7075铝合金挤压棒材表面起泡的原因分析
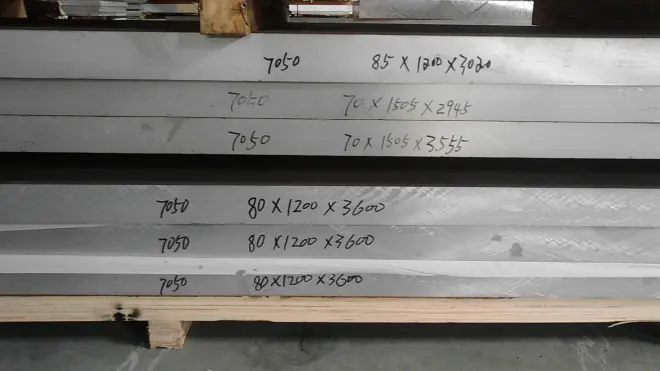
摘要:采用正交试验对7075铝合金挤压棒材表面起泡的原因进行了分析。结果表明:7075铝合金挤压棒材表面起泡主要来源于挤压过程中挤入的气体和夹杂。另外。固溶热处理不当会促进表面成层缺陷处产生气泡。通过优化挤压工艺和模具导流腔设计可消除挤压棒材的表面起泡,降低固溶加热炉内水汽含量并采用合理的热处理工艺可避免淬火后棒材表面起泡。
关键词:7075铝合金;挤压棒材;表面起泡;淬火
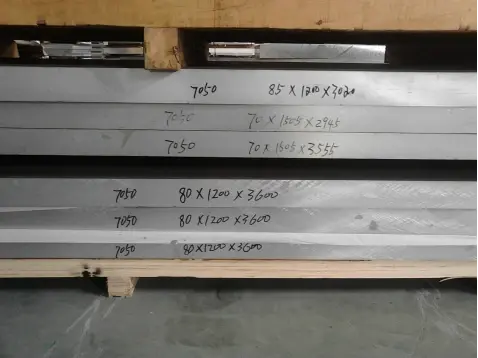
气泡是高强铝合金(如7075)挤压生产中的一个比较常见的缺陷,目前国内外学者对不同挤压产品表面气泡的形成有不同观点,王凤春将2A14铝合金棒材表面气泡分为夹杂气泡、挤压分层气泡和气体渗透性气泡三类,认为夹杂气泡占绝大多数。生产中严格控制夹杂物带入可以防止气泡的产生。程勇胜等网研究2017铝合金退火棒材表面起泡的原因时,认为气泡是起源于成层缺陷的夹杂型表面起泡,合理选择挤压工具和模具,提高工模具表面质量可以减少或消除气泡。PradipKSaha在分析7075薄壁型材气泡产生的原因时,认为气泡的形成主要是来自铝合金内部和外部的氢原子或离子在夹杂物周围沉淀聚集,形成氢气泡,热处理过程能促进氢气的膨胀,控制合金内、外部氢的来源能够减少或者消除固溶热处理过程中形成气泡的几率。崔景博等认为成层、高温氧化或过烧都能引起7A04铝合金产品起泡.通过分析金相组织可以判定具体的起泡原因。关于7075铝合金挤压棒材表面起泡的问题,目前报道较少。本文采用正交试验的方法,研究不同挤压工艺参数、模具设计和热处理工艺对气泡的影响,找出气泡形成的工艺因素并提出合理的解决方案,能够有效避免气泡的产生,提高棒材成品率。
1、气泡的形貌和分布
我公司生产的7075铝合金挤压棒材。挤压后出现连续分布的表面气泡,主要集中在棒材头部;淬火后气泡增多,沿挤压方向呈连续分布于整个挤压长度上。且头部单位面积气泡数量比尾部多,大小约1~2mm.其典型照片如图1所示。
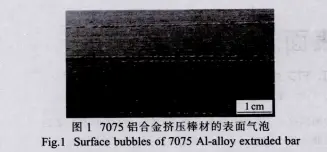
2、试验方法和结果
在试验之前,通过初步分析可能导致表面起泡的因素。分别选取了不同的挤压工艺、模具设计和热处理工艺进行试验。所用铸锭为采用半连续铸造法生产的同一批次、同一热处理炉次的去皮铸锭,并严格控制铸造前铝液中H含量低于0.10ml/lO0gAl,其化学成分见表1。根据单位面积表面气泡的数量和大小。将棒材的表面质量分为l0个等级:1级无气泡,10级气泡最严重。
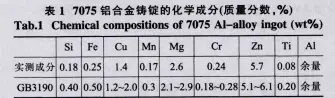
2.1挤压工艺的影响
采用正交试验方法,分析不同的锭筒温差、压余长度和镦粗排气压力对φl00mm棒材挤压后表面起泡的影响。试验在75MN(φ460mm挤压筒)正向挤压机进行,为了减少试验过程中其他因素引起的噪声干扰.除了作为变量的三个因素外,其余挤压参数相同:铸锭直径448mill,长度1000mnl,铸锭头部温度410℃,梯度15℃/m,模具温度430℃,挤压速度lm/min,挤压比21,模具采用小导流设计,每组试验挤压3根铸锭。
表2为挤压工艺因素和试验结果。表2中,镦粗压力54MN和27MN对应的挤压垫所受压强分别为325MPa和162.5MPa:锭筒温差=铸锭头部温度一挤压筒温度;压余长度为上一根铸锭的设定值。
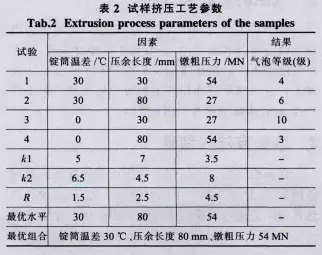
2.2模具设计的影响
本试验同样在75MN(φ460mm挤压筒)正向挤压机进行.模具分别采用大导流、小导流和小导流加防倒槽三种设计方案,模具结构简图见图2,分析不同的模具设计对挤压后棒材表面起泡的影响。挤压工艺采用表2中正交试验结果的最优组合,即:锭筒温差30℃、压余长度80mm、镦粗压力54MN,其余挤压参数与2.1节相同,每个试验挤压3根棒材,其中22(表3)采用表1中试验4的结果(条件相同)。
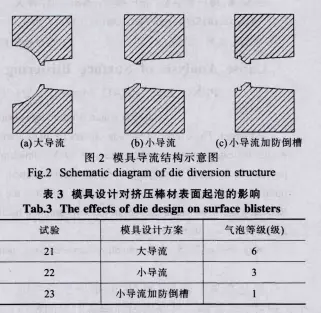
2.3固溶淬火工艺的影响
本试验在20m立式淬火炉中进行.采用正交试验的方法,分析不同加热温度、保温时间和空炉装料温度对棒材固溶淬火后表面起泡的影响。试验样品采用第22、23号试验生产的没有表面起泡的棒材,对淬火样品进行120℃x24h的人工时效后,用万能电子试验机进行拉伸测试。
3分析讨论
3.1挤压工艺的影响
从表2的结果可以看出,挤压工艺的三个因素对表面气泡都有影响,其中镦粗压力影响最大,其次是压余长度,锭筒温差也有一定影响。由于7075铝合金变形抗力大,如果采用和6XXX系铝合金同样的镦粗压力(27MN),不足以使金属完全变形填满整个挤压筒,在排气过程中不能将简内气体完全排放,在挤压过程中气体被挤入制品表层形成表面气泡。压余太短时,接近挤压终了的金属紊流阶段,金属死区的杂质、氧化皮等被挤入制品表面,或被挤入模具内导致挤压下一根制品时,在制品表面形成成层缺陷,气体在成层缺陷处聚集形成表面气泡。筒温低于锭温时(锭筒温差>O),与挤压筒之间的传热效应,铸锭的内部温度高于表面温度,挤压时铸锭内部流动性好于表面.表面杂质、氧化皮等不易被挤入模具:当锭筒温差变小或为负时,铸锭表面的流动性变好,表面的杂质、氧化皮等容易被挤入模具。但由于挤压筒内衬的温度升降速度较慢,在同一批次挤压过程中改变筒温对汽泡的影响相对较小。因此,选取合适的镦粗压力、压余长度、锭筒温度等挤压参数可以减少或消除挤压态棒材的表面气泡。
3.2模具设计的影响
棒材模具分为有导流和无导流模.有导流模具的优点是挤出后棒材连着上一根,可以提高生产效率。但有导流模最大的缺点是上一根铸锭残留在导流腔内的金属,在挤压时会被挤入下一根产品表面产生成层缺陷,导流越大则缺陷越明显,因此,减少导流大小可以改善成层缺陷.减少因成层缺陷产生的气泡。同时,由于7075铝合金变形抗力大,在切压余时导流入口上部的金属容易被拉出而形成空洞(如图3箭头所示),在挤压下一根铸锭时,空洞处的气体被挤入下一根产品表面形成气泡。导流越大则空洞越明显,在导流入口附近加上一圈防倒槽时.可以减少或避免因切压余造成空洞引起的棒材表面气泡。
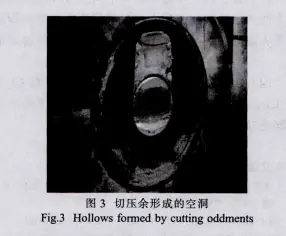
3.3固溶淬火工艺的影响
从表4可知,空炉装料温度对气泡影响最大,其次是保温时间,加热温度对气泡无影响。热处理过程产生的表面气泡与铝合金内部或外部的氢有关,内部的氢为铝合金在铸造过程中所吸收,外部的氢为铝合金在高温、高湿的环境下与水分子反应所释放出。内部的氢在挤压过程的高压作用下迁移到成层缺陷的夹杂物内部.外部的氢则以离子或者原子形式扩散到棒材夹杂物周围沉淀聚集。在热处理过程中氢离子或原子随着夹杂物继续迁移,当晶格畸变能减到最小时.沉淀聚集的氢原子在夹杂物中重组成氢气而不能溢出.同时氢气受热膨胀.扩大所在夹杂物的空腔而形成表面气泡。由于在熔铸过程中严格控制了氢含量.因此氢主要来源于外部。炉内湿度越大则越容易反应产生氢,表面气泡也越严重,而热炉装料能保证炉内干燥,因此空炉温度对气泡影响最大。氢的扩散速度主要受温度、时间的影响,试验中两组温度相差较小,对气泡的影响并未体现出来,保温时间相差较大,对气泡的影响也相对较大。因此,不合适的固溶处理能够促进表面成层缺陷处产生气泡。
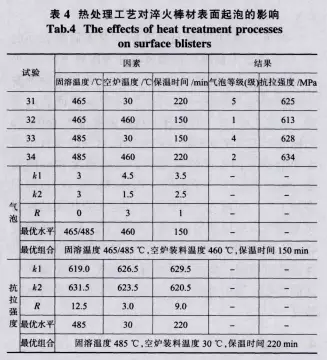
从表4还可看出,对力学性能的影响程度依次为固溶温度、保温时间和空炉装料温度。在过烧温度以下保温温度越高、保温时间越长则固溶程度越高,时效后的抗拉强度越大。试验中的温度为炉气温度,热炉装料对应的炉内总时间比冷炉装料少了炉气升温时间,即金属实际保温时间变短,因此也对力学性能有一定影响,在实际生产中热炉装料时要进行相应的炉气保温时间补偿。采用热炉装料、高温短时间的固溶淬火工艺可以有效防止表面气泡的产生。由于当前7075棒材存在的主要矛盾是表面起泡,抗拉强度方面则因性能过剩降为次要矛盾,如果表面气泡和抗拉强度出现相对立时,可以在标准要求范围内适当牺牲一定的抗拉强度以保证表面质量。从表4可知,所有试样的抗拉强度都比560MPa的标准要求高出9.5%~13.2%.而对气泡和抗拉强度影响最大的因素分别是空炉装料温度和固溶温度,因此,实际生产中应优先选择热炉装料、高温固溶的工艺,而对气泡和抗拉强度起次要作用的保温时间则可以相应缩短。即最优组合工艺为:固溶温度485℃,空炉装料温度460℃,保温时间150min,可保证在抗拉强度满足标准要求的前提下避免表面气泡的产生,该组合在后续的批量化生产中也得到了验证。
4结论
(1)7075铝合金挤压棒材的表面气泡起源于挤压过程带入的气体或杂质.不合适的固溶处理能够促进表面成层缺陷处产生气泡。
(2)避免挤压棒材表面气泡的关键是减少气体或杂质被挤入。采用小导流加防倒槽的模具设计,同时选取合适的镦粗压力、压余长度、锭筒温度等挤压参数可以减少或消除挤压态棒材的表面气泡。
(3)淬火后表面起泡与炉内气氛和热处理参数有关,采用热炉装料、高温短时间的固溶淬火工艺可以有效防止表面气泡的产生。