关于TPU的一些知识
TPU的开发和商业化可以追溯到上世纪50年代,1950年,BF Goodrich公司的Schollenberger等人开始研制TPU,1961年,Goodrich公司(现为 Lubrizol公司)正式推出以Estane Vc为代表的商品化TPU产品。上世纪90年代,随着外资TPU生产企业在中国投资建厂,我国TPU工业开始起步并逐步发展。
TPU是热塑性聚氨酯弹性体的简称,英文是Thermoplastic Polyurethanes,是一种由二异氰酸酯、扩链剂、多元醇组成的多相嵌段共聚物。
如下图所示,TPU根据二异氰酸酯的种类不同,分为芳香族TPU和脂肪族TPU,芳香族TPU为二苯甲烷二异氰酸酯(MDI),脂肪族TPU为六亚甲基二异氰酸酯(HDI),两者的性能差异主要集中在耐黄变性上。
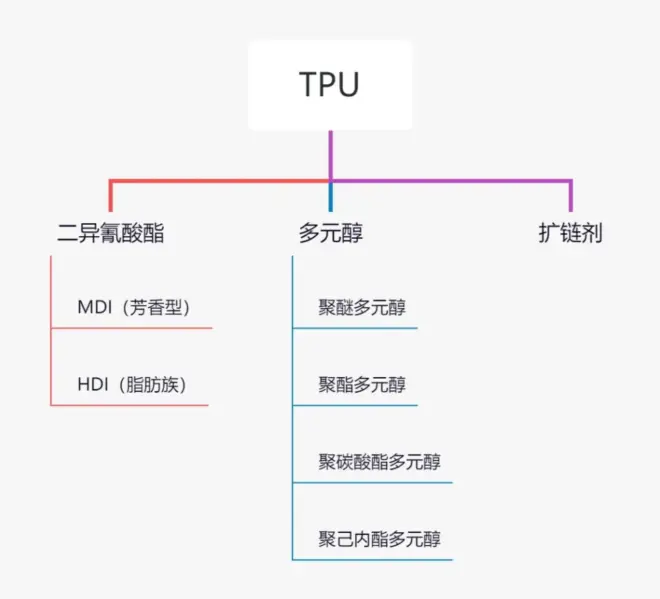
日常生活中用到的TPU大部分都是芳香族TPU,它之所以容易黄变,是因为MDI上的苯环结构,MDI在两个苯基之间有亚甲基桥,这个亚甲基在紫外线的环境下很容易被氧化,从而失去亚甲基桥上的氢,这种化学反应在两个芳环之间形成共轭体系,称为醌亚胺。尽管这种氧化反应对于TPU的物理性能影响较小,但是会导致TPU不可逆转的泛黄。用HDI体系TPU发泡制成的中底还可以显著提高耐紫外黄变性能。
同时,MDI体系聚醚TPU发泡后蒸汽成型中底的落球回弹率在60%左右,而HDI体系的TPU可以达到70%以上,并弱化中底的表面颗粒感。因此HDI体系TPU逐渐成为中高端运动鞋中底材料的最佳选择。
以下内容节选自《国内外热塑性聚氨酯材料的技术和应用进展》(《聚氨酯工业》2023年第38卷第1期)
早在1993年,BASF公司的Fischer等公开了一种高压釜发泡制备ETPU粒子的技术,使用的是邵氏硬度85-100的TPU粒子,其蒸汽成型温度超过145℃。2006年,Prissok等使用邵氏硬度44-84的聚醚型TPU,以超临界CO2等作为发泡剂,制得微孔发泡TPU颗粒。这些发泡颗粒填充到模具后,往模具中通入100-140℃的水蒸气,使颗粒表面微熔并粘接到一起,冷却后可以得到具有模具形状的发泡TPU制品,水蒸气成型技术使超临界发泡ETPU颗粒的商业化成为可能。
2012年德国阿迪达斯公司与巴斯夫公司联合开发了以发泡TPU(商品名为Infinergy)为中底材料的跑鞋品牌Energy Boost,由于采用邵氏硬度80-85的聚醚型TPU为基材,相较于乙烯-醋酸乙烯共聚物(EVA)中底,发泡TPU中底在0℃以下的环境中仍能保持良好的弹性和柔软度,使穿着舒适度得到提升,受到市场广泛认可。
超临界发泡ETPU的制备一般经历4个步骤:一是气体扩散, 在一定温度和压力下发泡剂以超临界流体状态均匀分散到TPU中形成TPU-发泡剂均相体系;二是气泡成核,采用降压或升温的方式使TPU-发泡剂均相体系在短时间内达到热力学不平衡,发泡剂溶解度降低、析出并逐渐形成气泡核;三是泡孔生长,在持续的降压或升温下,发泡剂从超临界状态转变为气态进人气泡核,使泡孔逐渐长大;四是泡孔固化,通过快速降压或冷却,TPU熔体强度增大,泡孔结构稳定和固化。
超临界发泡ETPU的工艺路线可分为高压釜发泡、连续挤出发泡和注塑发泡3种,高压釜发泡、连续挤出发泡占了绝大部分。目前商业化的超临界发泡ETPU主要是高压釜发泡,但近几年连续挤出发泡也快速发展,所需要的发泡剂用量远少于高压釜发泡工艺,生产效率较高,产品质量较稳定,但对设备和工艺的要求较高,而高压釜发泡所得ETPU粒子反弹性能较高,密度较低。此外,TPU颗粒还可以利用注塑机进行超临界流体直接注塑发泡,比如New Balance公司慢跑鞋上使用的N2缓冲技术便是超临界注塑发泡TPU。
影响高压釜发泡效果的因素大致有以下4个方面:发泡剂、发泡温度、超临界流体压力以及TPU类型和熔点、硬度等物理性能。泡沫的发泡倍率主要由温度决定,而泡孔大小和密度主要由CO2/N2的压力决定。聚合物发泡材料的泡孔直径越小、泡孔密度越均匀,其力学及隔热性能就会越高。泡沫强度随着发泡倍率的增加而显著下降,但泡沫回弹性变好。
利用水和超临界二氧化碳作为共发泡剂可有效提高发泡材料的性能:利用高压釜制备聚合物发泡材料的方法主要为快速升温法和快速泄压法,但目前用快速泄压法制备发泡TPU普遍存在发泡倍率不高的问题。在不加水的情况下,TPU发泡颗粒的泡孔结构呈现边缘泡孔直径小、中间泡孔直径大的特点,并在靠近边缘的位置有一层不发泡的边缘层。加入水后,TPU发泡颗粒的边缘层厚度明显减小,这可能是由于在TPU发泡过程中,靠近颗粒边缘的CO2容易外溢,而加水后可以阻止其外逸,从而使TPU颗粒的边缘部位更容易发泡,减小了边缘层厚度。另外加水后,TPU发生部分水解,使熔体强度降低,气泡更容易长大,最终得到更大的泡孔和更高的发泡倍率,但如果加人过量水,则会出现泡孔塌陷和合并的现象。
浸渍的饱和时间、温度也有影响:加水后,随着饱和温度的升高,发泡颗粒的发泡倍率上升,泡孔密度下降,泡孔平均直径增大。与饱和温度为150℃相比,饱和温度为190℃时的发泡倍率提高了94.8%,泡孔密度下降了77.7%,泡孔平均直径提高了95.2%。饱和时间为30min时,发泡倍率最大而边缘厚度最小,之后发泡倍率随着饱和时间的延长急剧下降,而边缘厚度明显增加。这可能是由于TPU在高温高湿的环境中易发生降解,而随着饱和时间的延长,降解变得越明显,进而使熔体弹性下降,CO2外溢加剧使得泡孔壁厚和边缘厚度增加,内部泡孔出现更多的塌陷与合并现象,泡孔密度降低,而泡孔平均直径增大。
超临界CO2和N2混合发泡剂对TPU发泡的影响:当CO2比例增大时,材料发泡所需要的温度降低,ETPU的泡孔尺寸明显变小变均匀,泡孔壁更薄,泡孔密度增大,同时ETPU熔点降低,熔程变宽,蒸汽成型的结合质量较好,成型的ETPU拉伸强度、撕裂与剥离撕裂强度增大。而随着N2的比例增大,ETPU在熟化过程中尺寸稳定性增强,收缩率减小,制品的压缩永久变形率也逐渐减小。同样条件下,发泡剂选用混合气体比如50% C02+50% N2或25% CO2+75% N2可以制备密度较低的ETPU。
梯度加压控制泡孔结构的方法:即在5MPa压力下达到TPU-气体均相平衡,在温度不变的情况下,将压力增至15MPa,第二次加压时间控制在1-8min,然后泄压发泡。利用CO2在TPU中较快的扩散速度,使TPU颗粒中心和边缘位置发泡剂含量形成一定的梯度。发泡时,中心区域泡孔尺寸较大,边缘位置泡孔较小而泡孔密度较高,从而保证了泡沫高密度外层的强度和硬度,以及低密度中心区域的轻质量和高能量吸收等性能。
近年来,随着超临界发泡技术的进步,TPU发泡颗粒做得更轻、更有弹性,比如安踏公司通过对TPU进行改性,引人了聚酯弹性体、聚酰胺弹性体等材料,将改性TPU颗粒发泡,再通过蒸汽成型制作ETPU复合中底鞋材,其成型鞋底的密度可以低至0.1g/cm3。目前研究和探索的重点是如何把密度降低到0.05g/cm3,同时提升拉伸和撕裂强度。