丰田公司“持续改善”的主要方法
天行健精益生产顾问认为使“持续改善”取得持续效果的方法主要有两个,那就是在丰田公司持续进行得QC小组活动和“提案活动”。
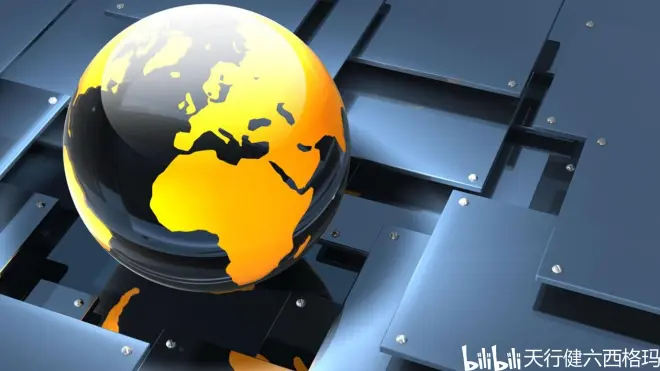
“改善”,并没有什么至深至奥的理论体系,也无须什么繁琐复杂的程序和手段。它所需要的是认真求实的敬业精神、追求完美的细致作风和永无止境的进取意识。
在丰田公司的生产现场,在各条生产线的上方,高悬着这样一幅标语——“好产品,好主意”。QC小组活动和“提案制度”的目的和意义在这幅标语中得到了充分的体现。意思是说要生产出好产品,又要拿出好主意;进而,只有持续不断地拿出好主意,才生产出更好的产品。
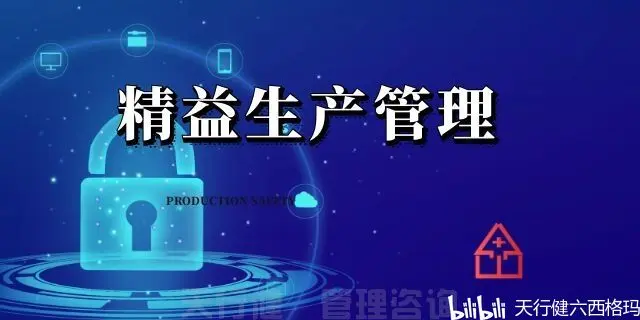
丰田公司的QC小组是员工们进行“持续改善”的群众性组织。它与作业或工作现场的正式生产、经营组织有着直接的关系。丰田公司的全体员工都参加到某一个QC小组中去。包括直接的生产部门在内,66,000多名员工参加到数千个QC小组当中,自主而持续地开展质量管理、降低成本、设备保全、保障安全、研究替代能源等方面的改善活动。
与QC小组活动密切相关的是“提案制度”,也就是我们耳熟能详的“合理化建议制度”。“提案制度”在丰田公司已经有了57年的历史。1950年6月,丰田公司现任名誉董事长丰田英二参观考察美国福特汽车公司,将该公司的“建议制度”引入到丰田公司。丰田公司原副社长石田退三又将其逐步“改善”,形成了日前丰田公司持续广泛开展的富有日本特色的“提案制度”。
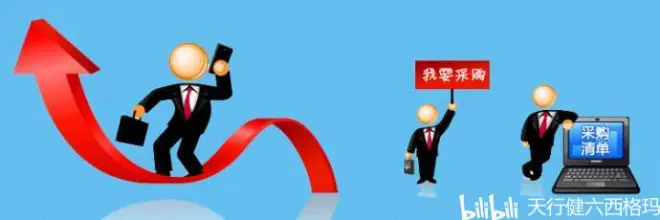
据统计,1986年丰田公司合理化建议书为2,648,710件,平均每名员工47.7件,员工参加率为95%,采用率达到了96%。自1989年以来,根据员工提出的合理化建议而减少的成本就达到了数亿美元,其中仅1997年一年就减少7,200万美元。
最新资料提供:2005年丰田公司员工的合理化建议达到了60多万件,采用率达到了99%。由此可见,合理化建议活动在丰田公司的经营管理中的作用和产生的巨大效益。可以说,丰田公司今天在精益生产上的一切成果都是通过激励全体员工“持续改善”而带来的。
丰田公司合理化建议活动中提案的件数、参加率、采用率的变化