WSS威士|粉末冶金用什么刀具加工
粉末冶金(PM)是由金属粉末与金属粉末或金属粉末与非金属粉末按所需比例混合后在模腔内压制成型,随后通过烧结和精整变成粉末冶金机械零部件的工艺。多孔材料是PM零部件取得广泛应用的特点之一。包含可加工性等在内的PM部件的绝大多数特性不仅与其合金化学成分有关,而且和多孔材料的孔隙率有关。很多结构部件的孔隙率多达15%~20%,作为过滤系统的部件的孔隙率很有可能达到50%。而煅造或HIP(热离子压铸)零部件孔隙率为1%或者更少。HIP材料适合在汽车和飞机里应用,但是它们可以获得更高抗压强度水平。
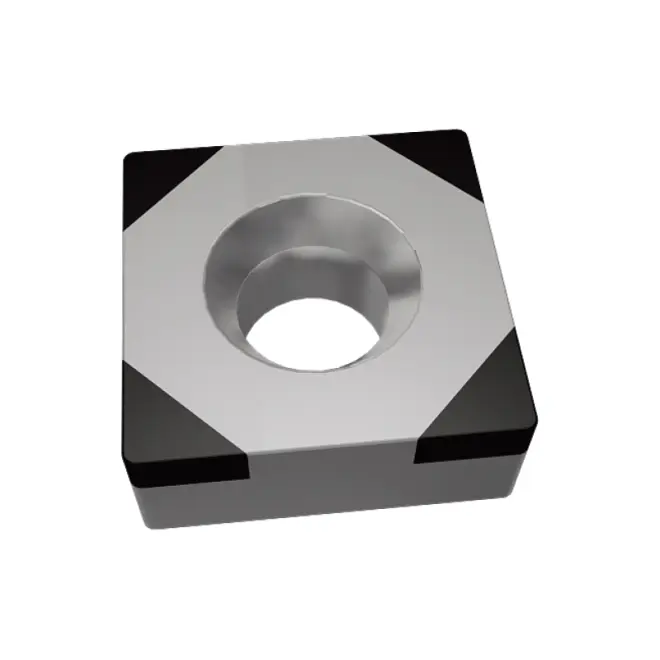
铁基、镍基粉末冶金是如今粉末冶金的最重要的构成部分,其制品大部分用以汽车、机械及家用电器的零部件等,如粉末冶金齿毂,粉末冶金同步带轮,粉末冶金齿轮等。而粉末冶金零部件又特别难加工,现在还没有一种完全有效的刀具能加工粉末冶金材料,主要是因为粉末冶金区别于其他铸铁、淬火钢材料,每家制造的粉末冶金材料成分、占比都不相同,并且具有多孔性结构,宏观硬度虽为HRC20-35,但构成部件的颗粒硬度会达到HRC60,这种硬颗粒会导致刀具严重磨损。
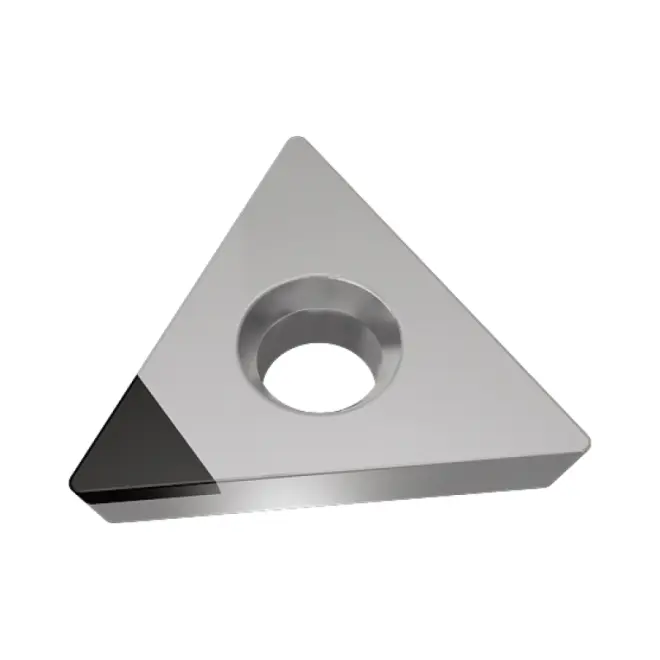
封闭式表层多孔材料由金属(通常是铜)或聚合物浸渗完成。网上有人认为浸渗的作用象润滑剂,但大多数的实验数据显示,浸渗真正的优点就在于关闭表层多孔材料,从而阻止切削刃的微观疲劳,降低刀片的振颤,提高刀具寿命和降低表面粗糙度。采用浸渗处理后,刀具寿命提高2倍。
实践活动说明,在粉末冶金材料中加入例如MnS、S、MoS2、MgSiO3和BN等添加剂能够提高刀具寿命。这种添加剂通过使切屑比较容易从工件上分离、断屑,并且能够阻止积屑瘤的形成和润滑切削刃来提升材料的可加工性。提升添加剂的使用量能够提高可加工性,但也会降低材料强度和韧性。
现阶段普遍地用来PM行业刀具材料通常是立方氮化硼(CBN)刀片、不涂层和涂层金属陶瓷及其改进的涂层煅烧硬质合金。这种刀具材料在切削粉末冶金材料时都有着耐磨损、耐刃口破裂与不产生积屑瘤的特点,并可以获得低的表面粗糙度。
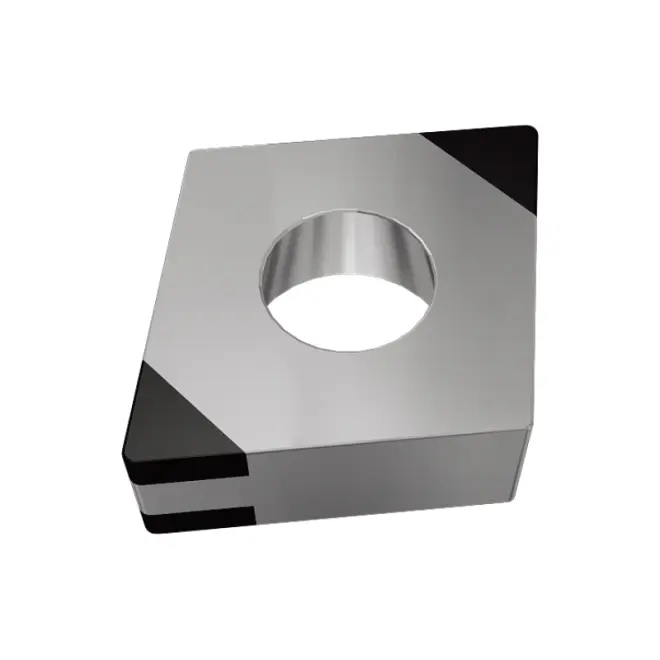
CBN刀片以其高韧性和耐磨性而适合于PM部件的生产加工。CBN刀片早就在HRC≥45的铸铁件和铸铁加工中采用数年。但,因为PM合金独特的特性及其显微硬度和宏观硬度的巨大区别,使CBN刀片能用来生产加工软到HRC25的PM零件。关键性的参数是颗粒的硬度,当颗粒的硬度超过HRC50时,不管宏观硬度值是多少,CBN刀片是可以用的。CBN刀片显著的缺点就是它的韧性欠缺。假如是断续切削或孔隙度比较大,必须加强CBN刀片负倒棱和比较重的珩磨等在内的刃口。假如是轻载切削,采用通过珩磨处理切削刃就可以完成生产加工。
来源:www.wss.com.cn