5条PFMEA开发经验,实践出真知!
1、PFMEA编写必须要有跨职能小组,并且需要获得企业管理层支持
企业当中最常见的问题就是把PFMEA仅仅当作APQP的一项交付文件,只是为了完成PPAP,没有把PFMEA当作公司的知识宝库。好多公司PFMEA就成了项目经理或者质量工程师一人的任务,甚至交由新到公司的相关人员负责,导致同一公司同一产品不同项目的PFMEA竟然有多处不一致。
PFMEA的编写需要一个跨职能小组来完成,至少包括质量、工程、制造、物流、采购等部门。
2、PFMEA提倡编写 master PFMEA
现在公司一般产品都是原材料经由几大功能块后生产完成的,因此鼓励供应商编写每个功能块的master PFMEA,如果投入足够多精力把MAETER PFMEA 建立好,有事半功倍作用。不仅有助于收集经验教训,而且可以作为产品、质量、生产制造等部门的培训资料,甚至可以用来做产线规划。
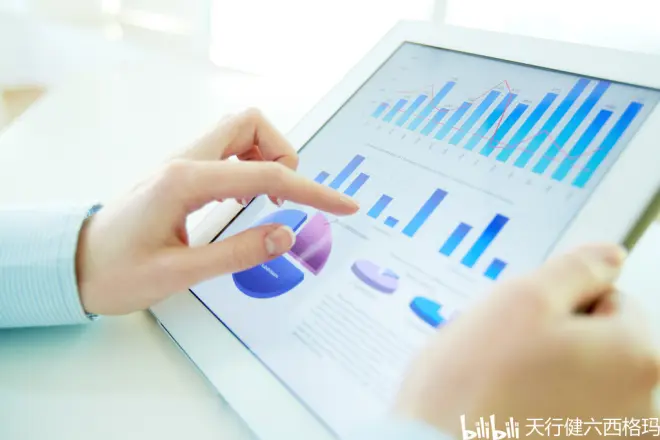
3、利用过程流程图识别所有需要制定PFMEA的过程
PFMEA分析一个假设是供应商来料或者上道工序来料OK,所以需要将全部过程都识别到,利用过程流程图是一个不错的方法。
特别强调的是,厂内来料检验、物流运输、最终出货、在线检验工位(氦检、气检、动平衡等)都需要制定PFMEA。
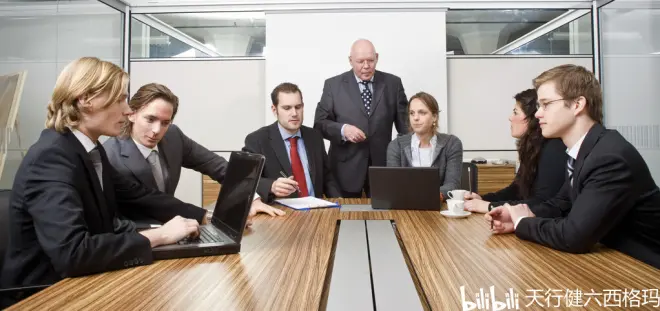
4、失效模式与严重度打分
分析好每一个要求以后,失效模式可直接理解为要求的反面,比如:要求是正确的螺钉,那失效模式就是不正确的螺钉。
来料检验这一步对应的失效模式是:漏检、检验结果不正确、检验出的NG件混入OK件、检验时损伤零件。
失效后果要考虑供应商自己厂内、主机厂、最终客户三个方面,将失效后果一一列出并依据打分规则逐一打分,选取最严重的一项作为此项的严重度。需要强调的是,打分需要遵循打分规则,不可拍脑袋决定。
另外在此处需要结合DFMEA,可参照DFMEA里给出的严重度进行打分。
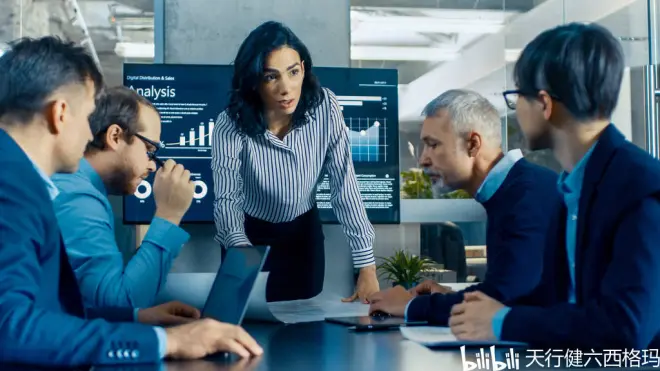
5、结合预防措施进行频度打分
频度打分的依据是失效发生次数,这就需要统计本工位、终检工位、主机厂、最终客户四处的失效次数,但很多时候我们没法拿到这么多数据,在此种情况下,可以使用频度4或5,不可以再低。
频度1适用情况为从设计上避免了此种缺陷;频度2适用于,现场有预防措施,防止此种失效模式发生(注意不是防止失效模式产生的后果发生)