涡轮转子用GH4141高温合金锻造工艺研究
液体火箭发动机涡轮转子工作环境一般比较恶劣一温度高、转速高、气动冲击大等。某型液体火箭发动机工作时涡轮转速达30000rpm,涡轮腔燃气温度高达1123K。为了增加涡轮转子机械强度以及保证轮盘和转动轴连接简单、可靠,涡轮转子可采用一体化结构,即转子叶栅与轮盘一体,同时传动轴与轮盘一体。结构上就显得盘轴外径尺寸差异大,采用棒料直接机械加工不太现实,也不经济,一般采用整体锻造而成。因此涡轮转子的锻造工艺将是转子机械性能的关键因素,一旦机械性能不合格,就会出现叶片断裂、轮盘龟裂等故障,造成发动机不能正常工作,直接导致发射任务失败。
GH4141材料的本身特性决定了其锻造加工温度范围窄,变形抗力大,因此确定科学合理的锻造工艺,确保工作可靠,降低产品废品率,节省生产成本有着重要意义。
1高温合金GH4141的化学成分和机械性能指标
高温合金GH4141使用要求的机械性能指标见表1。

2锻造基本原理
塑性材料南开始变形直至破坏分为三个阶段:弹性变形、塑性变形、破裂。弹性变形发生在变形的初期阶段,塑性变形是变形的第二阶段。当塑性变形达到极限状态时,金属的连续性和完整性被破坏,发生裂纹或断裂。锻造就是利用金属加热到高温所具有的塑性,使之变形到规定的形状而不产生破裂。
金属的塑性变形微观上是晶体的塑性变形,晶体有单晶体和多晶体,通常使用的金属大都是多晶体,是由大量的形状、体积和晶格方位不同的晶粒所构成的晶体。各个晶粒间的晶界呈犬牙交错状态,每个晶粒内部的变形都在晶界上受到晶界杂质和相邻晶粒的阻碍,变形抗力大。同样成分的金属,晶粒愈细,变形抗力愈大,强度亦愈高。同时,由于各个晶粒的晶格位向不同,塑性变形并不是在所有晶粒内同时和相同程度地发生着,而是首先在那些最有利于发生滑移的晶粒内发生,因而,晶粒越细塑性变形就越均匀地分布在更多的晶粒内,塑性越好,使金属能承受更大的整体变形而不会破裂。
金属高温下发生塑性变形时,晶粒在滑移面附近发生晶格畸变和晶粒破碎,在高温下原子的扩散速度很大,原子排列首先趋向正常,这个过程为回复,回复只能消除品格畸变,不改变晶粒的形状和大小,也不能消除破碎的晶粒。随着原子活动能力进一步增强,破碎和变形的晶粒就以碎晶块为核心成长为新的细小晶粒,这个过程称为再结晶。再结晶后晶粒得到细化,塑性改善,可继续进行锻造。一般随着锻造进行,金属温度快速降低,塑性随之变差,同时再结晶速率也会快速降低,此时如果继续使之发生变形,变形抗力增大,会出现破裂。可再次加热,提升温度,同时充分发生再结晶,改善塑性。然而如果再结晶过程中,金属的温度继续升高,则再结晶后晶粒就会聚集长大,发生二次再结晶,使材料的性能变差。
3影晌金属塑性的因素
除了金属本身的化学成分和组织状态对其塑性有重大影响外,还受以下条件影响。①变形温度。一般塑性变形的温度越高,则再结晶的速度越快,塑性越好,可改善金属的锻造性能。但是,变形温度过高,晶粒长大,塑性则急剧下降。②应变速率。即单位时间内的相对变形程度。随着应变速率的增加,回复和再结晶不能及时克服加工硬化的作用,使塑性下降。因此,对于本质塑性较差的材料,应采取较低的应变速率,通过多次锻造,每次回炉时,通过回复和再结晶,使塑性改善。③应力状态。金属在经受不同的法变形时,其内部的应力状态也不同。例如,挤压时的应力状态是三向压应力;拉拔时则为两个方向受压,一个方向受拉;自由锻时坯料上下同部位的应力状态不完全相同。压应力使金属质点间趋向紧密,拉应力则使它们趋向分离而易导致破裂。因此在三个方向的应力中压应力的数目越多,金属的塑性越好。但是,在压应力作用下变形时,金属内部的摩擦力增大,变形抗力增加。
4锻造对金属组织和性能的影响
锻造不仅可以使金属改变形状,还可使其内部组织发生如下变化,从而影响材料的机械性能。①材料内部空洞性缺陷,如疏松、微裂纹等缺陷,在锻造压应力作用下可以压实直至焊合。改善组织致密性。②细化晶粒,锻造时粗大的晶粒在巨大的压应力作用下得到充分的破碎。经过再结晶后重新形成晶粒,形成晶粒的大小与变形温度和变形程度有关。一般地,在达到一定的变形程度后变形温度越低,晶粒越细。③形成纤维组织。锻造金属发生塑性变形时,金属内部非金属夹杂物沿着变形方向呈带状或链状分布。这种组织称为纤维组织。纤维组织的形成使金属的机械性能出现方向性,沿纤维方向的塑性和韧性高于垂直纤维方向。但金属的强度在两个方向上差别不大。
5GH414l材料涡轮转子毛坯的锻造工艺研究
5.1锻料情况
锻料如图1所示,图1中的左图为锻造前毛料图,右图为锻造后毛坯图。
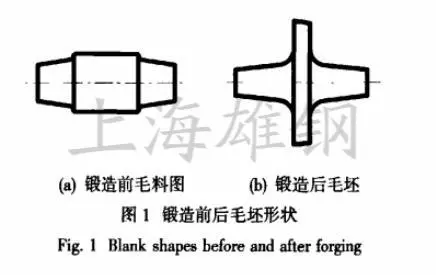
5.2原有锻造工艺
GH4141材料晶界结构属多晶体结构,具有合金化程度高,高温下机械性能好,变形抗力大、塑性低等特点。由图l可见,毛坯状态比毛料状态中心轮盘直径增加了一倍多,轴径缩小近一倍,材料变形很大。而涡轮工作环境要求转子具有好的高温性能,相应的锻造工艺要求也高。
原有的简要锻造工艺见表2。
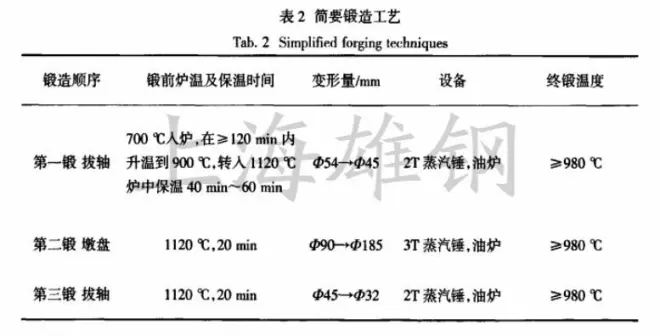
采用界于自由锻和模锻之间的半模锻。考虑到锻造前后毛坯结构的巨大变化,不可能通过一次锻造使形状到位。整个锻造过程分3个阶段,包括拔轴、墩盘、拔轴。使用两套模具,各分上、下模。第一、第1锻拔轴使用一套,第二锻墩盘使用一套。模具简图见图2。
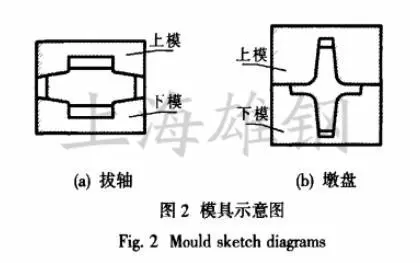
第一锻进行两侧轴的锻造,在锻造过程由于材料与环境的热交换使其温度下降,塑性降低,不宜继续进行锻造,将材料回炉重新加热后进行第二锻墩盘,变形满足要求后回炉重新加热后进行第三锻拔轴。
经过该锻造丁艺成形后,材料中如疏松、微裂纹等缺陷得到消除,改善了组织致密性。锻造所形成的纤维组织的方向与实际工作中受力情况相适应,满足要求。同时采用半模锻,金属内部的应力状态相对较好。而实际锻造出的产品合格率低,批次稳定性差,产品成本高,下面主要从影响锻造性能的其余两个方面进行分析。
从锻造温度上分析,经过早期丁艺摸索,GH4141材料在接近1110℃时晶粒会急剧长大,1120℃以上时晶粒度变化不大。第一锻加热炉温度为1120℃,锻件处于晶粒长大温度区域,锻造时轴上粗大的晶粒在巨大的压应力作用下得到充分的破碎。再经过第二锻、第三锻的回炉加热,由于温度1120℃略超出了晶粒急剧长大温度,轴上破碎的晶粒在经过回复和再结晶后部分晶粒会发生二次再结晶,但在第三锻时轴上的晶粒在巨大的压应力作用下又得到了充分的破碎。在后续专门的热处理工艺中得到回复和再结晶,晶粒细化,以使轴的强度满足要求。第二锻后在进行第三锻时,由于炉温偏高,轮盘上破碎的晶粒在经过回复和再结晶后部分晶粒会发生二次再结晶,使轮盘的机械性能有所降低。而在实际操作中各锻件的保温时间略有差异,导致各锻件晶粒中出现二次再结晶程度有差异,严重二次再结晶的锻件会使材料性能不合格。轮盘机械性能合格和不合格所对应的晶粒度见图3。
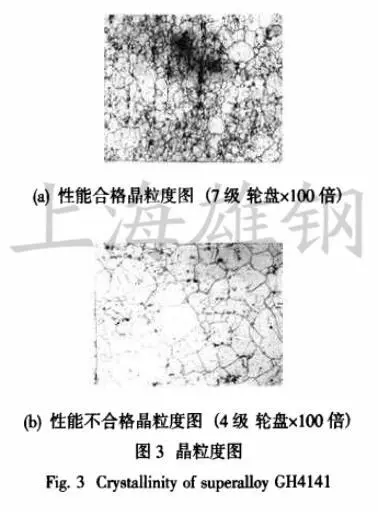
从应变速率上分析,共用三锻,每轮变形速率偏大,GH4141高温合金本身高温下塑性低,变形抗力大,会造成每轮锻造操作时间较长。尤其是轮盘直径由φ90mm-φ185mm只经一次墩盘,变形过大,锻造中随着材料与环境的热交换导致温度降低,材料塑性变差,在大的锻造应力作用下增大了发生破裂的可能性。另外,从操作方便程度上分析,表面上看仅用3轮锻造便完成了锻造成型,似乎操作工作量小。实际上考虑到每轮锻造时材料与环境的热交换导致温度降低,塑性变差,这就要求操作人员在尽可能短的时间内使材料的变形达到要求,操作难度大。
5.3改进后的锻造工艺
鉴于原有锻造工艺种种缺点所导致锻造废品率较高,批次一致性较差等原因,对原有的锻造工艺进行了改进,改进后的简要工艺见表3。采用半模锻造,将整个锻造过程分为五个锻造阶段,共使用三套模具,各分上、下模。前两锻拔轴,使用一套。第三、第四锻墩盘,使用一套。第五锻拔轴,使用一套。
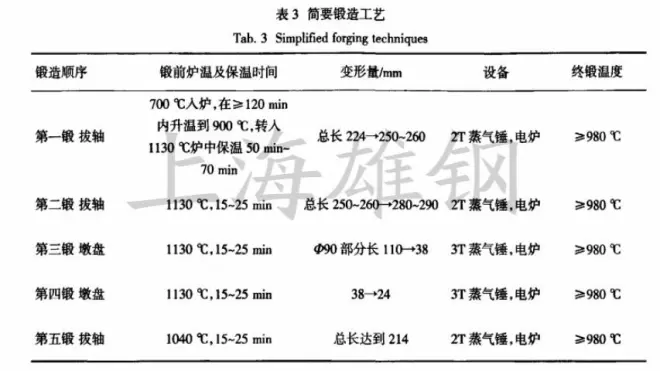
第一锻进行两侧轴的锻造,通过在模具上刻线来控制变形量,满足要求后将材料回炉重新加热进行第二锻拔轴,使用同样方法控制变形,之后将材料回炉加热进行第三锻墩盘,使用限位环来控制变形量,之后将材料回炉加热进行第四锻墩盘,靠模具本身形状控制变形,之后将材料回炉加热进行第五锻拔轴,模具上刻线来控制变形量。前四锻锻造炉温为1130℃,第五锻锻造前炉温为1040℃。
该工艺继承原有工艺中锻造后形成的纤维组织的方向与实际下作中受力情况相适应的优点,同时仍采用半模锻,保持了金属内部的应力状态相对较好的特点。改进后的工艺影响分析如下:从锻造温度上分析,前四锻炉温为1130℃,第五锻炉温为1040℃。第一锻、第二锻拔轴,轴上晶粒在两次巨大的锻造压应力作用下均得到充分的破碎。之后均经过回复和再结晶,由于温度为1130℃,高于晶粒急剧长大温度,保温时间为15~25min,一部分晶粒会发生二次再结晶,但在第五锻拔轴时轴上的晶粒在巨大的压应力作用下又得到了充分的破碎。在后续专门的热处理工艺中又得到回复和再结晶,晶粒细化,以使轴的强度满足要求。第三、第四锻墩盘过程中轮盘上粗大的晶粒在巨大的锻造压应力作用下得到充分的破碎。由于第五锻炉温仅为1040℃,低于ll10℃晶粒会急剧长大温度,保温过程中轮盘上晶粒只发生回复和再结晶,不会出现二次再结晶,晶粒不会长大。整个锻造过程温度合理,无论是轴上的还是轮盘上的晶粒均得到了细化,避免了二次再结晶发生,保证了强度。
从应变速率上分析,分为五次锻造,使变形速率降低,较好地适应了GH4141高温合金高温下塑性低、变形抗力大的特点,避免了发生破裂的可能性。同时由于变形速率降低,操作人员有较充分的时间来操作,降低了操作人员的工作强度。
改进后的锻造工艺很好地解决了原有工艺的缺点,可操作性强。产品合格率得到大大提高,批次稳定性好,节约了成本。
6结论
依据锻造原理,从影响金属塑性的因素以及锻造对金属组织和性能的影响等方面,对原有的GH4141材料涡轮转子毛坯的锻造工艺和改进后锻造工艺进行了分析,结论如下:
1)原有的锻造T艺中轮盘处晶粒存在二次再结晶的可能,导致部分晶粒粗大,材料性能下降;改进后的锻造工艺,轮盘和轴中晶粒不存在二次再结晶问题,有效保证了强度要求。
2)原有的锻造工艺中,每次锻造变形速率偏大,在大的锻造应力作用下增大了发生破裂的可能性。改进后锻造工艺变形速率降低,避免了破裂的发生。
3)原有的锻造工艺对操作人员的技术水平要求高,操作难度大。改进后锻造工艺降低了操作人员的难度。
4)改进后锻造工艺产品合格率高,可操作性强,批次稳定性好,节约了成本。
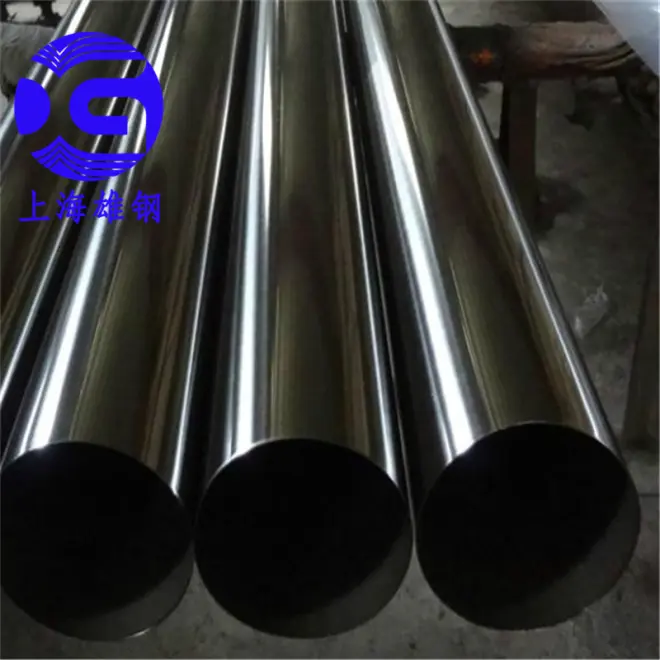