新材料研发,学术研究如何应用到实际制造中
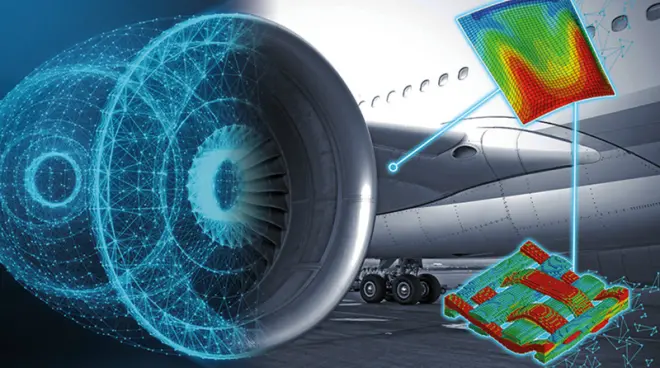
客户越来越担心他们的选择对环境的影响,行业监管机构也是如此。然而与此同时,人们通常会根据价格做出最终的购买决定。因此,毫不奇怪,许多制造商努力在眼前的成本和生产率限制与长期可持续发展目标之间寻求平衡。
然而,集成计算材料工程(ICME)的最新进展使得设计和生产结合了更高的可持续性、成本效益和制造效率的产品变得更加容易。
制造商对材料的选择对产品的整体成本和整个生命周期的环境影响都有巨大的影响。ICME认识到材料特性在产品性能中的关键作用,利用模型和软件工具将材料置于产品设计和工程的中心。例如,利用ICME,公司可以设计出充分利用给定复合材料性能的产品,以减少制造过程中的浪费。通过使用ICME,制造商可以消除对物理原型的需求,进一步降低材料消耗。ICME的另一个关键优势是,它可以在传统方法的基础上减少多达20%的组件重量,同时确保它们的强度,使它们更不容易出现故障,从而使产品更节能、更耐用。ICME还帮助制造商遵守安全和可持续发展法规。
那么,考虑到ICME的优势和这门学科已经存在几十年的事实,为什么没有更多的制造商使用它呢?答案是,直到最近,采用ICME都是昂贵且耗时的。因此,它的使用仅限于航空航天和汽车等少数行业,在这些行业中,制造商面临着使用新型轻质复合材料提高车辆燃油效率的压力。
我们决心帮助我们所有行业的更多客户从开发和使用新材料中获得商业优势,在过去的17年里,我们一直与领先的学术研究人员合作,解决如何使ICME更容易获得、负担得起和更容易使用的问题。结果是海克斯康的10xICME。
更智能地使用数据
长期以来,广泛、经济地使用ICME的最大障碍之一是数据管理。高效、经济的ICME依赖于将材料工程的准确信息无缝集成到产品设计和制造解决方案中。
10xICME是第一个克服安全数据管理挑战的ICME解决方案,这样制造商就可以利用整个供应链中关于材料的一致和可信的数据源,并嵌入从供应商的材料卡到制造到最终零件的材料的数字双胞胎。没有有效可靠的数据管理系统,使用不同系统的团队很容易丢失重要的测试信息。为了提高效率,材料生命周期管理必须能够将模拟系统的虚拟数据与物理材料测试、CT扫描和计量数据结合起来使用,而没有任何信息丢失的风险。
能够高效地使用由强大的仿真工具生成的材料数据对于使设计和工程更加可持续(包括材料选择)具有重要作用。通常,一旦工程师找到了一种材料的设计,他们就会生产并物理测试多个样品。通过使用计算机模拟对材料进行虚拟测试,工程师不仅可以对先进材料的性能极限进行全面分析,还可以减少制作多个物理测试样品的需求。例如,Camanho模型使航空航天复合材料性能能够从样片到零件进行精确预测。这让工程师们对性能预测更有信心,因为先进的复合材料不被视为“黑色金属”。使用材料生命周期管理,他们可以与材料专家一起审查物理和虚拟测试的相关性,并将这些安全裕度应用到他们的设计中,以减少材料的使用。
ICME解决方案还考虑了制造过程如何影响每种材料的独特性能和性能极限。有了这些信息,制造商可以优化设计,使用最少的材料,从而减少浪费。