不懂精益生产的企业,效益很难做好!
文中所用工具⬇️
轻流(免费试用入口见评论区)
精益生产的核心,就是更少的投入,更多的产出。
精益生产的目标,是彻底消除无效劳动和浪费,最大限度地为企业谋取经济效益。
小批量生产比大批量生产成本更低,这就是精益生产的核心观点之一,听起来很反直觉。
从第一次工业革命,福特创立第一条汽车生产流水线以来,批量生产一直是现代工业的本质特征,和降低成本的关键所在。
但偏偏有企业把这套反直觉的逻辑给跑通了,它就是上世纪八九十年代的丰田公司。
有多厉害呢?通过推广丰田汽车的精益生产哲学,日本的汽车工业超过了美国,产量达到了1300万辆,占世界汽车总量的30%以上。
除了汽车,精益哲学在日本电子、计算机、飞机等制造工业也遍地开花,日本制造在二战后的废土中一飞冲天。
日本人工业的成功引起了美国人的浓厚兴趣。
1985年,国际汽车计划(IMVP)耗巨资500万美元,对全世界17个国家的汽车制造厂调查、对比分析。
最终认为日本丰田汽车公司的生产方式是最适用于现代制造企业的一种生产组织管理方式,并命名为“精益生产”。
精益生产和批量生产的根本区别?
精益生产和批量生产的根本区别,在于对企业经营目标无止境的尽善尽美的追求。
打个比方,武林里修炼力量的功夫秘籍有很多。
但同样是击破一扇门,追求寸劲巧劲的一阳指相比以力破力的金刚拳,原理更复杂。
精益生产方式的起点在用户的真实需求,把用户看成是生产制造过程的组成部分
宁可零库存,也不超前超量生产,以此达到低成本、无废品、零库存和产品多样化。
这就对企业精准调控和管理提出了更高的要求。
2023年,公司为什么还要推行精益生产方式?
为了提高劳动效率,彻底消除无效劳动和浪费,取得最大的经济效益,提高企业的竞争力。
精益生产最难的点在哪?
最难的是在管理层思想观念上的转变。
精益生产的十大工具与步骤
1.十大工具
01
准时化生产(JIT)
准时生产方式是起源于日本,其基本思想是“只在需要的时候,按需要的量生产所需的产品”。这种生产方式的核心是追求一种无库存的生产系统,或使库存达到最小的生产系统。我们在生产作业时要严格按照标准要求作业,按需求生产,现场需要多少就送多少材料,防止库存异常。
02
5S与目视化管理
5S(整理、整顿、清扫、清洁、素养)是现场目视化管理的有效工具,同时也是员工素养提升的有效工具。5S成功的关键是标准化,通过细化的现场标准和明晰的责任,让员工首先做到维持现场的整洁,同时暴露从而解决现场和设备的问题,进而逐渐养成规范规矩的职业习惯和良好的职业素养。
03
看板管理(Kanban)
看板是可以作为交流厂内生产管理信息的手段。看板卡片包含相当多的信息并且可以反复使用。常用的看板有两种:生产看板和运送看板。看板比较直接,且有目共睹,容易管理。
04
标准化作业(SOP)
标准化是生产高效率和高质量的最有效管理工具。生产流程经过价值流分析后,根据科学的工艺流程和操作程序形成文本化标准,标准不仅是产品质量判定的依据,也是培养员工规范操作的依据。这些标准包括现场目视化标准、设备管理标准、产品生产标准及产品质量标准。精益生产要求的是“一切都要标准化”。
05
全面生产维护(TPM)
以全员参与的方式,创建设计优良的设备系统,提高现有设备的利用率,实现安全性和高质量,防止故障发生,从而使企业达到降低成本和全面生产效率的提高。不仅体现5S,更重要是工作安全分析,安全生产管理。
06
运用价值流图来识别浪费(VSM)
生产过程中到处充斥着惊人的浪费现象,价值流图(Value StreamMapping)是实施精益系统、消除过程浪费的基础与关键点:
07
生产线平衡设计
生产线平衡是精益制造计划的重要组成部分,因为不平衡会产生浪费。生产线平衡是平顺化的一部分,它是平衡生产的艺术。这使生产能够有效地满足客户需求,同时避免批量生产。它导致整个价值流中的库存、资本成本、人力和生产提前期最少。
08
拉动生产(PULL)
所谓拉动生产是以看板管理为手段,采用“取料制”即后道工序根据“市场”需要进行生产,对本工序在制品短缺的量从前道工序取相同的在制品量,从而形成全过程的拉动控制系统,绝不多生产一件产品。JIT需要以拉动生产为基础,而拉系统操作是精益生产的典型特征。精益追求的零库存,主要通过拉系统的作业方式实现的。
09
快速切换(SMED)
快速切换的理论依据是运筹技术和并行工程,目的是通过团队协作最大程度地减少设备停机时间。产品换线和设备调整时,能够最大程度压缩前置时间,快速切换的效果非常明显。
为了使停线等待浪费减为最少,缩短设置时间的过程就是逐步去除和减少所有的非增值作业,并将其转变为非停线时间完成的过程。精益生产是通过不断消除浪费、降低库存、减少不良、缩短制造周期时间等具体要求来实现的,降低设置时间是帮助我们达到这一目标的关键手法之一。
10
持续改善(Kaizen)
当开始精确地确定价值,识别价值流,使为特定产品创造的价值的各个步骤连续流动起来,并让客户从企业拉动价值时,奇迹就开始出现了。
这里列出的步骤仅供参考,因为实施精益生产是必须要对企业现场进行调研诊断后,根据现场实际情况去设立针对性的实施步骤的。
2.具体步骤
◆ 第一步:现场5S活动;
◆ 第二步:看板管理;
◆ 第三步:价值流分析;
◆ 第四步:标准化作业;
◆ 第五步:拉动生产;
◆ 第六步:JIT生产;
◆ 第七步:均衡生产;
◆ 第八步:快速切换;
◆ 第九步:TPM管理;
◆ 第十步:持续改善。
01 中国五百强制造业企业的精益实践案例
企业背景
该家企业在中国有多家工厂,信息化建设相对完整,且公司领导层十分重视精益生产,全员致力于有效践行精益生产。
落地效果
最初,先选择有千名员工的苏州工厂为试点,具体做了CI(合理化建议)、Andon(安灯)、Safety Observation(安全观察)、TPM(全员生产维护)以及销售订单流程管理。
试点成功后进行推广,目前已在十余家工厂落地精益生产管理具体场景,也做了部分系列延伸,比如食堂刷卡、速度门等等。
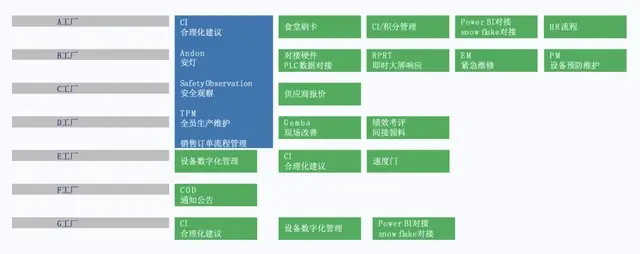
公司内部有自己的微软全家桶、SAP,他们使用无代码平台将组织架构进行打通,实现了全球10万+统一账号打通,顺利对接自己的PowerBI,实现了单点登录、验证码等多重安全保障;90天用户登录安全保障;根据操作系统,自动切换中英文。
基于无代码平台开发接口,支持前端JSP、SKD部署及开发,通过数据打通,实现SAP、生产、硬件数据联动。
过去,企业的数字化精益生产是通过一面黑板来操作,流程复杂,难以及时跟进;
如今,全部迁移至无代码平台进行系统化处理,操作便捷,及时性强。
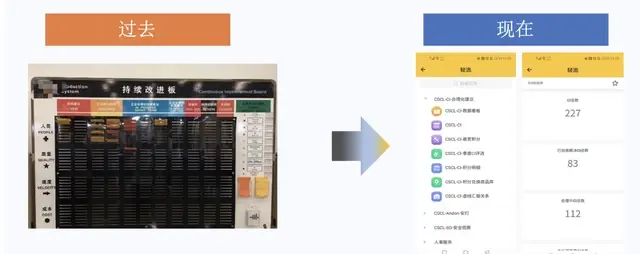
借鉴与思考
做精益生产的关键性因素就是要取得管理层及一线员工层面的统一认可,这家企业对精益生产的推广方法也具有一定的借鉴意义,比如设置兴趣小组、以奖代罚、重视支持。
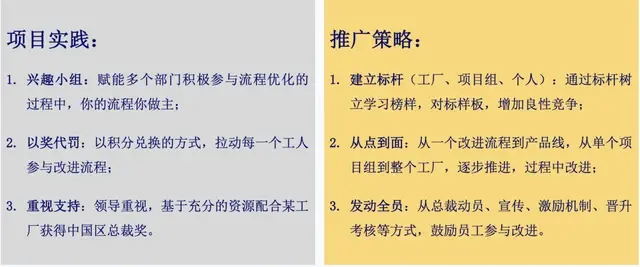
无代码平台平台对客户来说不仅仅是精益生产,也打通了上下游的价值链,包括链接海外集团总部、链接管理层以及一线工人、链接硬件、链接供应商、链接代理商/客户,让未来充满更多想象。
02 全球领先企业的精益实践案例
企业背景
该家企业顺应互联发展浪潮,内部有多套垂直场景SaaS类软件,比如微软全家桶、BPM及低代码平台、SAP、企业微信、OCR系统。但这些系统只能解决某一个场景问题,当企业业务发生变化,就需要进行原系统的二次开发,或者直接采购新的系统去满足。这种业务一发展就要开发系统,购买系统,给企业造成了巨大的IT运维压力。
在这样的情况下,这家企业找到了无代码平台,决定采用一套面向用户的无代码平台,以此解决信息的流转,打通已有系统,实现数据流闭环,提高IT系统建设效率。
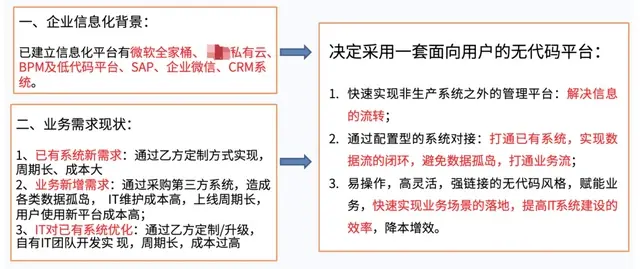
落地效果
无代码平台借助私有云,打通所有业务系统。
既可以把业务系统里的所有数据流转到无代码平台,也能够通过无代码平台发起业务数据,反向推送到一系列的业务系统中;下游的精益生产内容赋能给工人,工厂生产数据通过无代码平台进行分析,直接呈现给管理层。采购方面的成本控制与管理可以链接到下游的供应商,经销商等,与终端的物流用户也可以直接链接。
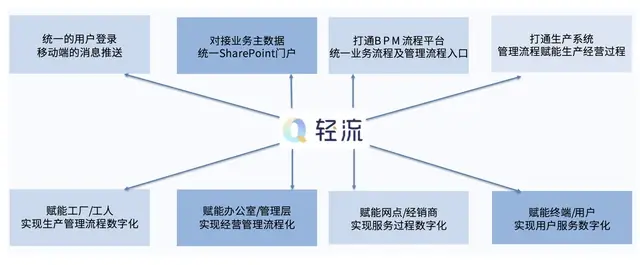
在2个月周期内,该企业产生892条建议数据, 实现458项优化点,347条待优化中,间接经济价值超过400万。
无代码平台以精益生产的场景为落地,与企业实现了更深层次合作,涉及周边所有上下游、终端客户的打通,这是以精益生产为开始,更深层次价值的体现。