高速电主轴振动异常的原因分析与解决方法探讨
在现代制造业中,高速电主轴作为关键的机械部件,在加工、切削等工艺中发挥着重要作用。然而,有时候这些高速电主轴可能会出现振动异常,影响加工质量、设备寿命甚至操作安全。本文将深入探讨高速电主轴振动异常的可能原因,并提供相应的解决方法。
一、高速电主轴振动异常的原因分析:
不平衡: 高速电主轴的零部件质量分布不均匀,或者安装时的不平衡,都可能引起振动。
轴承问题: 轴承损坏、磨损或润滑不良,都会导致轴承振动异常。
装配与安装: 不合适的装配过程或安装松动可能导致电主轴的振动。
材料问题: 使用劣质或不适合的材料可能影响电主轴的平衡和稳定性。
冷却不良: 不良的冷却系统设计或操作可能导致电主轴过热,引发振动。
加工质量: 不良的加工工艺可能导致电主轴的不均匀受力,进而引发振动。
二、解决方法探讨:
动平衡: 通过在电主轴上进行动平衡操作,调整质量分布,消除不平衡引起的振动。
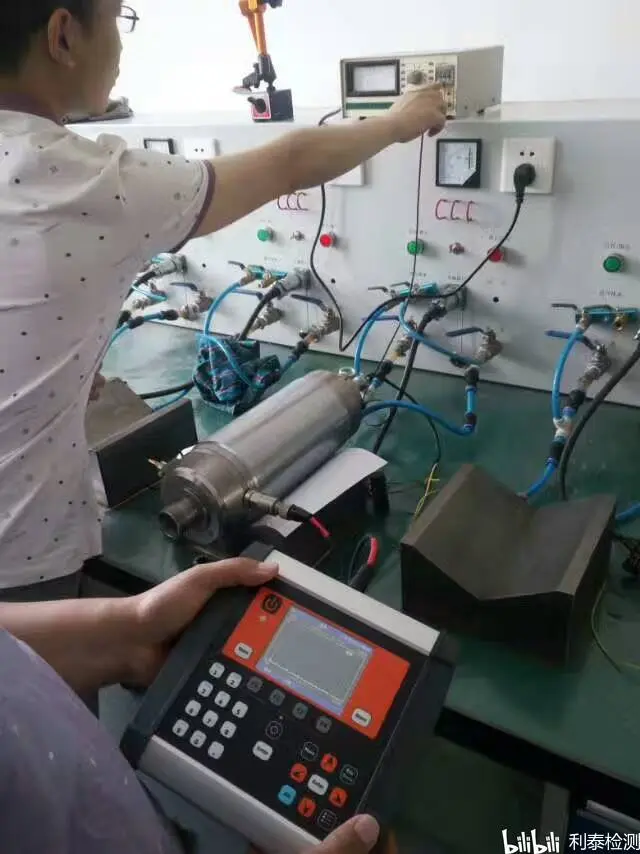
轴承维护: 定期检查和更换轴承,确保其良好状态,适时添加适当的润滑剂。
精确装配: 确保装配过程精确,紧固螺栓,避免松动。
选材优化: 使用高质量、合适的材料,避免材料问题引起的振动。
冷却改进: 设计合理的冷却系统,确保电主轴运行温度适中,避免过热。
加工优化: 优化加工工艺,避免加工不均匀引起的振动。
振动监测: 安装振动传感器,实时监测电主轴的振动情况,及时发现并解决异常。
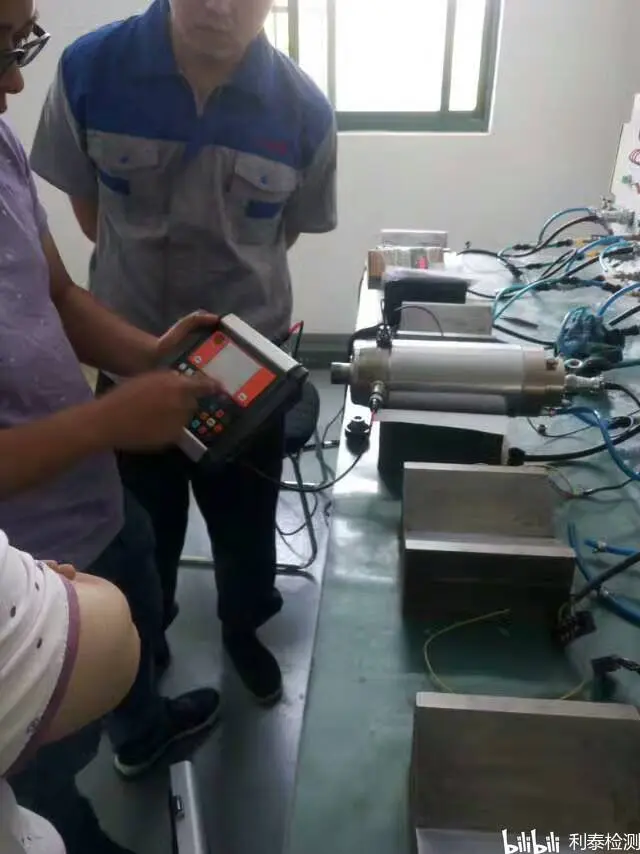
三、结论:
高速电主轴振动异常可能由多种因素引起,但通过合适的分析和解决方法,可以有效地减少振动对设备和加工质量的影响。定期维护、科学装配、适当的材料选择和冷却系统设计,都有助于确保高速电主轴的稳定运行,提高生产效率和产品质量。在实际应用中,综合考虑各种因素,制定合适的维护和操作策略,有助于降低高速电主轴振动异常的风险。
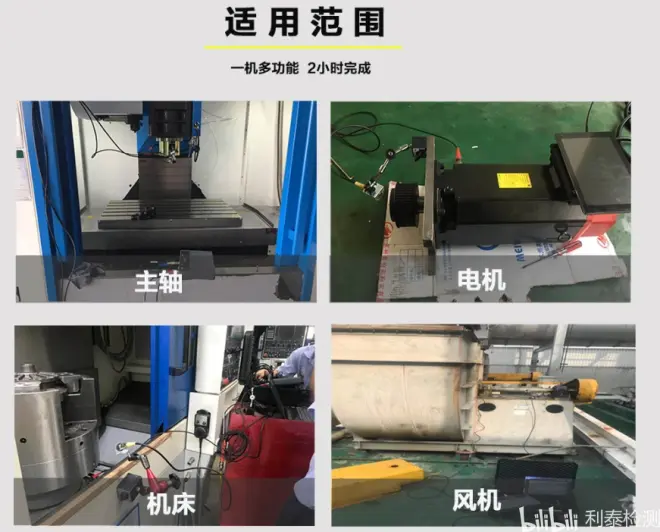