模压成型、树脂传递成型、注射成型、冷压成型、结构反应注射成型;
(2)接触成型:
手糊成型、喷射成型、真空袋成型、压力袋成型、高压釜成型;
(3)其他重要成型方法:
纤维缠绕成型法、拉挤成型法、连续板材成型法、离心铸型法;
不同的生产工艺,适应不同的制品和生产规模,除手糊、喷射、缠绕三种工艺为开模成型外,其余均为闭模成型工艺。下面对普遍使用几种复合材料成型及应用进行概括。
1. 手糊成型工艺
手糊成型工艺是指通过手工把增强材料和树脂相互交错的在模具上铺层,黏结然后固化成型的工艺。
手糊成型工艺所需原材料包括:增强材料(玻璃纤维粗纱、玻璃纤维织物、粗纱织物、玻璃纤维毡等)、树脂(环氧树脂、聚酯树脂、酚醛树脂等)和辅助材料(催化剂、脱模剂、填料等)。
手糊成型生产设备与技术简单但效率低下,尺寸形状不受限制但稳定性差,主要用于生产汽车车壳、机器盖、保险杠等方面。
2. 喷射成型工艺
喷射成型工艺是将混有引发剂的树脂体系或含有促进的树脂体系分别从不同的树脂罐中吸入并在喷射枪中混合或喷出后混合,且喷枪上的切割器将连续纤维切成短纤维与树脂混合,再喷到模具上,待喷涂到规定的厚后,用辊筒压实再固化成型的一种方法。
喷射成型常用的树脂是30~40min贮存期的固化树脂,常用增强材料为玻璃纤维。喷射成型效率较手糊法提高2~4倍、生产投资少但光洁度差、工作环境恶劣,主要生产汽车车体、内饰件等。
3. 树脂传递模塑成型(RTM)工艺
树脂传递模塑过程是指将树脂注入到闭合模具中浸润增强材料并固化成型的工艺方法,是近年来发展较为迅速的适宜多品种、中批量、高质量的先进复合材料成型工艺,它是一种最接近产品形状部件的生产方法。
RTM工艺的高性能树脂有:乙烯基酯树脂、环氧树脂、双马来酰亚胺树脂(BMI)和热塑性树脂。增强材料有玻璃纤维、碳纤维、碳化硅纤维和芳纶纤维等。
树脂传递成型工艺可满足精确、大尺寸、外形复杂的模型要求但模具造价高、设计复杂。主要用车生产汽车车身板、保险杠、齿轮箱壳体、小卡车车厢等。
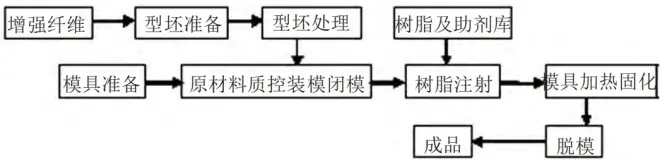
树脂传递模塑成型工艺流程
4. 模压成型工艺
模压成型是将一定量的预混料和浸润料加入金属对模内,经加热、加压固化成型的方法。模压料的品种有很多,可以是浸润物料,预混物料,也可以是坯料。
当前所用的模压料的品种有热固性复合材料包括:SMC (片状模塑料)、BMC (块状模压料)、TMC(厚片状模塑料)等品种;热塑性复合材料有 GMT(玻璃纤维毡热塑性塑料)、LFT-D(长纤维增强热塑性复合材料直接在线生产工艺制品)、LFT-G(长纤维热塑性颗粒注射制品)等。
模压成型的高性能树脂有:环氧树脂、酚醛树脂、有机硅树脂、烯丙基酯树脂等。增强材料主要有玻璃纤维束、玻璃纤维布、玻璃纤维毡等,也有少量特种制品选用碳纤维、有机纤维等品种,有时也采用两种或两种以上纤维混杂料作增强材料。
模压成型生产效率高、产品尺寸稳定、耐冲击、防碰撞、可批量生产但设备投资大、模具制造复杂。主要用于生产汽车车门、仪表盘、前端框架、汽车内板等。
BMC、TMC与SMC生产工艺流程相近,图为SMC生产工艺流程图:
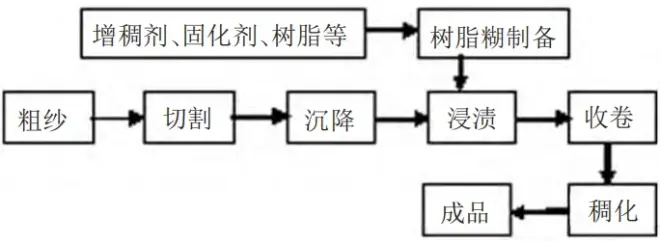
由于受到汽车回收方便和和相关环保法规的要求,目前热固性塑料用量正在下降,而热塑性复合材料随着其工艺的发展较为迅速,成本逐渐降低,其用量正逐步扩大,在汽车轻量化设计中,越来越多的零部件将考虑使用热塑性复合材料。
特别是热塑性复合材料的三种成型工艺中,相较于GMT和LFT-G这两种依赖于半成品板材或粒料的生产工艺,LFT-D技术则是直接利用聚合物母粒和玻璃纤维进行日常生产,省去了制板或造粒的中间过程,降低成本的同时使得制品在原料的选择上更为便捷实用,所以越来越多的汽车零部件厂商引进LFT-D生产技术。
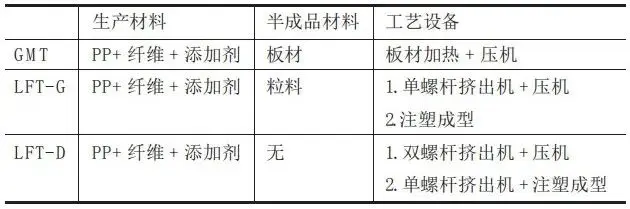
GMT、LFT-G和LFT-D生产方式比较
本文来源:北京航空航天大学机械工程及其自动化学院
版权声明:复材云集尊重版权并感谢每一位作者的辛苦付出与创作;除无法溯源的文章,我们均在文末备注了来源;如文章视频、图片、文字涉及版权问题,请第一时间联系我们,我们将根据您提供的证明材料确认版权并按国家标准支付稿酬或立即删除内容!