砂石厂专用除尘器
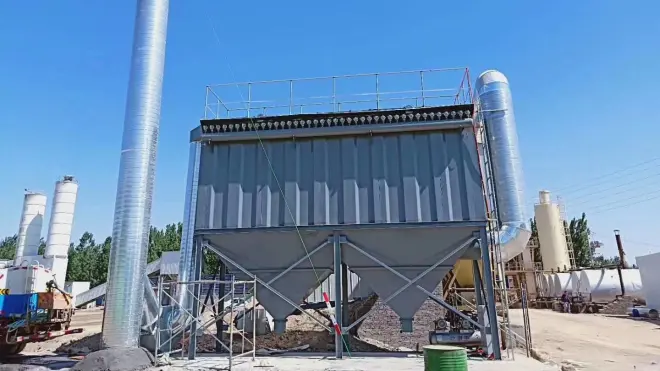
砂石厂专用除尘器,砂石料厂专用矿山除尘器设备,1) 除尘器本体壁板材料和结构确保耐压≥4000Pa、漏风率≤3%,维护保养到位可确保十年的使用寿命。 2) 花板采用Q235厚6mm的钢板制作。
3) 除尘器的管道及平台、除尘器图纸、扶梯、踏板的设计、选材、制作按照国家标准和有关设计规范执行。 4) 气包的设计、选材、制作按照国家标准和有关设计规范执行。
5) 脉冲阀、电磁阀选用优质产品。
6) 配套件采用标准化元件和标准化设备组件,以适合用户使用更换的需要。
7) 设备焊接件应严格执行国家有关焊接标准。根据零部件的重要性进行直观检查和相应的无损探伤检查。
本次除尘器采用脉冲袋式除尘器,除尘器设计最大处理风量为33300m3/h。此次我公司提供除尘器包含花板、壳体、滤件、脉冲喷吹系统、控制器、气包及检修平台等部件,由贵公司进行设计、生产、现场安装,所提供的负压气力除尘系统具有完善的、先进的高效率过滤性能,而且有收集和自动卸料简单的功效。
在此输送工况点除尘中,采用9-26-12.5D 功率45kw/6,风压4179-4028Pa,风量为22206-33300 m3/h离心风机,这样不仅避免了过高风量引起过滤元件的高负荷,也降低了投资费用。
在此输送工况点除尘入口处,均加装了手动隔离阀,用户可以根据实际除尘的需要,增加或减少吸尘风量和除尘点,这样不仅有利于节能降耗,提高了吸尘效率,实现远程和就地操作运行的便利。
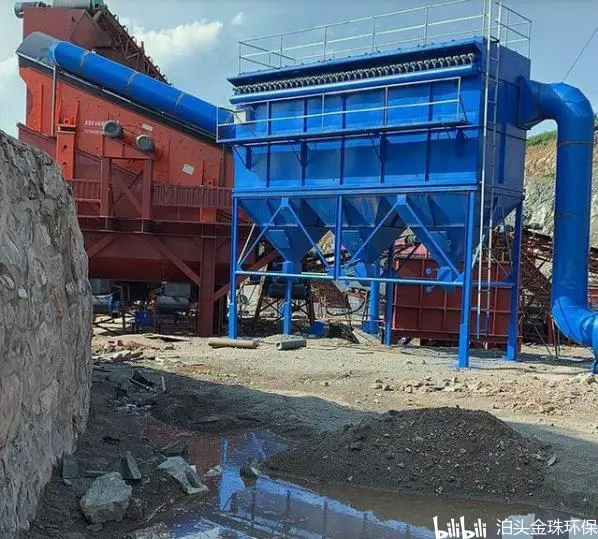
用脉冲清灰方式来清除袋式在工作时的集尘,由于脉冲清灰效率高,是被普遍认同、接受的一种成熟的清灰方式。相比其他方式的除尘器,脉冲清灰允许有相对较高的过滤风速,使除尘器占地面积、钢材耗量大大降低,降低了企业投资成本。
花板采用厚度为5mm的钢板,有加强筋,操作中有很强的抗弯折能力。花板孔的加工过程严格,满足精度要求,花板孔的切口处理也有极严格的工艺要求,确保花板和滤件完美地密合在一起。花板与壳体焊接在一起,杜绝粉尘漏过。
滤料采用美国BHA专利脉冲褶式滤袋过滤技术,该滤料选用纺黏聚酯滤料,独特连续长纤维粘压技术使此滤料形成许多均匀、致密的微细气流通道,其过滤效率极高;同时为表面过滤机理,能保持相对低的运行阻力, 处理风量显著增大。BHA脉冲褶式袋式材质刚性强,为一体化设计,一个褶式滤袋替代了常规滤袋和笼架等部件。同时该过滤材料抗潮性能好,强度高,清灰容易,使用寿命长, 基本上做到了除尘器的免维护。
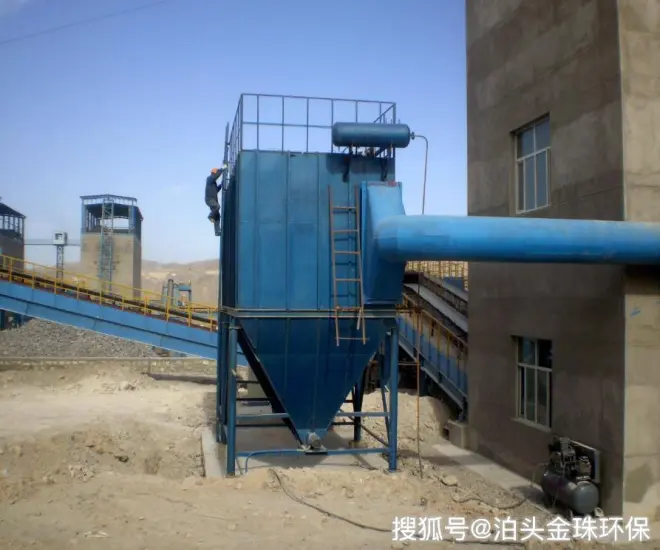
砂石厂除尘器的收尘原理:
当含尘气体由进风口进入灰斗后,一部分较粗尘粒在这里由于惯性碰撞、自然沉降等原因落入灰斗,大部分尘粒随气流上升进入袋室,经滤袋过滤后,尘粒被阻留在滤袋外侧,净化后的气体则由滤袋部进入箱体,再由阀板孔、出风口排入大气中,达到除尘的目的。随着过滤过程的不断进行,滤袋外侧的积尘逐渐增多,除尘器的运行阻力也逐渐增高,当阻力增到预先设定值(1200~1500Pa)时,清灰控制器发生信号,首先提升阀将阀板孔关闭,以切断过滤气流,停止过滤,然后电磁脉冲阀打开,以极短的时间(0.1秒左右)向箱体喷入压力为0.5~0.7MPa的压缩空气,压缩空气在箱体迅速膨胀,涌入滤袋部,使滤袋产生变形、抖动,加上逆气流的作用,滤袋外部的粉尘便被清除下来掉入灰斗,清灰完毕后,提升阀再次打开,除尘器又进入过滤工作状态。
上述的工作原理所表示的仅是一个室的情况,实际上气箱脉冲袋式除尘器是由多个室多排滤袋组成的,清灰时,各室分别按顺序进行,这就是分室离线清灰,其优点是清灰的室和正在过滤的室互不干扰,实现了长期连续作业。一个室从清灰开始到结束,称为一个清灰过程,清灰过程一般3~10秒,从第一个室的清灰结束,到第二个室的清灰开始,称为清灰间隔,清灰间隔的时间长短取决于烟气参数、选型的大小等,短则几十秒钟,长则几分钟甚至更长时间,清灰间隔又可分集中清灰间隔和均匀清灰间隔二种,所谓集中清灰间隔是指从第一室清灰开始到最后一个室清灰结束以后,所有室进入过滤状态,直至下一次清灰开始;而均匀清灰间隔则在最后一个室清灰结束以后,仍以间隔相同的时间启动第一室的清灰。因此均匀清灰间隔的清灰过程是连续不断的。从第一室的清灰过程开始到该室下一次的清灰过程开始之间的时间间隔,称为清灰周期,清灰周期的长短取决于清灰间隔时间的长短。
上述清灰动作均由进口西门子PLC全自动控制,清灰控制器有定时式和定压阻二种。定时式是根据除尘器阻力的变化情况,预置一个清灰间隔时间,除尘器按固定预置时间进行清灰,这种控制器结构简单,调试、维修方便,价格便宜,适用于工况条件比较稳定的场合。定阻式是在控制器部设置一个压力转换开关,通过设在除尘器上的测压孔测定除尘器的运行阻力,当达到清灰阻力时,压力转换开关便送出信号,启动清灰控制器进行清灰。
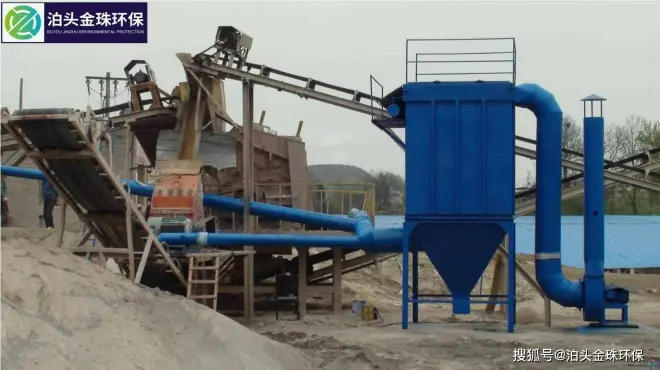